A mázolómunkákhoz felhasznált lakkok, festékanyagok, oldószerek, hígítók stb. jelentős része tűz- és robbanásveszélyes. Több közülük rejtett veszélyforrást képez. A tűzvédelmi óvintézkedéseket a területileg illetékes tűzrendészeti hatóság a helyi viszonyoknak megfelelően egyértelműen előírja, így az abban foglaltak maradéktalan betartásával a veszélyforrások megszüntethetők. A továbbiakban néhány olyan rejtett veszélyforrást kell megemlíteni, amelyeket kevésbé ismernek vagy helytelenül alábecsülnek. Ezek röviden összegezve a következők.
Bizonyos anyagok védelme az öngyulladástól
A lenolajkence, a zsíros hígító, az olajfestékek és esetleg egyes oxigénfelvétellel száradó zománcfestékek oxidációja (száradási folyamat) olyan heves lehet, hogy nagy fajlagos felületű anyagokkal érintkezve (pl. törlőruha, fűrészpor, faforgács, papír stb.) öngyulladást idézhetnek elő. Ezt a közvetlen napsugárzás vagy a hőforrások elősegíthetik. Emiatt kellemetlen, rejtett tűzveszélyforrást jelentenek.
Heves öngyulladás veszélye
Sokkal hevesebb öngyulladást idézhetnek elő a telítetlen poliésztergyanták szerves peroxid katalizátorai, a kobaltnaftenát alapú gyorsítókkal érintkezve. Bár ezeket közvetlenül a mázolási munkákhoz alig használják, de mégis számításba jöhetnek pl. gyorsjavító tapaszok alakjában. Ritkábban, de előfordulhatnak olyan esetek is, hogy a térhálósítóval nem az előírt arányban elegyített epoximűgyanták erős felmelegedéssel térhálósodnak, s emiatt öngyulladás jöhet létre.
Egyéb veszélyforrások
Hasonló veszélyforrást képez a klórmész, a HYPO, szerves anyagokkal érintkezve, a beszáradt fakorhadásgátló szer, bár ez utóbbi már csak elvétve használatos.
Robbanásveszély
Súlyos robbanást idézhetnek elő az alumíniumpigment paszták vízüveges keverésnél, továbbá a hőálló ezüst beszáradt dobozai pl. lúgos maratásnál, esetleg a cinkporos alapú, korrózió ellen védő alapozók, ha az edénybe – hiányos elzárás miatt – vízgőz, lecsapódott pára kerül. Mindegyik esetben hidrogéngáz fejlődik (jelentős hőképződéssel), amely robbanáshoz vezet.
Tűz- és robbanásveszély
A tűz- és robbanásveszélyes oldószereket tartalmazó lakkok, festékek felhasználásakor biztonságtechnikai szempontból elsősorban arra kell ügyelni, hogy a munkatérben töménységük (cmax) ne érje el a jellemző alsó robbanási határt (ra), ill. biztonsági tényezővel csökkentett értékét (általában 1/5-ét). A mázolómunkákhoz használt oldószerek, hígítók alsó robbanási határtöménysége viszonylag csekély, 1,1-5,0 térfogatszázalék, ezért különösen kisméretű műhelyekben, munkaterekben nagyobb az oldószergőzök robbanásveszélye.
E veszélyforrás ellen légcsere növelésével (természetes vagy mesterséges szellőztetéssel), kevés, ill. helyesen felmért anyagmennyiség felhasználásával, végül oldószermentes vagy oldószerszegény festékanyagokkal lehet védekezni. Jó megközelítéssel ui. felbecsülhető az az oldószer-hígító, ill. lakk- vagy festékanyag-mennyiség, amely egy adott méretű munkatérben, légcsere figyelembevételével felhasználható. Oldószeres festékanyagok felhasználásakor a „légáramlási holtterek “-ben az oldószergőzök helyi feldúsulása fordulhat elő, ami szintén robbanáshoz vezethet.
Gyújtószikra keletkezésének veszélye
Külön fel kell hívni a figyelmet az elektrosztatikus feltöltődés következtében létrejött, viszonylag nagy energiatartalmú gyújtószikrákra, amelyek már több robbanás előidézői voltak. Közismert, hogy a műanyagok, a festékbevonatok (pl. faszerkezeteken), a műszálas ruházatok, de maga ez emberi haj (száraz állapotban) is igen hajlamos szikrakisülések létrehozására, de ezt a körülményt általában alábecsülik. A villamos kapcsolók és gépi berendezések szikraképződései már ismertebbek.
Tűzvédelem fontosságának tudatosítása
Mivel a tűz elleni védelem társadalmi közügy, az ellene való védekezést gondosan meg kell szervezni, és jelentőségét tudatosítani kell.
Tűzvédelmi terv vállalatok, szövetkezetek stb. esetében
A helyi, esetleg változó építéshelyi körülményekre, pontosan előírt tűzvédelmi munkatervet kell készíteni, az illetékes tűzrendészeti hatóság helyszíni szemle alapján elrendelt utasítása szerint.
Környezetvédelmi teendők
A mázolómunkák során felhasznált mérgező hatású, gyakran bűzös, kellemetlen szagú anyagok, továbbá az egyes zajos, szennyeződéssel, porképződéssel járó munkafolyamatok (pl. szemcseszórásos rozsdamentesítés, festékrétegek égetéssel, maratással való eltávolítása, festékszórás stb.) ún. környezetszennyező tényezőként jelentkeznek.
A következő általános környezetvédelmi teendőket kell foganatosítani a mázoló- (és azt kiegészítő egyéb) munkák során:
- A közterületet, élővizeket, talajt stb. oldószeres és mérgező festék¬anyagokkal szennyezni nem szabad. Szigorúan tilos – bármilyen csekély mennyiségben is – oldószereket, hígítókat, festékanyagokat közvetlenül a szenny¬vízcsatornába vagy az azzal összeköttetésben álló lefolyónyílásokba táplálni.
- Ugyanígy szigorúan tilos az ilyen anyagokat szeméttároló edényekben, szemétlerakóhelyeken gyűjteni, annál is inkább, mert öngyulladást, tüzet és robbanást idézhetnek elő. Oldószereket és ezeket tartalmazó festékanyagokat kizárólag az arra kijelölt tárolóhelyeken kell összegyűjteni és előírás szerint megsemmisíteni.
- Értelem szerint ugyanígy kell eljárni természetesen a savas és lúgos, maró hatású anyagok (pl. vegyi rozsdamentesítők, lúgos festéklemarató szerek stb.) felhasználásakor is, azzal az eltéréssel, hogy kis tömegű felhasználásuk esetében semlegesítve, bő vizes öblítéssel, vagyis az előírt hígítás után a szenny¬vízlevezető csatornákba táplálhatok.
Mázolási munkák – Balesetelhárítás, egészségvédelem, környezetvédelem
A mázolási munkák során sokkal több tűz- és robbanásveszélyes, mérgező hatású anyagot kell felhasználni, továbbá veszélyesebb gépi berendezéseket és segédeszközöket üzemeltetni, mint a festés esetében. Ennek figyelembevételével, röviden csak a falfestőmunkáktól eltérő jellegű körülményeket kell megemlíteni.
Balesetelhárítás, munkavédelem
A mázolómunkáknál a következő általános munkavédelmi óvintézkedéseket kell foganatosítani.
Általános munkavédelem:
- A helyi (építéshelyi) körülmények előzetes gondos felmérésével a baleseti veszélyforrásokat meg kell szüntetni (pl. a munkaterület körülhatárolásával, védőkorlátok létesítésével, a rend, áttekinthetőség biztosításával stb.).
- A kézi szerszámok, gépi berendezések, villamos készülékek feleljenek meg az erre vonatkozó szabványok biztonságtechnikai, villamos érintésvédelmi előírásainak, ezek rendszeres, folyamatos ellenőrzéséről gondoskodni kell.
- Ugyanígy biztosítani kell a szabványelőírásoknak megfelelő minőségű egyéni védőeszközök (pl. védőszemüveg, arcvédőlemez, munkaruha, gumikesztyű stb.) használatát, az egyes munkaműveletek megkövetelte feltételek szerint.
- A mázolást és a kiegészítő tevékenységet végző dolgozókat rendszeres, folyamatos munkavédelmi oktatásban kell részesíteni (a helyi, változó munkahelyi körülmények figyelembevételével), s ennek fontos társadalmi jelentőségét állandóan tudatosítani kell.
- Egyéb vonatkozásban a tűzrendészeti, egészség-, ill. környezetvédelmi általános feltételeket is biztosítani kell.
Egészségvédelmi óvintézkedések
Mázolómunkáknál – a nagyszámú vegyi termék felhasználása miatt – elsősorban kemizációs eredetű vegyi ártalmakkal lehet számolni. Az ezek elleni védekezés azonban a jelenlegi technikai színvonalon teljes megbízhatósággal megoldható. Néhány ilyen jellegű veszélyforrás a következő.
Acélszerkezetek (hidak, ipari csarnokok stb.)
Mázolás előtti felület-előkészítésükkor az ólomtartalmú, régi festékréteg eltávolításánál fennállhat az ólommérgezés veszélye. Ugyanígy a szemcseszórásos rozsdamentesítés esetén a szilikózisveszélyt is számításba kell venni. Megfelelő zárt rendszerű védőruhás álarc és helyi elszívással ellátott szívóberendezések kielégítő védelmet nyújtanak.
Acél-, fém- és faszerkezetek stb.
Mázolásukkor az ólomkróm-, mangán-, esetleg más mérgező hatású pigmentek jelenlétével számolni lehet. Igen helytelenül terjedt el a szakmai gyakorlatban a cink-kromátos, cinktetroxikromátos alapozók szívóeljárásos felhordása. Utóbbiak ui. még az ólomnál is nagyobb mérgezési veszélyforrást jelentenek.
Szóróeljárás
Ez esetben- még ólom- és más mérgező pigmentektől mentes festékek főleg szórással való felhordásakor is – fennállhat az ólom-, sőt a veszélyesebb mangánmérgezés lehetősége! Ennek az az oka, hogy a kb. 1-3% szárítóadalékok (szikkatívok) ólom-, mangán- és kobalttartalmúak, s ezek a szervezetben igen gyorsan felszívódhatnak.
Lakkbenzin, terpentin és más oldószerek és hígítók
Az összes oldószer és hígító – de különösen a benzolhomológ-tartalmúak (pl. nitrohígítók, parkettalakk-hígítók stb.) – erősen bódító és mérgező hatásúak, s főleg szórással való felhordásnál lehet nagy a mérgezés veszélye. Ezek ellen légcserével, helyi légelszívással, tisztalevegős légzőkészülékkel stb. lehet védekezni. Különösen zárt térben (pl. tartályok belsejében) végzett munkáknál kell arra ügyelni, hogy a munkatérben az emberi szervezetre ártalmas oldószergőzök és más szennyező (vegyi) anyagok töménysége ne haladja meg a felső határértéket.
Lakkok
Egyes lakkok esetében (pl. a savra keményedő amingyantás lakkoknál) az oldószergőzökön kívül egyéb veszélyes mérgező hatású melléktermékek, pl. formaldehidgáz (amelyből a megengedett felső határtöménysége csak 1 mg/m3!) kerülnek a munkatérbe.
Zártabb, rosszul levegőző műhelyek
Ilyen helyiségekben (pl. pincehelyiségben) olaj- és egyes oxidatív úton száradó zománcfestékek száradási folyamata egyrészt jelentős oxigénfogyasztással jár, másrészt szén-monoxidot (CO) juttatnak a munkatérbe, és így ott veszélyes szennyezettségű légtér alakulhat ki. (Ez esetleg állandó fejfájást, rosszullétet okozhat.)
Faszerkezetek felületvédelme
Faszerkezetek felületvédelmére használatos gomba- és rovarmentesítők, korhadást gátló szerek mérgező hatásával is számolni kell. Ugyanez áll fenn egyes lángmentesítő szerek esetében is.
Fémszerkezetek zsírtalanítása
Ezen tevékenység során esetleg mérgező hatású oldószereket (klórozott szénhidrogéneket, pl. széntetrakloridot, triklóretilént stb.) és maró hatású anyagokat is használnak. A klórozott szénhidrogéneket kizárólag zárt rendszerben szabad használni. Oldószeres zsírtalanítás (amelynek eredménye műszaki szempontból is vitatható) helyett ma már kiváló, ártalmatlan mosószerek is alkalmazhatók.
Régi festékrétegek eltávolításánál a következő veszélyforrásokkal lehet számolni:
- lúgos maratóknál: tömény lúgoldatok (pl. marónátron, szóda-f oltott mész, trisó stb.) maró hatás és fokozott csúszásveszély;
- égetéssel való eltávolításnál a foltbenzin, továbbá a kifejezett mérgező hatású légszennyező anyagok, így elsősorban szén-monoxid, benzingőz, akrolein, formaldehid stb. kerülnek a légtérbe. Zártabb munkatérben fokozottabb légszellőzésre van szükség.
Az előbbieken túlmenően egyéb veszélyforrásokkal is lehet számolni
Általános elvként törekedni kell a mérgező hatású oldószeres festékek helyett teljesen veszélytelen, oldószermentes festékanyagok, esetleg vizes diszperziós festékek felhasználására (pl. faszerkezetek mázolásához). Ily módon az előbbi veszélyforrások jelentős mértékben csökkenthetők.
A mázolási munkák előtervezése, minőség-ellenőrzése
A mázolási munka megkezdése előtt a következő kiindulási adatok, ill. tényezők ismeretesek.
Ezek a tényezők:
- alap anyaga (fa, acél, beton, vakolat, azbesztcement stb.),
- az alapfelület régi (szennyezett) vagy új (és ennek megfelelően szennyezett),
- igénybevétel (pl. beltéri, száraz, kültéri, vegyi stb.),
- a védőbevonat jellege (színtelen lakkozás, fedőmázolás, színdinamikai igények).
Az alap anyaga jelentős mértékben meghatározza a számításba vehető festék-, ill. lakk-választékot, a felület-előkészítő műveleteket (pl. pórustelítő kezelés, vegyi stabilizáló kezelés, rozsdamentesítés, tapadásjavító felületkezelés stb.). Az alapfelület lehet régi és új. Első esetben felmerülhet a már lehámlásra hajlamos, régi festékréteg, lakkbevonat eltávolítása. Az alap anyaga és kora együtt szabja meg végérvényesen a felületelőkészítés (mint egyik legfontosabb mázolási alapművelet!) munkaműveleteit és az elvégzendő feladatokat.
Az igénybevétel még inkább körülhatárolja a számításba vehető anyagválasztékot, a jelleg pedig már egyértelműen meghatározza. A továbbiakban, a fajlagos anyagfelhasználási adatok ismeretében, az anyagszükségletet pontosan ki lehet számítani. Ezek után már csak a kivitelezési részletkérdések maradnak hátra, azaz, hogy gépi erővel, kézi mázolással (pl. ecseteléssel, hengerezéssel stb.) célszerű-e elvégezni a munkaműveleteket.
Minőségellenőrzés
A mázolómunkák minőségi követelményei
Hogy ha egy korrózió ellen védő bevonat nem tölti be funkcióját és nem tanúsít nagy ellenálló képességet, akkor előállítási költségénél sokkal nagyobb kárösszeggel és biztonságtechnikai hiányosságokkal, sőt súlyos baleseti forrásokkal kell számolni!
A minőségi hibákat előidéző okok
A mázolómunkák e hibaforrásainak okai azonban egyrészt nagyobb számban jelentkeznek, másrészt bonyolultabbak, ill. szerteágazóbbak lehetnek. Röviden áttekintve ezek a következő változatokban összegezhetők.
Anyaghibák (a felhasznált festékanyagok, segédanyagok stb. nem megfelelő minőségűek)
Nem sorolhatók ide azok az esetek, amikor adott rendeltetési célra (igénybevételre) nem alkalmas anyagokat választottak ki, vagy az anyagok esetleg helytelen tárolás elszennyeződés stb. következtében káros átalakulást szenvedtek.
Tervezési hibák
Adott rendeltetési célra nem a legalkalmasabb festékanyagok előírása, vagy a környezeti károsító tényezők helytelen felmérése vagy alábecsülése.
Kivitelezési hibák:
- a tervezési hiba kifogásolásának elmulasztása a kivitelező részéről;
- előírt munkaműveletek elhagyása, vagy nem megfelelő elvégzése;
- hiányos, nem kielégítő felület-előkészítés (pl. rozsdamentesítés) vagy anyag-előkészítés (pl. túlzott mértékű hígítás);
- az előírt környezeti, légköri és egyéb technológiai feltételek mellőzése (pl. hideg, csapadékos időben kültéri acélszerkezet alapozó mázolása);
- nem megfelelő kéziszerszámok, gépek, segédeszközök használata;
- a festékbevonat kialakítása közbeni esetleges károsodás, környezetszennyezés vagy más építési munkák stb. következtében (munkaszervezési hiba, kellő körültekintés hiánya stb.);
- egyéb hasonlójellegű, összetett hibaforrások.
Előre nem felbecsülhető, elháríthatatlan hibák
Körültekintő, szervezett munkák esetén ezek szinte eleve kizártak. Előfordulhat azonban olyan rejtett hibaforrás, aminek a következtében egy mesterséges szerkezeti anyag (pl. faforgácslemez, farost, azbesztcement stb.) utólag károsodik, s ennek során a lakk- vagy festékbevonat-rendszer részben vagy teljesen tönkremegy. (Éppen ezért a még nem teljesen ismert, új szerkezeti anyagok festéstechnikai jellemzőit előzetesen gondosan tisztázni kell!)
A minőségi hibák javítási lehetőségei
Általános szempont, hogy a minőségi hibák csak abban az esetben tekinthetők javíthatóknak, ha
- további károsodás vagy meghibásodás veszélyét nem rejtik magukban,
- teljes értékű állagvédelmet nyújtanak,
- kihangsúlyozott, kiemelő hatású esztétikai igényt nem rontanak le zavaró mértékben. Egyedül ebben a vonatkozásban tehetők engedmények.
A lakk- és festékbevonat-rendszerek ápolása, karbantartása
Bármilyen szokatlannak is tűnik, de a mázolási munka befejeztével az azt végző vállalatnak, iparos mesternek kötelességszerűen kezelési (ápolási, karbantartási) utasítást (tájékoztatót) kell adni a megrendelőnek. A szakmai alaposságon túlmenően, ezt éppen a mázolás – mint egyik legelterjedtebb korrózió ellen védő megoldás – fontos szerepe indokolja. (Pl. gépkocsik esetében ezt már régóta gyakorolják.)
Elő kell írni, hogy:
- milyen hatásoknak nem szabad kitenni a védőbevonatot;
- milyen vegyi jellegű vagy egyéb ápolószereket szabad felhasználni a tisztításra stb.;
- esetleg milyen kezeléssel, ápolással nyújtható meg a bevonat élettartama, amely végső soron fontos társadalmi érdek, bárhol is készült a védőbevonat.
A mázolómunkák technológiája, szennyeződések eltávolítása
A mázolás munkaműveletei és értelmezésük
Mázolási munkákon a felület előkészítésétől az átvonó festékréteg felhordásáig, esetleg az azt követő utókezelésig terjedő műveletek összességét értik.
A szükséges technológiai műveletek kiválasztása és elvégzése elsősorban:
- a felület jellegétől (fa, fém, vakolat stb.),
- a felület szennyeződésétől (pl. oxidréteg, zsír, olaj stb.),
- a felület felületi érdességétől,
- a kialakítandó festékbevonat-rendszer rendeltetésétől, igénybevételétől, felépítésétől és a hozzá használatos anyagok tulajdonságaitól,
- a felület környezeti, ill. légköri adottságaitól és egyéb műszaki, gazdaságossági, egészségvédelmi stb. tényezőktől függ.
Mechanikai szennyeződések eltávolítása
A szennyeződések és a felület jellegétől függően, kaparószerszámokkal, kalapáccsal, spatulyával, drótkefével stb. történik. Lényegében ez az előtisztítás.
Oxidmentesítés
Ez a művelet a fém-, elsősorban az acélszerkezetek felületén a megmunkálás (pl. hengerlés) és a környező vegyi hatások okozta oxid-, rozsda-, reveréteg stb. eltávolítását jelenti. Acél- és fémfelületeken ez a művelet az egyik legfontosabb munkafolyamat, mely a mázolás élettartamát, tartósságát elsősorban befolyásolja. A korszerű mázolási munkáknál – a technológiai fegyelem betartása érdekében – igen fontos az acélszerkezetek felületi tisztaságának ilyen szempontból való egyértelmű jellemzése.
Portalanítás
Az ismert módszerekkel porolóecsettel, esetleg sűrített levegőfúvással vagy elszívással (porszívóval) végezhető.
Zsírtalanítás
A felület zsiradék szennyeződéseinek eltávolítását a gyakorlatban rendszerint oldószeres lemosással, ecseteléssel végzik. Itt az ecsetszőrök mechanikai koptató hatása is előnyösen érvényesül. Kizárólag ártalmatlanabb oldószereket (pl. lakkbenzin, foltbenzin, esetleg szolventnafta stb.) szabad használni.
Az erősen mérgező, bőrön keresztül is felszívódó oldószerek (pl. klórozott szénhidrogének, benzolhomológok stb.) zárt térben csak elszívás esetén használhatók. A zsírtalanítás végezhető még égetéssel, különféle emulziós készítményekkel, sőt újabban ultrahanggal is. Fafelületek zsírtalanítása általában nem szükséges. A felszínre tört gyantacsomókat azonban oldószeres kezeléssel (célszerűen aceton, denaturált szesz és xilol 3:3:1 arányú elegyével) el kell távolítani. Farostlemezek esetében a zsiradékfoltok eltávolítása már gyakrabban felmerül.
Vegyi felületkezelés
A vegyi felületkezelő – az anyag tulajdonságaitól függően – legcélszerűbben ecseteléssel, ritkábban merítéssel hordható fel, de szórással nem. Kivételt képezhetnek egyes olyan felületkezelők, amelyek az alapra vegyi hatást nem fejtenek ki. Ezek azonban nem tekinthetők vegyi felületkezelőknek.
Fapácok, lazúr bevonatok felhordása
Elsősorban ecseteléssel, ritkábban szóróeljárással vagy merítéssel (mártó eljárással) végezhető, az anyagok tulajdonságaitól függő előkészítő műveletek (pl. hígítás, egyneműsítés, egyes alkotórészek súlyarányok szerinti összekeverése stb.) elvégzése után.
Savas oxidmentesítés
A savas oldat felületre való ecsetelésével, locsolásával, ill. kisebb méretű tárgyak savas oldatba merítésével végezhető el. Savas oxidmentesítés után a felületet enyhén lúgos, majd tiszta vizes leöblítéssel semlegesíteni kell.
Lúgos előkezelés
Célja nemcsak zsírtalanítás, hanem egyes fémek esetén (pl. alumínium és ötvözetei, horgany stb.) a felület enyhe maratása az alapozóréteg számára kedvezőbb tapadófelület létrehozása is lehet.
Pórustömítés
A durva pórusú fák felületét – a rajzolatok kiemelésére – spatulyával pórustömítő tapasszal húzzák át, s így a pórusokat tömítik. (Legtöbb esetben díszítő hatású célzattal; ritkán a falfelületek pórusait is hasonló módon szokták tömíteni.)
Pórustömítő telítés, ill. beeresztés (átitatás, impregnálás)
A fa-, fal- és egyéb pórusos anyagok felületeit megfelelő hígfolyós készítményekkel, javarészt ecseteléssel, esetleg merítéssel itatják át, a felületi pórusok telítése céljából.
Alapozó mázolás
A beeresztett (impregnált) vagy előkezelt felülettel (alappal) közvetlenül érintkező első festékréteg felhordásának művelete. A kedvezőbb tapadás érdekében kizárólag ecseteléssel végezhető. Díszítő jellegű vagy ideiglenes védelmet nyújtó alapozó mázolás azonban szórással, merítéssel stb. is elkészíthető.
Tapaszolás
A felületi egyenlőtlenségek, pórusok, folytonossági hiányok kitöltése e célra készített anyagokkal. A tapaszréteg kenőkéssel (spatulyával, spachtlival) és szórópisztollyal alakítható ki. Első esetben vajszerű állapotú (kenőtapaszt), a másodiknál sűrűn folyó, festékszuszpenzióhoz hasonló megjelenésű, szórótapaszt (fröccskitt) használnak – a felület tulajdonságaitól és a környezeti adottságoktól függően.
Csiszolás
Az alapfelület, a tapasz- vagy festékrétegek kiálló felületi egyenlőtlenségeinek csiszolóanyagokkal való lekoptatása.
Rendeltetését illetően a csiszolás a következőképpen csoportosítható:
- a síkból kiálló felületi egyenlőtlenségek (szemcsék stb.) lekoptatása, egyenletes, sík felület kialakítása céljából;
- az egyes rétegek felületi felérdesítése, összekarcolása a bevonatok tapadásának elősegítésére;
- Az átvonó réteg fényező (vagy finom) csiszolása, ill. polírozása.
Közbenső rétegek felhordása
Az alapozó és átvonó réteg között egy közbenső réteget kell képezni. Ez ecseteléssel és szórással egyaránt kialakítható, a lakk- vagy festékanyag jellegétől függően.
Az átvonó (tehát a legkülső) réteg felhordása
Ez előtt a közbenső réteget csiszolóvászonnal (közepes finomságúval) enyhén, körkörösen össze kell karcolni, a tapadás növelése céljából. Vastagbevonatoknál közbenső réteg képzésére nincs szükség, mivel ezeknél a felületkezelt alapra az átvonó (alapozó és közbenső réteg szerepét is betöltő) réteg egy műveletben felhordható.
Tixotrópia a festékszuszpenziók ama tulajdonsága, hogy különböző adalékanyagok (tixotropizálószerek, pl. a bentonit, kolloid kovasav stb.) hatására folyékonysági állapotukat (viszkozitásukat) megváltoztatják, mintegy kocsonyaszerűen megdermednek, de külső, mechanikai hatásra (pl. keverés, ecsetelés stb.) eredeti folyékonyságukat visszanyerik. A tixotrop festékek használata azzal az előnnyel jár, hogy egyszerű fejhordással vastagabb réteg képezhető, és a felhordási anyagveszteség a minimálisra csökkenthető. Ez utóbbi szempont különösen erősen tagolt felületek ecsetelésekor jelentős. A tixotrop festékek megjelenését, valamint ecsettel való felhordását az alábbi ábrák szemléltetik.

Tixotrop és nem tixotrop zománcfesték viselkedése az ecset bemerítésénél.
a) nem tixotrop;
b) tixotrop
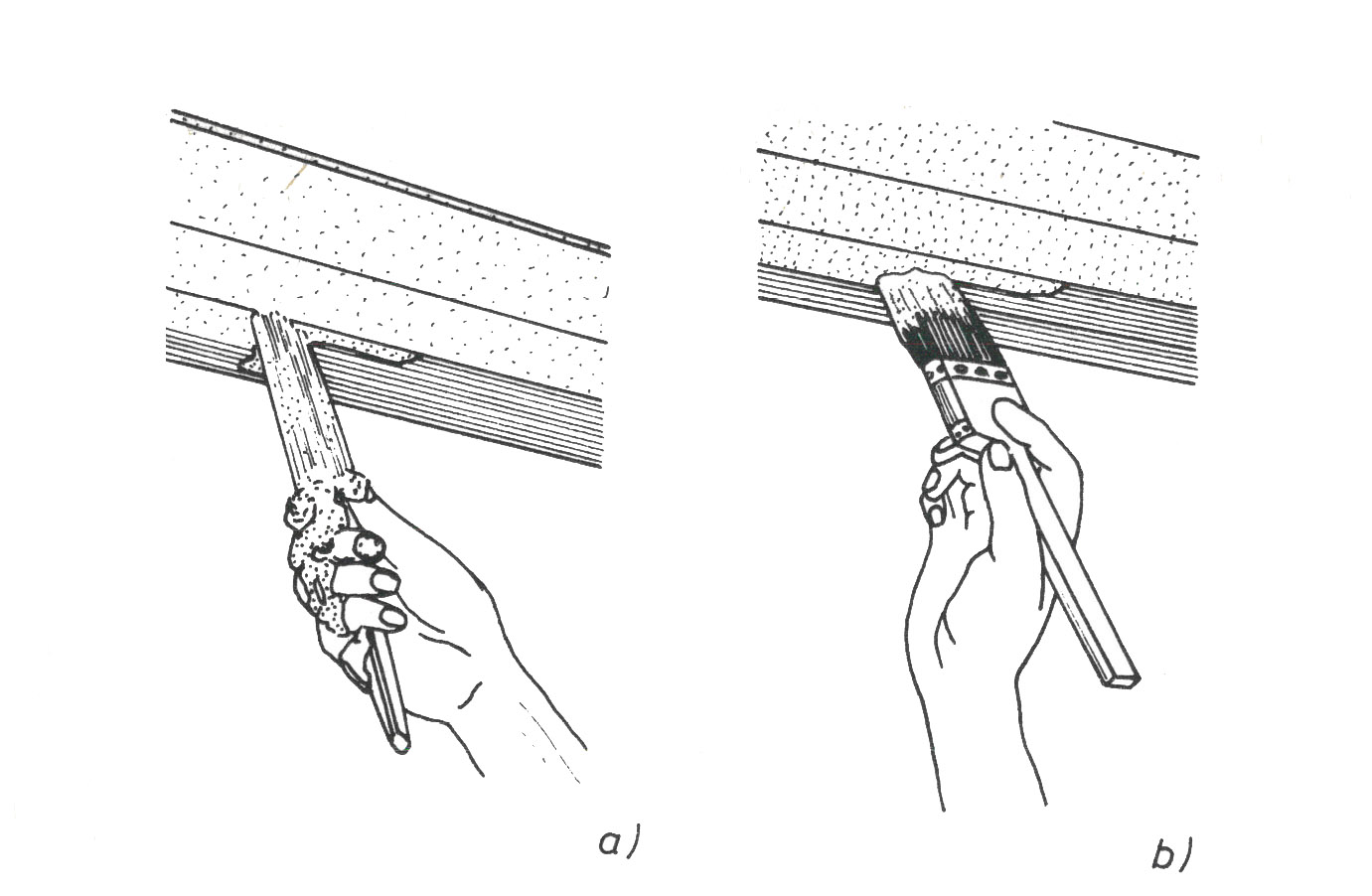
Tixotrop és nem tixotrop zománcfesték viselkedése ecseteléskor.
a) a nem tixotrop festék a függőleges helyzetű ecsetről visszafolyik;
b) a tixotrop festék a függőleges helyzetű ecsetről sem folyik vissza
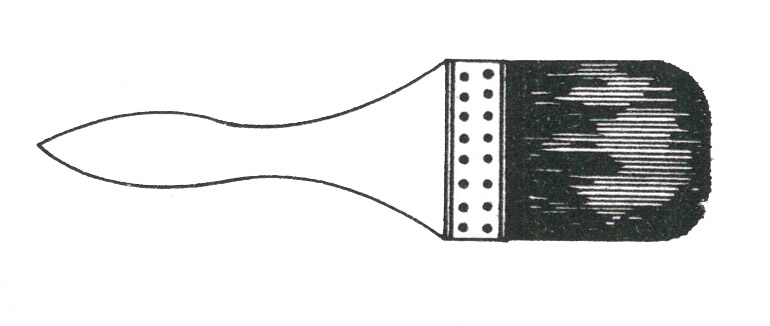
A tixotop festékek felhordására kiválóan alkalmas sörteecset
A bevonatok szárítása
Végezhető egyszerű fizikai úton (ahol kizárólag az oldószer elpárologtatása képezi a szárítási folyamatot) vagy oxigénfelvétellel (oxidatív úton), mint pl. lenolajkencés olajfestékek esetében, ahol a tiszta levegő, oxigéndús levegő (megfelelő hőmérséklet mellett) jelenléte fontos követelmény. Az előbbi természetes szárítási folyamat mellett mesterséges úton, hőkezeléssel gyorsítják a száradást. Ennek fontosabb változatai a következők.
A film vagy bevonat képzése beégetéssel
Erre alkalmas, rendszerint villamos fűtésű, beégető kályhákban. Ennek egyik hátránya, hogy a sugárzó hő egyenes vonalban terjed, így tagolt felületen nagymértékű lehet a leárnyékolás, amely jelentős hőmérséklet-különbséghez vezet.
- Hőkezelés külön e célra készült, infrasugárzó lámpákkal, amelyek a gyakorlatban (az előbbi okok miatt sem) nem váltották be azt a kedvező értékelést, amelyet a szakirodalom általában közölt.
- Hőkezelés áramló hőenergiával (pl. áramoltatott hevített levegővel), amely kedvező esetben, jól tervezett és kifogástalanul működő berendezés esetén a legegyenletesebb (leárnyékolásmentes) hőkezelési megoldás.
Követelmények a festékbevonatok hőkezelésekor
A festékbevonatok hőkezelésekor lényeges követelmény az előírt hőmérséklethatár és a beégetési idő betartása, valamint a bevonat előzetes szárítása, szikkasztása. A szárítás elhagyása esetén a festékbevonatokban maradt oldószergőzök a hőkezelés során felhólyagzást és egyéb meghibásodást okoznak.
Az oxigénfelvétellel filmet képző festékbevonatok (pl. olajfestékek, alkidgyan-tás lakkok és zománcok stb.) száradása szobahőmérsékleten, de főleg 40- 60 °C-os hőmérsékleten, ultraibolyasugarak hatására, technológiai szempontból előnyös gyorsasággal következik be. Pl. egy 40-50 p rétegvastagságú, 20 °C-os szobahőmérsékleten általában 36 óra alatt keményedő olajfesték-bevonat, egy 375 W teljesítményű kvarclámpa 50-70 cm távolságról érő sugárzása hatására, 2 órán belül teljesen száraz lesz.
Fényező csiszolás (polírozás)
Az átvonóréteg lágy, igen finom szemcsézetű, lemezes szerkezetű anyagokat (pl. bentonit, vasoxidvörös, csapatott kréta stb.) tartalmazó készítményekkel (polírviasz, polírozópaszta vagy víz) végzett olyan felületi koptatása, amely következtében a bevonat kellemes zsír- vagy magasfényű lesz. E művelet során a felületet lényegében igen vékony viaszszerű réteggel vonják be (polietilénviasz, szilikonolaj adalékok a polírozószerekben!), amely a festékbevonatot víztaszítóvá (hidrofóbbá) is teszi, és ezáltal annak ellenálló-képességét, tartósságát növeli. Bár elvileg mindegyik festékbevonat polírozható, a gyakorlatban csak az ilyen szempontból előnyös tulajdonságú festékbevonatokat (pl. nitro- és nitrokombinációs zománcok) szokták utólagos fényező csiszolással kezelni.
Minőségi ellenőrzés
A mázolómunkák fontos befejező művelete. Először a műveleteket végző dolgozóknak, majd csak ez után az ellenőrzéssel megbízott személynek (MEO) kell elvégeznie. A minőségi ellenőrzés elsősorban a festékbevonat-rendszer előírt műszaki jellemzőit (pl. rétegvastagság, színárnyalat, filmkeménység, egyenletesség stb.) hivatott megállapítani.
Ápolás, karbantartás
A festékbevonat-rendszerek igénybevétel alatti ellenőrzése, tisztítása és ápolása igen fontos művelet, mert ezáltal a bevonatok élettartama, tartóssága mintegy 25-35°/0-kal növelhető. Sajnos hazánkban ezt az igen fontos műveletet csak igen szűk területen vagy egyáltalán nem végzik el, pedig országos szinten is komoly anyagi megtakarítást jelentene. Az egyes festékbevonat-rendszerek karbantartásának menetét egyrészt a bevonat anyagi tulajdonságai, felépítése és a környezeti tényezők (elsősorban a szennyeződés és egyéb igénybevétel stb.) határozza meg.
A karbantartás a gyakorlatban a következő általános műveletekre terjedjen ki:
- A bevonatot mechanikai vagy egyéb úton (pl. durvaszőrű ecsettel, porszívóval, sűrített levegővel való fúvással stb.) meg kell tisztítani a por alakú, a környezetből lerakódott szennyeződésektől, amelyek gyakran komoly mértékben tartalmaznak a bevonatot erősen támadó anyagokat (pl. vegyi üzemek közelében).
- Ez után a bevonatot le kell mosni az előbbi eljárásokkal el nem távolítható szennyeződésektől.
- A felület letisztítása után alaposan át kell a bevonatot vizsgálni. A sérülések helyét és az egyéb folytonossági hiányokat előzetes (drótkefével vagy csiszolópapírral) felérdesítés után, lehetőleg saját (vagy azzal összeférő tulajdonságú) festékanyaggal – célszerűen ecseteléssel – ki kell javítani.
- Befejező műveletként az egyes festékbevonatokat, felépítésüknek megfelelően, felületi utókezeléssel kell ellátni.
Festékbevonatok ápolása, karbantartása
A festékbevonatok előbbiekben leírt ápolása és karbantartása szinte elhanyagolhatóan csekély összegbe kerül, nem munkaerő-igényes, mert 1-2 betanított dolgozó még jelentős létesítmények festékbevonat-rendszerének folyamatos karbantartási munkáit is el tudja látni.
A karbantartás, ápolás költségei sokszorosan megtérülnek, hiszen a bevonat élettartamának ily módon való mintegy 30%-os növelése azt jelenti, hogy pl. a 8 éven belül felújítandó festékbevonat-rendszert csak 8 + 2,5 = 11 év múlva kell felújítani. A kültéri festékbevonatok ápolási és karbantartási munkáit legalább évenként egyszer – kora tavasszal vagy késő ősszel – kell elvégezni, a belső, esetleg vegyi igénybevételnek kitett bevonatrendszer felújítására viszont az év bármely szakában sor kerülhet. Favédelem Protektor hőszigetelő festékkel, UV-védelemmel.
A mázolási műveletek elvégzéséhez a következő kéziszerszámokat, gépeket és segédeszközöket használják.
Kéziszerszámok
A fontosabb kéziszerszámokat az alábbi ábrák szemléltetik.
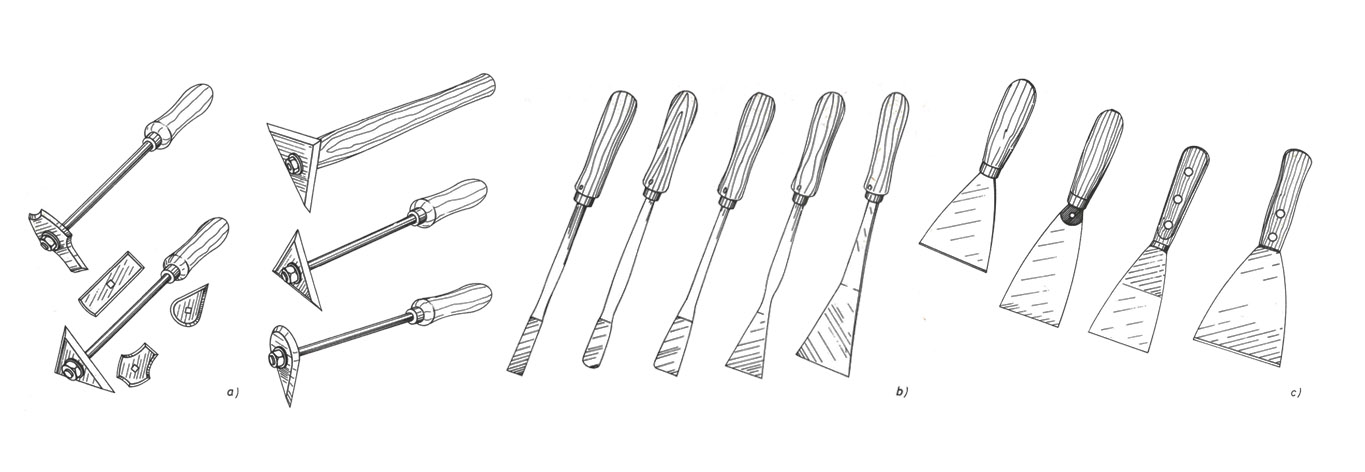
A felülettisztítás kéziszerszámai.
a) különféle kialakítású, cserélhető acéllemez kaparóéllel készült festékkaparók;
b) a festékréteg égetéssel való eltávolításához használatos, nyeles, acél kaparólemezek (spatulyák, shachtlik);
c) rozsdamentesítésre használt spatulyák.
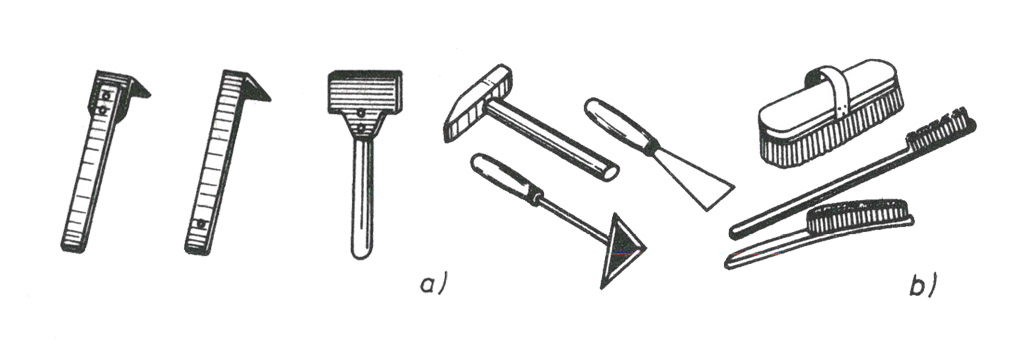
A felület-előkészítés fontosabb kéziszerszámai.
a) kaparóvasak (rasketták);
b) acélspatulyák, drótkefék
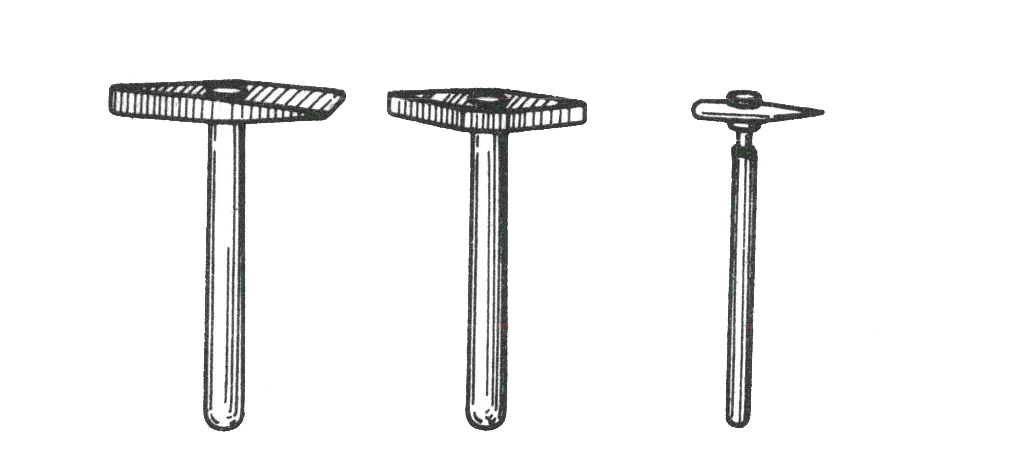
Rozsdaleverő kalapácsok
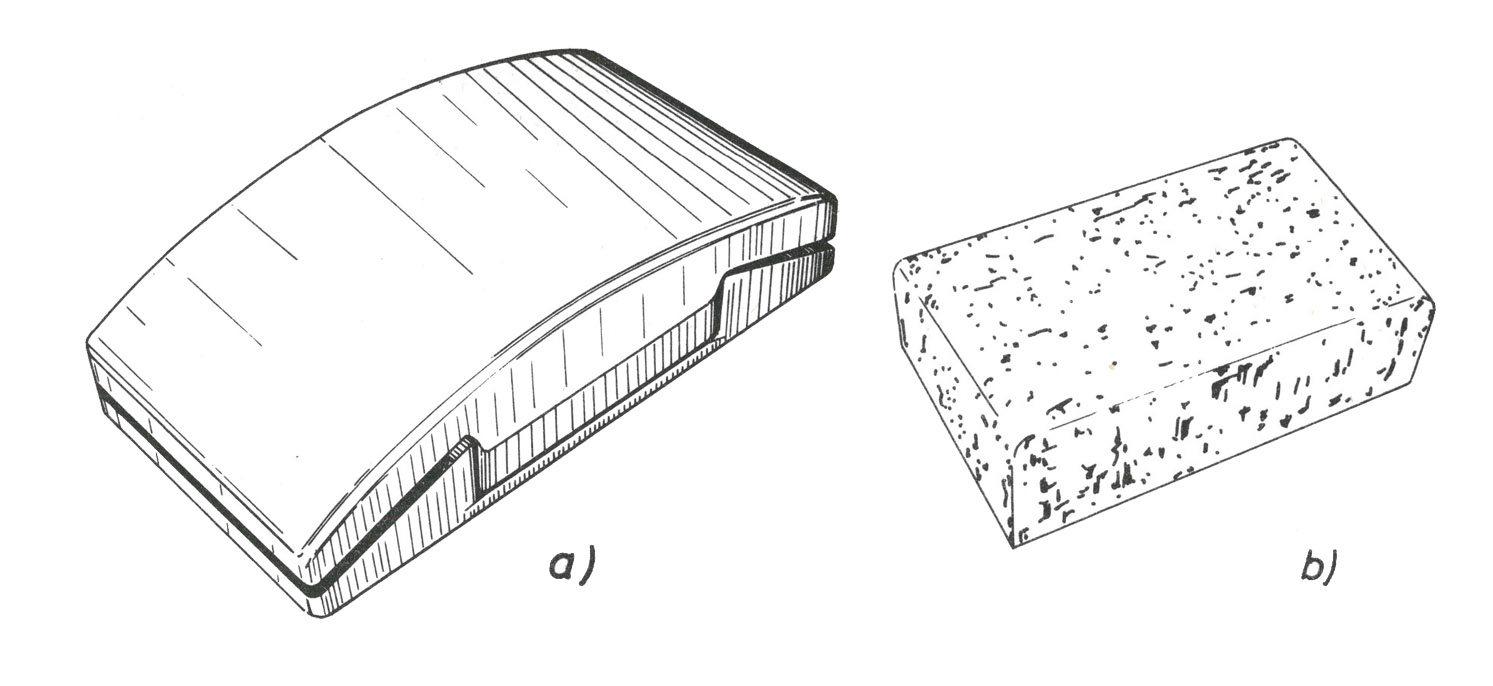
A kézi csiszolás segédeszközei.
a) gumiból készült bepattintós csiszolópapír-tartó idom (méretei: 120*70*35 mm, tömege: ~0,26 kg);
b) csiszolópapír-, ill. vászontartó parafatuskó (méretei: 100-120*60-70*35 mm, tömege: ~0,05-0,06 kg).
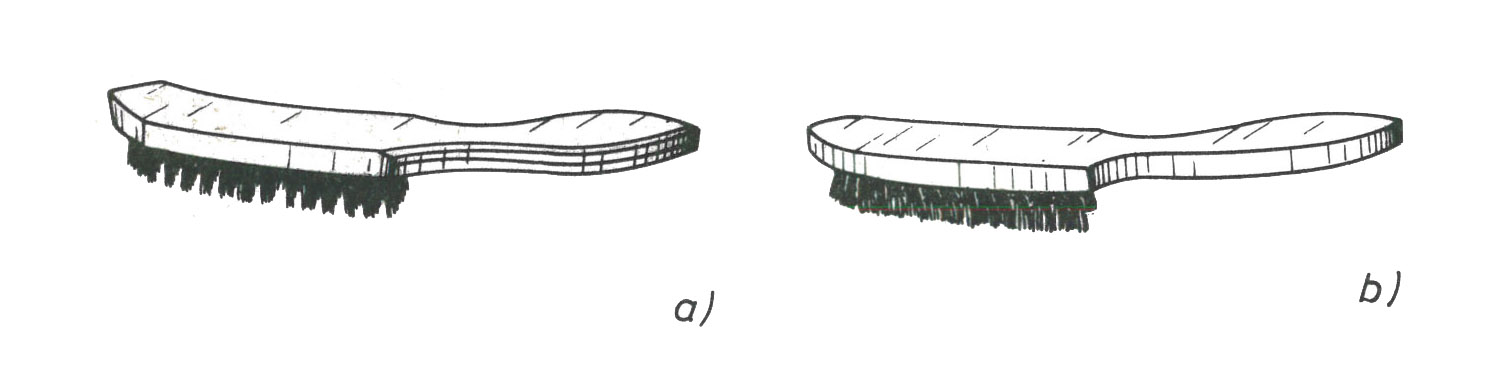
Felülettisztító fémhuzalkefék.
a) különlegesen kemény öntöttacél huzalkefe;
b) sárgaréz huzalkefe szikramentes rozsdaeltávolításhoz.
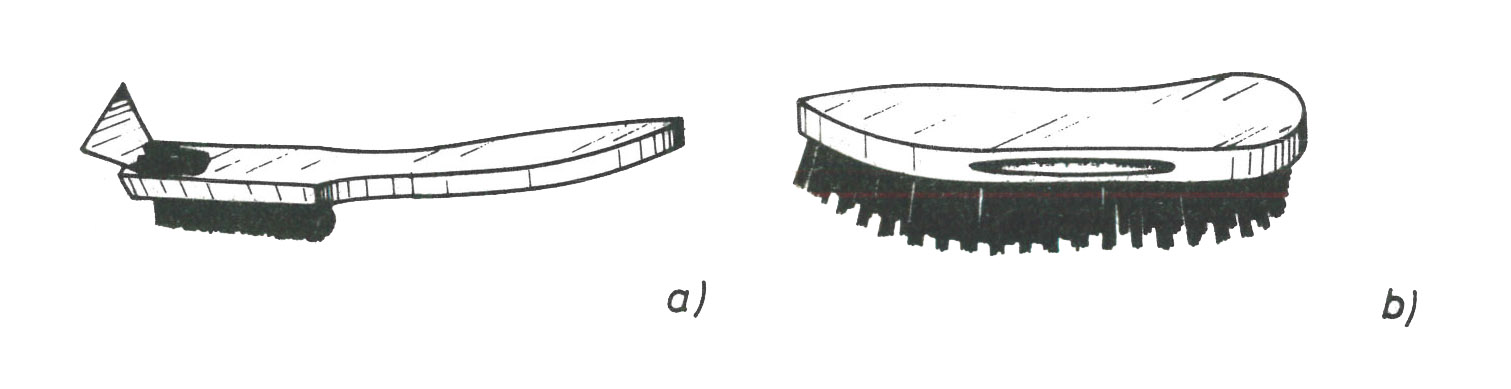
Acél huzalkefék.
a) kaparólemezzel egyesített;
b) régi lakkréteg, pl. parkettalakk felérdesítésére, átkarcolására.
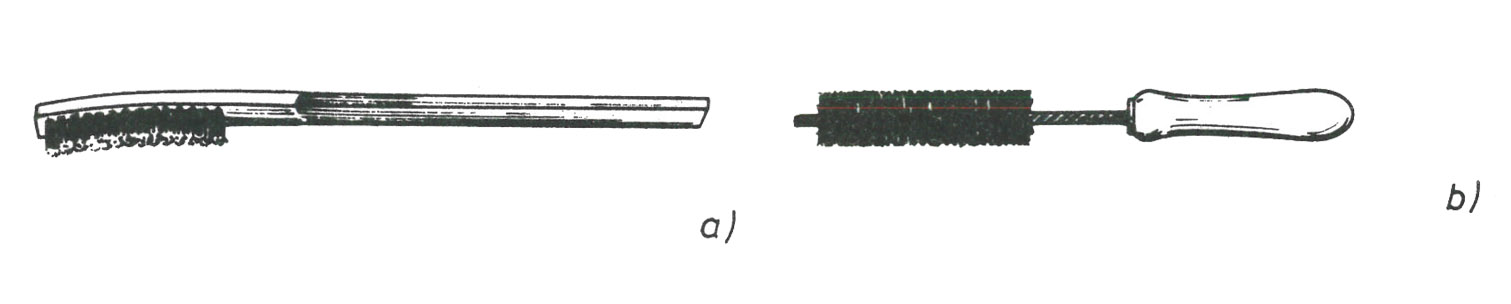
Különleges rendeltetésű acél huzalkefék.
a) fűtőtesttisztító;
b) csövek és üreges testek belső felületének rozsdátlanítására.
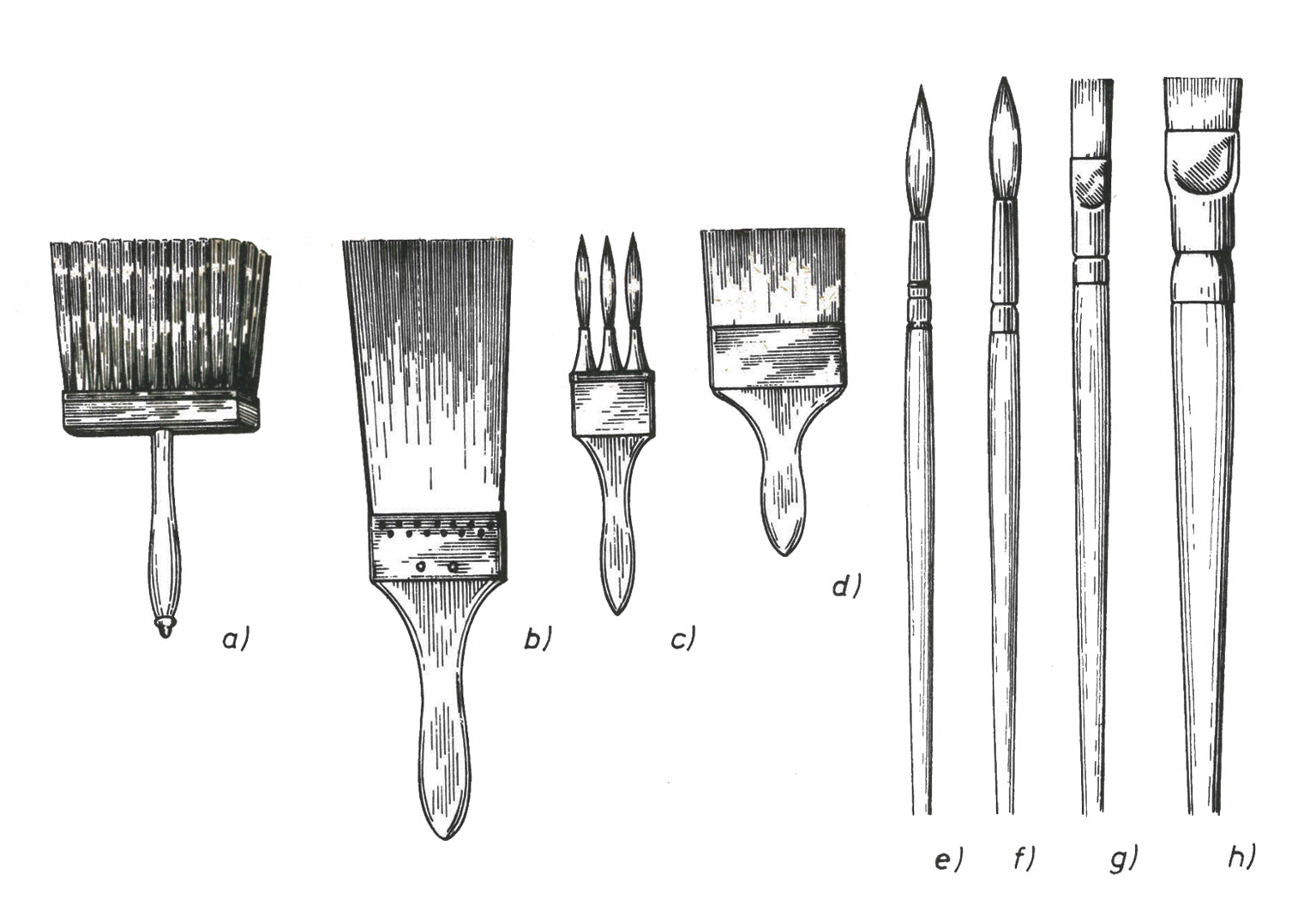
A díszítőfestés és erezés fontosabb ecsetfajtái.
a) mennyezetoszlató festőkefe;
b) ütögető (erező, finom rajzolatokat álcázó) ecset;
c) villás ecset;
d) mintázó ecset;
e) hegyes szőrecset;
f) sörte ecset;
g) hosszú sörtés lapos ecset;
h) rövid sörtés lapos ecset.
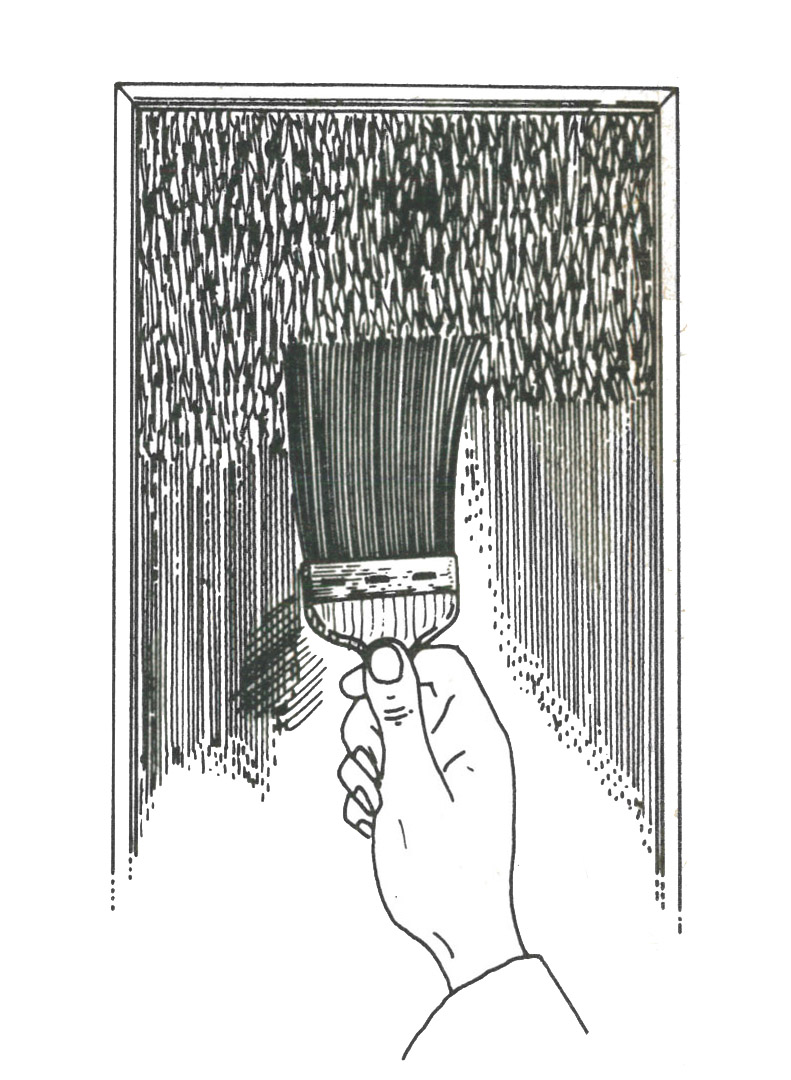
A finom pórusok hatását keltő festékréteg-szemcsézés művelete faerezésnél.
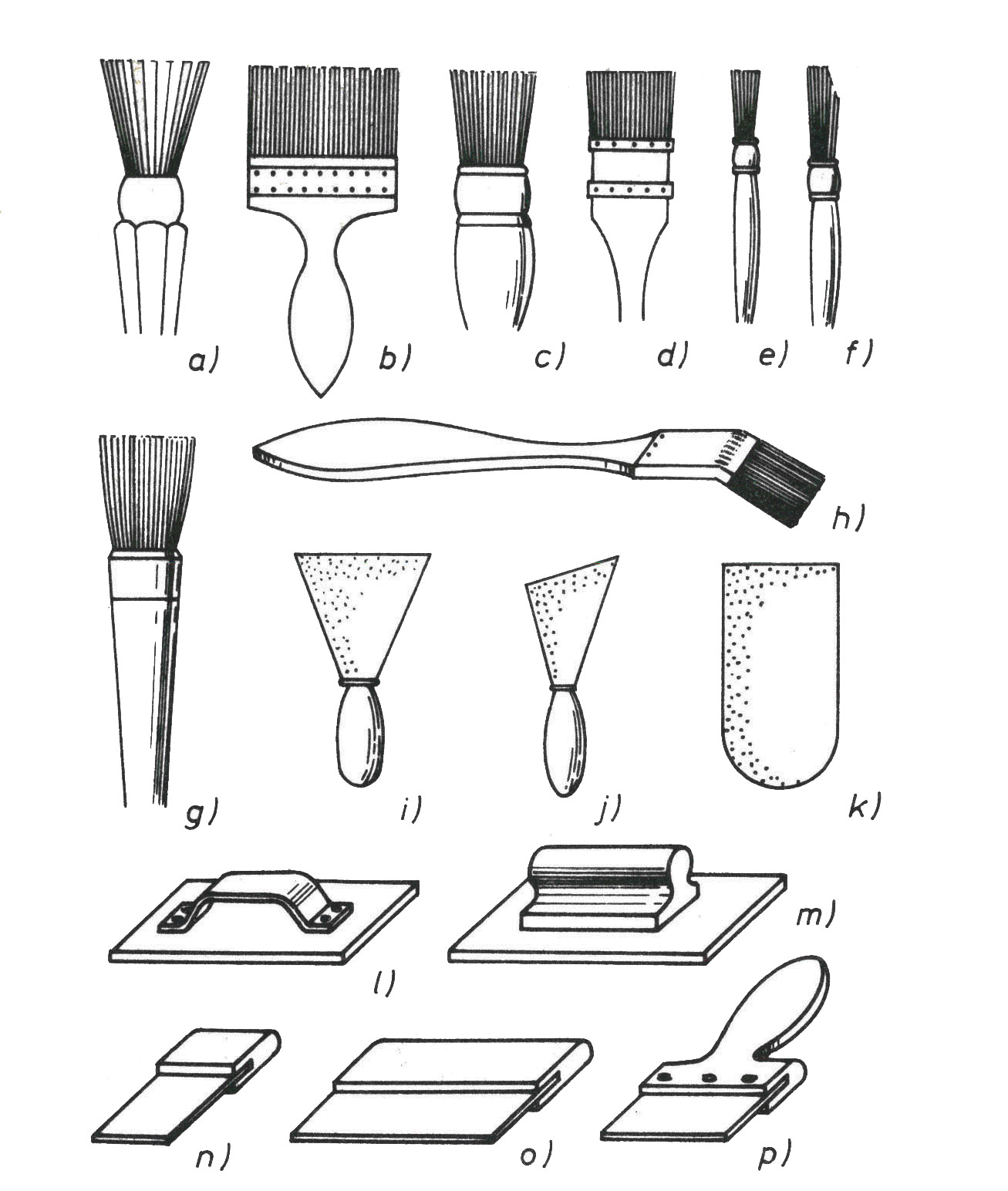
A mázolómunkák fontosabb kéziszerszámai.
a) marokecset;
b) oszlatóecset;
c) gömbölyű lakkozóecset;
d) lapos lakkozóecset;
e) f) vonalzóecsetek;
g) portalanító (felülettisztító) ecset;
h) radiátormázoló ecset;
i)-k) nyeles spatulyák;
l)-m) simítóacélok;
n)-p) japán és műanyaglemezes spatulyák.
Gépi-kéziszerszámok, gépi berendezések
A szakmai gyakorlatban használatos gépi, kéziszerszámokat az alábbi ábrák ismertetik.
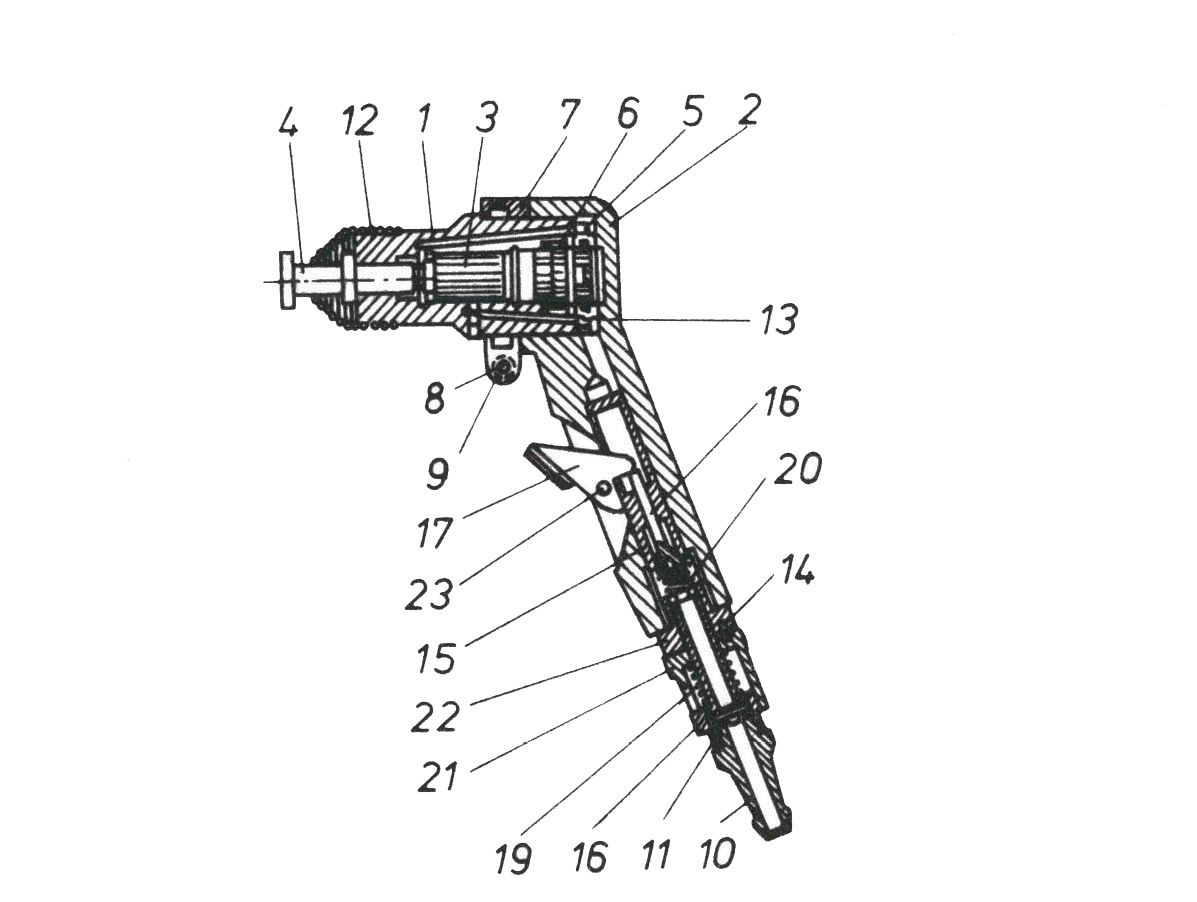
Légkalapács metszete.
1 – henger;
2 – markolat;
3 – dugattyú;
4 – tömörítő;
5 – tolattyúfedél;
6 – tolattyú;
7 – biztosító bilincs;
8 – hatlapfejű csavar;
9 – hatlapfejű anya;
10 – menetes tömlőcsatlakozó;
11 – szűrő;
12 – biztosítórugó;
13-14 – illesztőszeg;
15 – szelephüvely;
16 – szelepcsap;
17 – emeltyű;
18 – szabályozócsavar;
19 – rugó;
20 – kúposrugó;
21 – szabályozóhüvely;
22 – szabályozócsatlakozó;
23 – illeszthetőség.
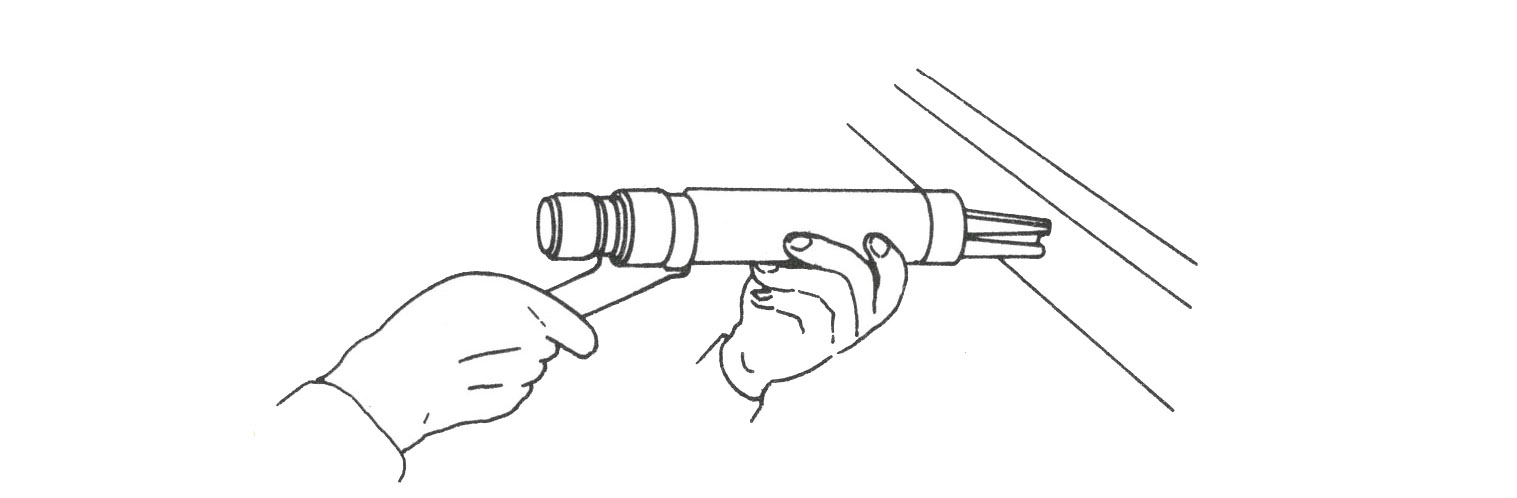
Acéltüskés verőpisztoly üzem közben
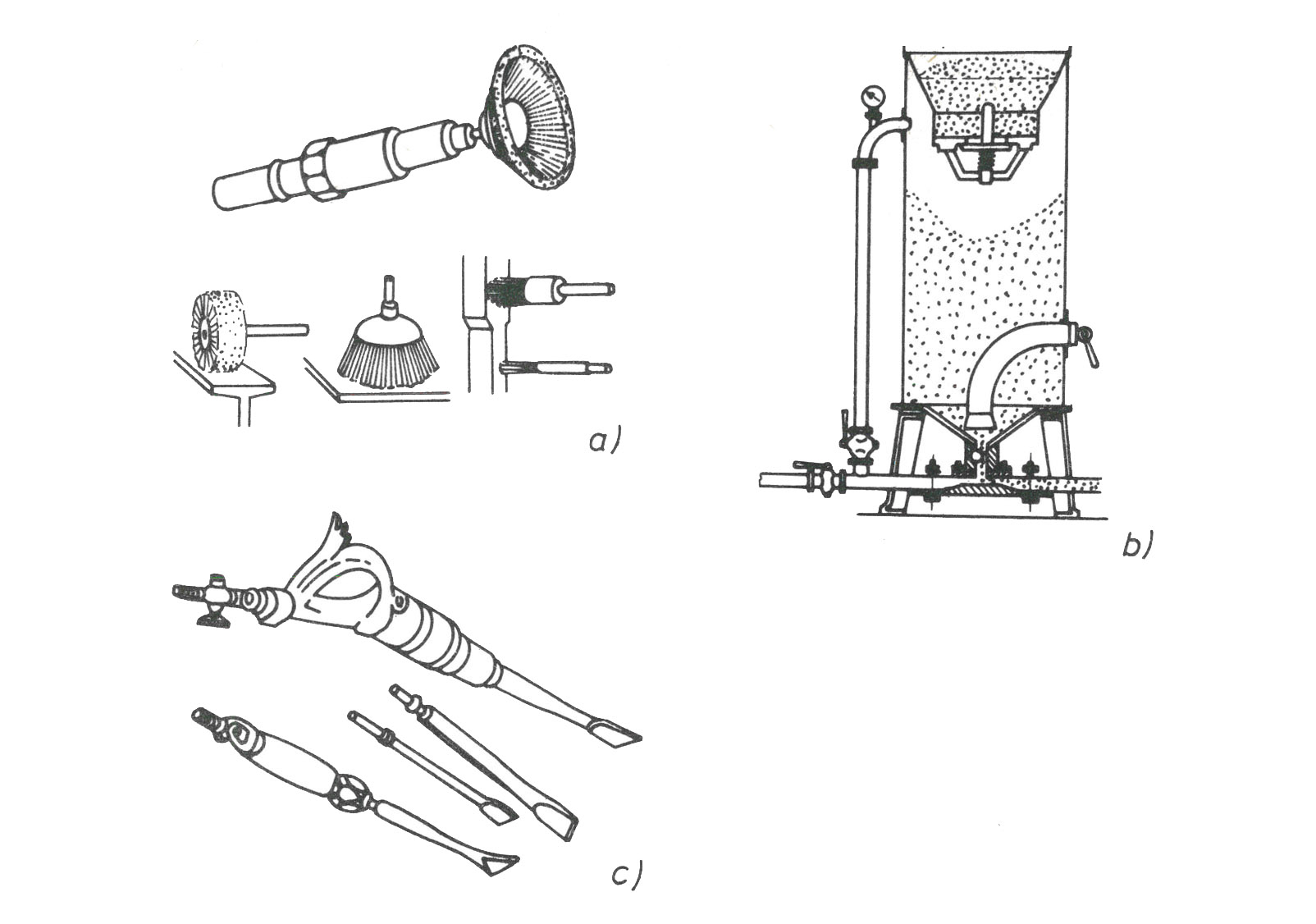
A rozsdátlanítás gépi eszközei.
a) rozsdaréteg eltávolító, gépi-kézi drótkefe (tömege kb. 2,6 kg, levegőszükséglete: 0,75 m3/min, fordulatszáma: 9500/min);
b) homokfúvó tartály szerkezete szemcsefúvó, rozsdátlanító berendezésekhez;
c) rozsdaeltávolító légkalapácsok, 2,5 kg-os, 2,15 kg-os, 1,0 kg-os légkalapácsok. Üzemi nyomás 5-7 bar, levegőszükségletük 0,25-0,30 m3/min, ütéseik száma 3500-3600/min, dugattyú-lökethossz 25 mm.
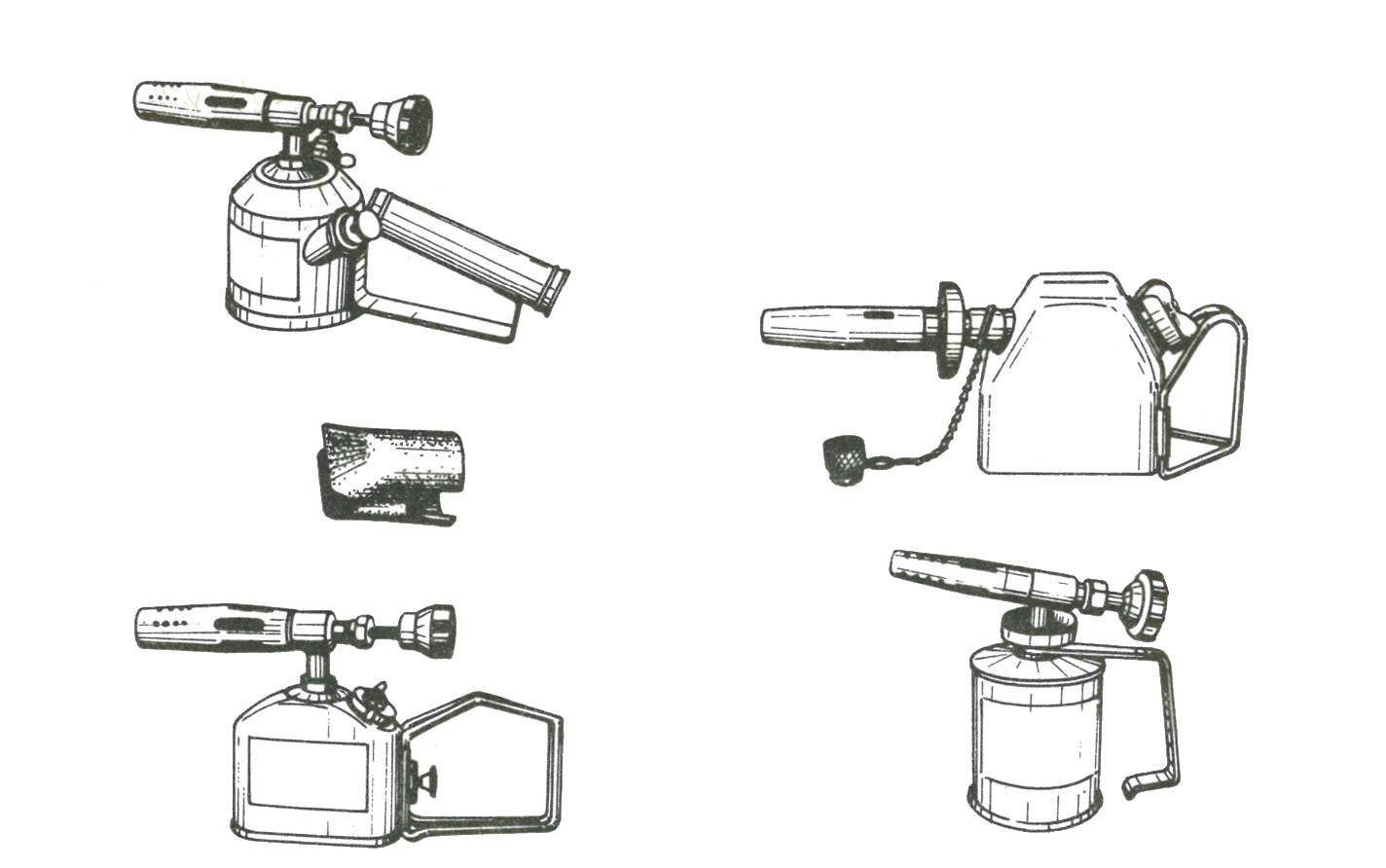
Különféle típusú benzinlámpák
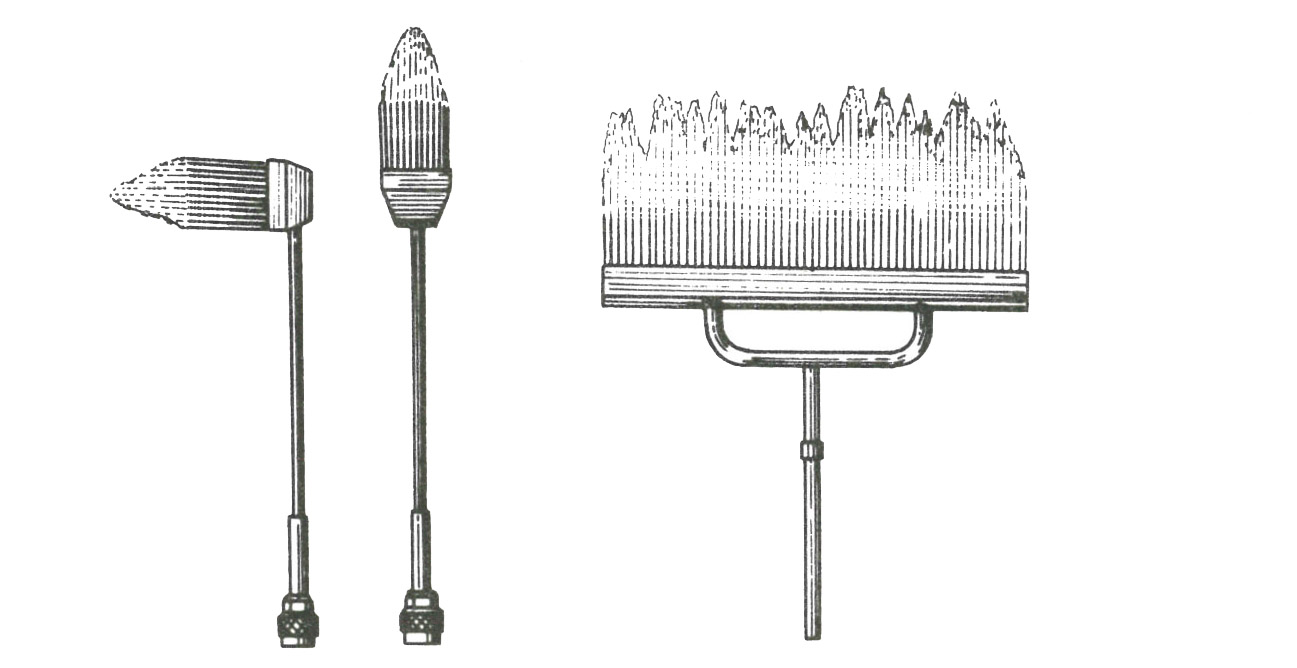
Különböző alakú égőfejek, lángsugaras oxidmentesítő berendezésekhez
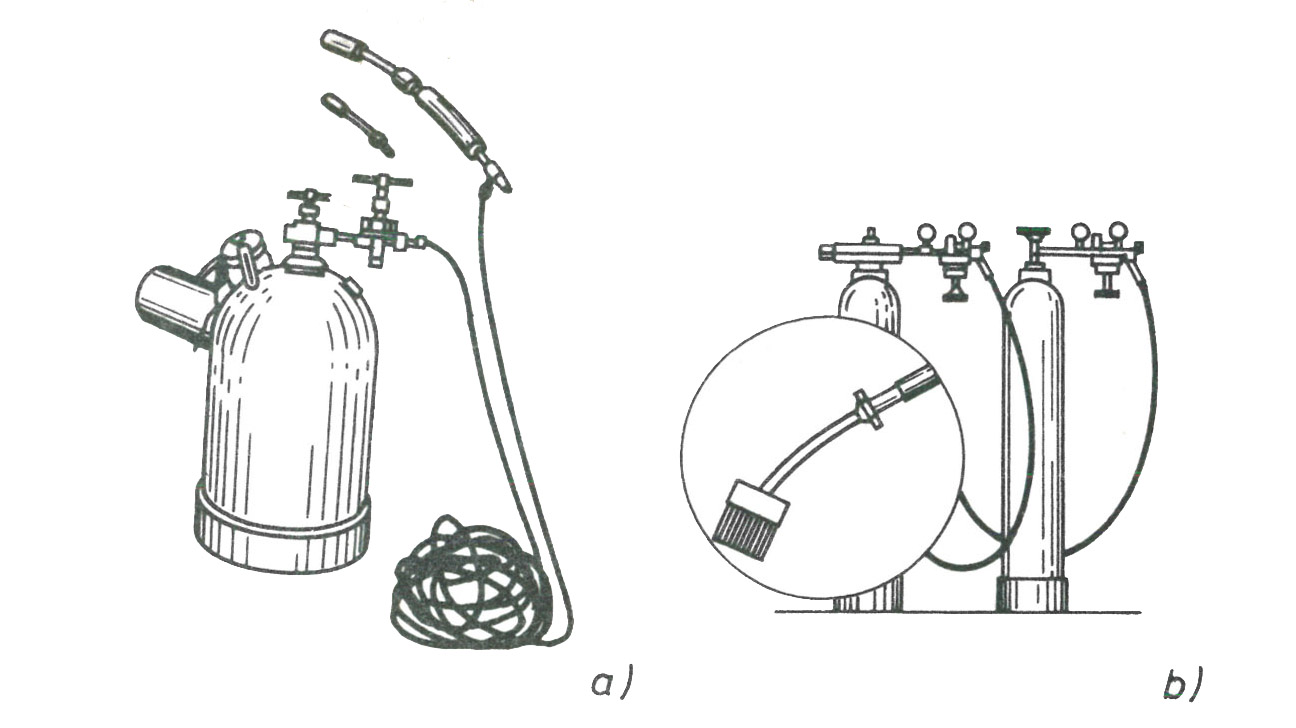
Lángsugaras oxidmentesítő berendezések.
a) propán-bután gázzal;
b) acetilén gázzal üzemeltethető.
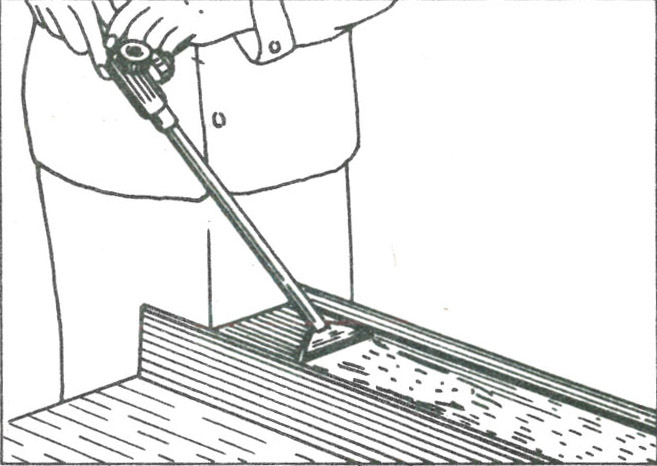
Lángsugaras oxidmentesítő berendezés üzem közben
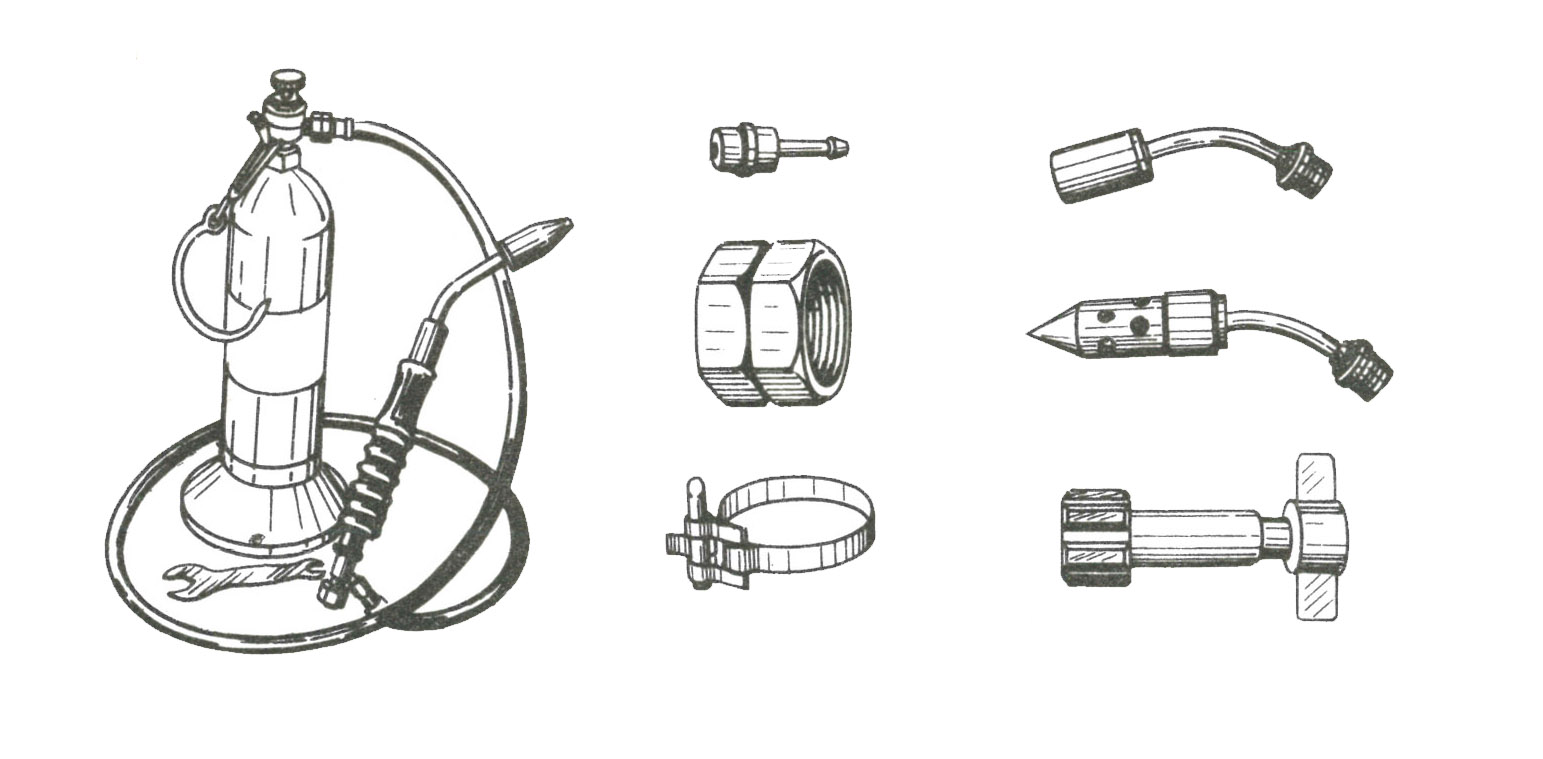
PB-gázos festékréteg-leégető berendezés és fontosabb tartozékai
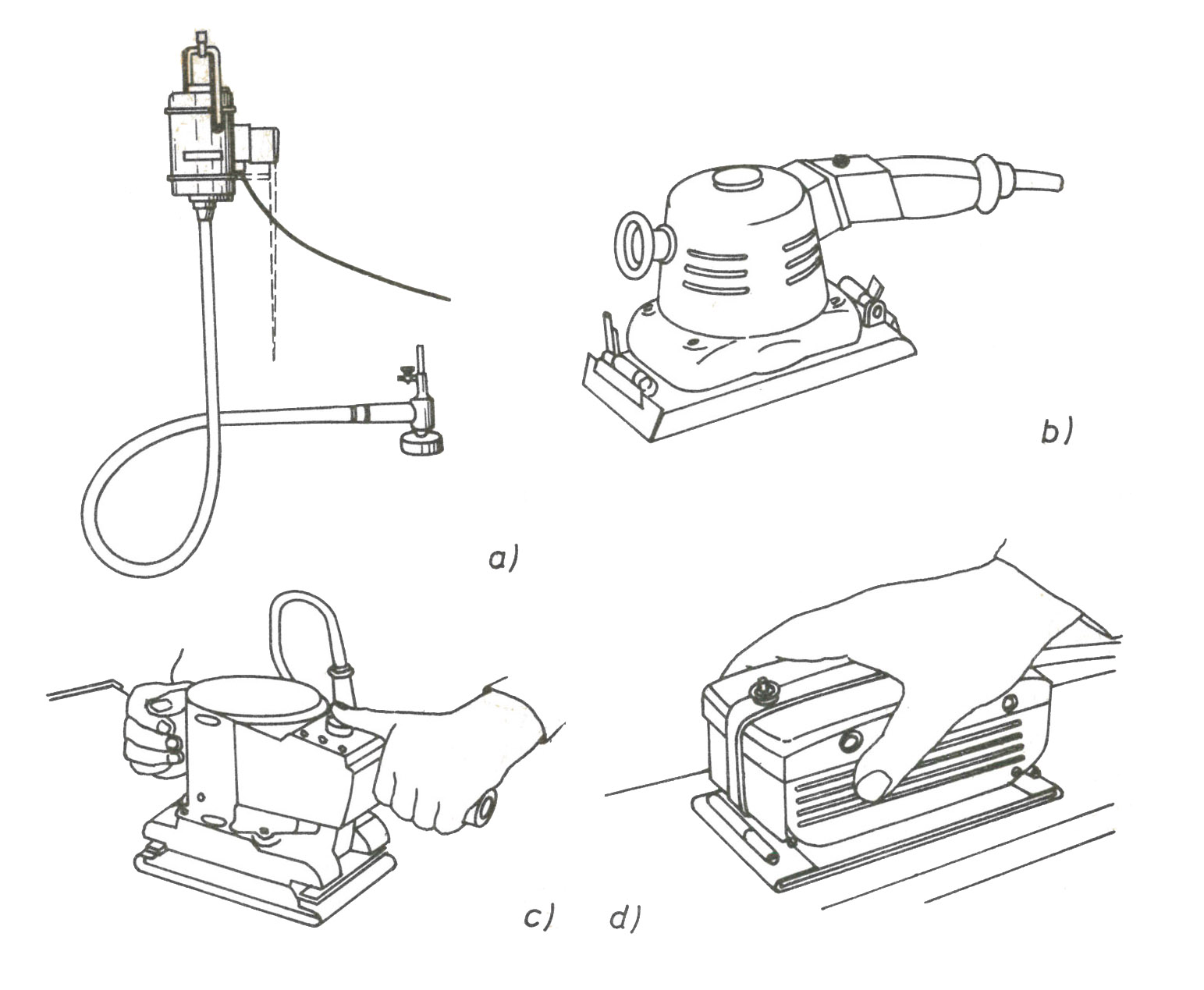
Csiszológépek.
a) felfüggeszthető motorházas, kisméretű, forgótárcsás csiszolóberendezés;
b) kisteljesítményű, vibrációs kézi csiszológép;
c) nagyteljesítményű, vibrációs kézi csiszológép üzem közben;
d) kisteljesítményű, vibrációs zsebcsiszológép üzem közben (fafelületek finomcsiszolására, polírozására használható, rezgésszáma 12000/min)
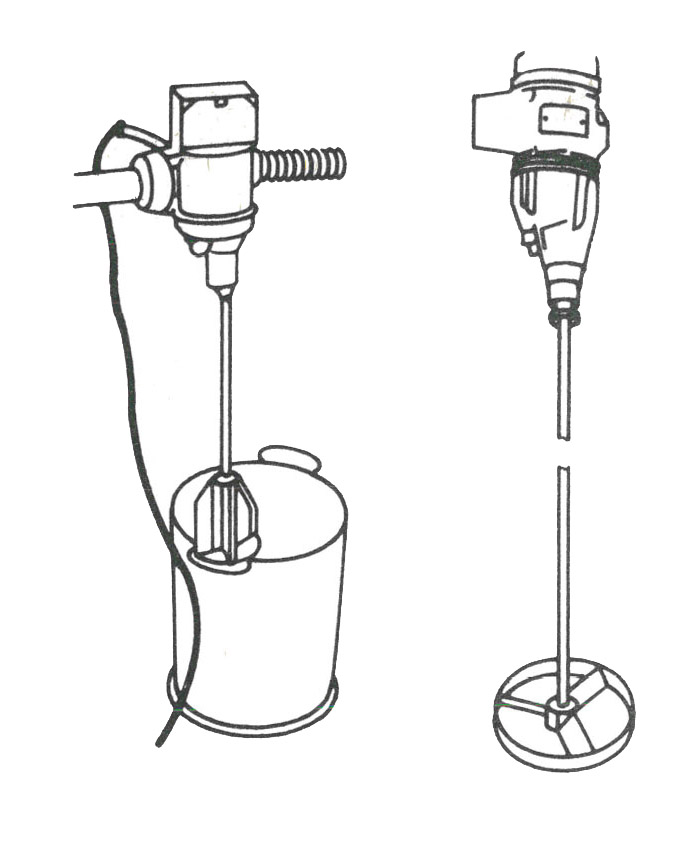
Különféle típusú, elektromos üzemeltetésű festékanyag keverők
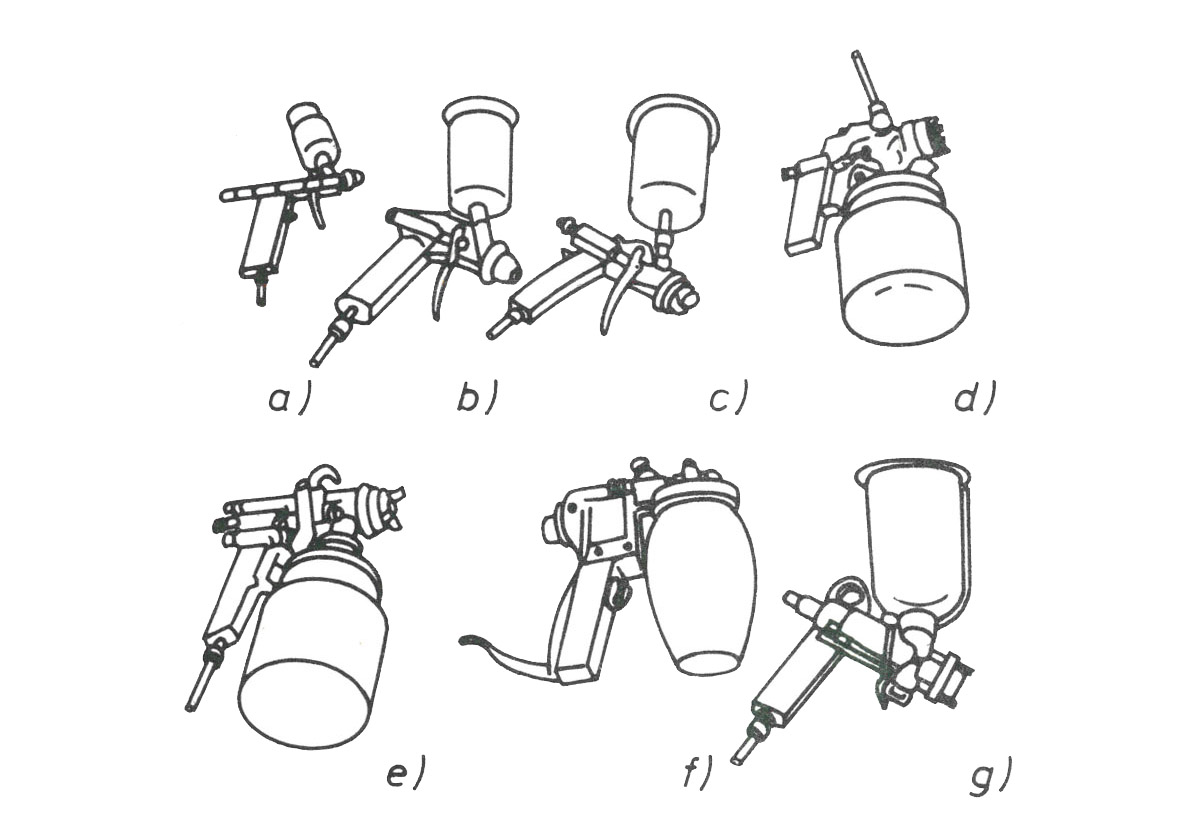
Különböző rendszerű festékszóró pisztolyok.
a) kisteljesítményű, felső tartályos, gravitációs adagolású, magasnyomású szórópisztoly;
b) c) ua., de nagyobb teljesítménnyel;
d) alsó tartályos, szívórendszerű, nagyteljesítményű szórópisztoly;
e) alsó tartályos, nyomás alatti porlasztású, nagyteljesítményű szórópisztoly;
f) rezgődugattyús, nyomás nélkül porlasztó, kisteljesítményű, főleg javításokra használható, elektromos üzemeltetésű szórópisztoly;
g) felső tartályos, nagyteljesítményű, magas nyomású szórópisztoly.
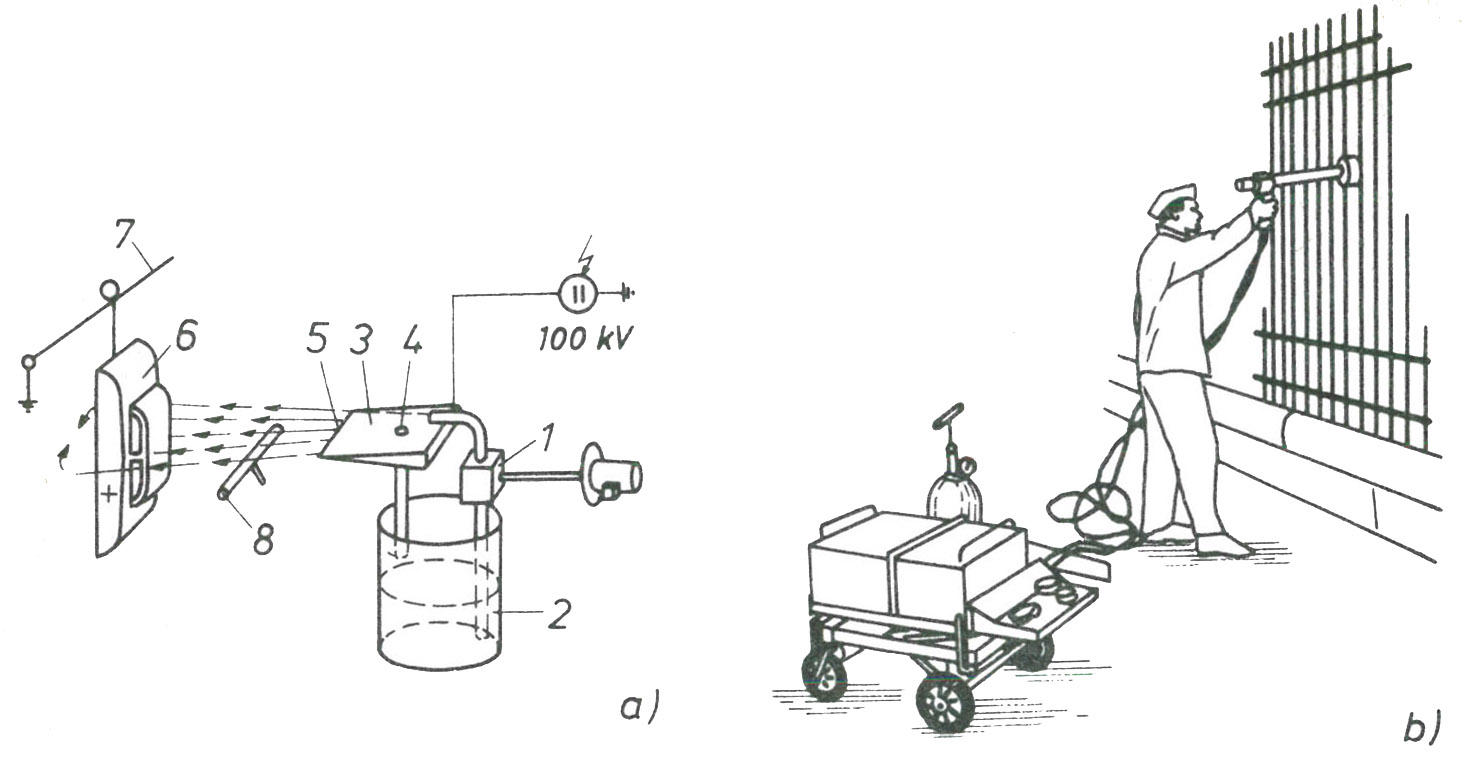
Elektrosztatikus festékszórás.
a) berendezés elvi sémája;
1 – nyomásszabályozó;
2 – festékanyag-tartály;
3 – porlasztást végző kúpos tárcsa;
4 – adagolónyílás, ill. vezeték;
5 – szórófej;
6 – festendő tárgy;
7-8 – földelés;
b) elektrosztatikus szórópisztoly üzem közben.
Mérőműszerek, segédeszközök
A mázolómunkákhoz a hazai gyakorlatban mérőműszereket és hasonló rendeltetésű segédeszközöket alig használnak, pedig ez minőségvédelmi szem-pontból különösen indokolt volna.
Példaképpen néhány ilyen rendeltetésű mérőműszer, ill. segédeszköz a következő:
- Mágneses festékréteg-vastagságmérők acélszerkezeteken képzett száraz festékréteg vastagságának mérésére használhatók (általában 5- 15%-os pontossággal).
- Nedves (tárcsás) rétegvastagságmérő: a nyers, még nem száraz festékréteg vastagságának mérésére alkalmas, sima felületű szerkezeti anyagok esetén (pl. acél, alumínium, fa, faforgács, farost stb.).
- Mérőpohár stopperórával: (FORD vagy DIN-mérőpohár) egy meghatározott hőmérsékletű lakk, vagy festékanyag állagának (folyékonysági állapotának, viszkozitásának) mérésére alkalmas. Meghatározott térfogatú (100 ml) lakk vagy festékanyag adott átmérőjű nyíláson (0=4, 6, 10 mm stb.) való kifolyási ideje (sec, min) jellemző az anyag viszkozitására. Minél nagyobb a kifolyási idő, annál nagyobb a vizsgált lakk vagy festékanyag viszkozitása (belső súrlódása) (sűrűnfolyós, hígfolyós, konzisztencia).
- Hőmérő: legalább ±0,5 °C méréspontosságú legyen.
- Légnedvességmérő (higrométer): előnyös az óraszerkezettel kombinált mérőműszer, amely folyamatosan jegyzi a munkatér páratartalmának változását (esetleg hőmérsékletét).
- A fa- és falszerkezet nedvességtartalmának meghatározására alkalmas elektronikus mérőműszer.
- A tömeg mérésére alkalmas mérlegek – legalább 0,01 kg pontossággal -, esetleg térfogatmérő eszközök (pl. mérőhengerek stb., amelyek szükség esetén a pontos keverési arányok ellenőrzésére használhatók.
Egyéni munkavédelmi eszközök
A felület-előkészítési és festési műveletek elvégzéséhez használatos néhány fontosabb egyéni védőfelszerelés az alábbi ábrákon láthatók.
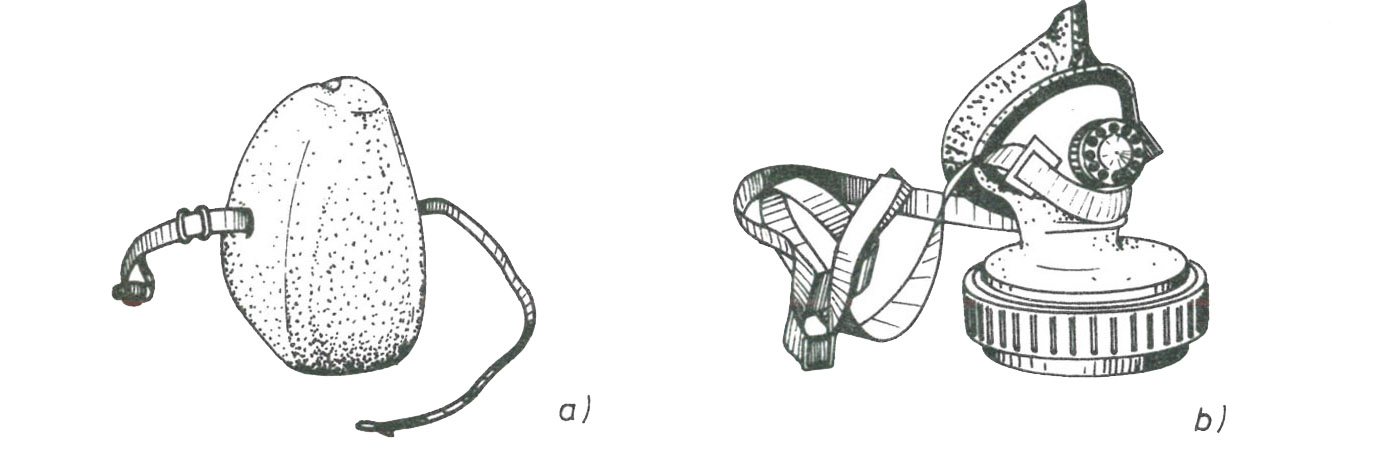
Légzésvédő segédeszközök.
a) por ellen védő szivacsálarc;
b) por és festékköd ellen védő, cserélhető szűrőbetétes álarc
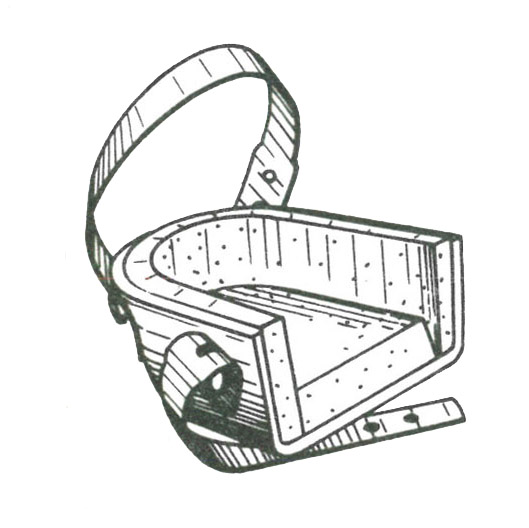
Habszivacs térdvédő
A festékanyagok kezelése és tárolás
A mázolási munkák festékanyagainak minőségét a tárolás és kezelés körülményei sokkal inkább befolyásolják, mint pl. a falfestőanyagokét. Éppen ezért a munkahelyi és az elosztó központi raktárakban a következő általános irányelveket kell betartani.
Általános irányelvek:
- A különféle anyagokat felhasználási területük szerint csoportosítva, egymástól jól elkülönítve úgy kell tárolni, ahogy azokat a gyártásidő sorrendjében felhasználják. A felhasználó vállalatnak az az érdeke, hogy a szavatossági időn túl az anyagokat lehetőleg ne tárolja, mert az ez utáni esetleges károsodásokért a gyártóműnél minőségi kifogás (reklamáció) nem érvényesíthető. Éppen ezért a raktáros minden beérkező szállítmánynál legalább szúrópróbaszerűen ellenőrizze, hogy a szavatossági (gyártási) idő fel van-e tüntetve az edények címkéin, ill. hogy az nem járt-e le. Ebben az esetben az anyagot rövid időn belül fel kell használni.
- Az egyes edényeket csak deszkaalátétek (lécek) közbeiktatásával szabad egymásra helyezni, úgy, hogy biztonságosan feküdjenek egymáson, és a terhelés az edények károsodását, alakváltozását ne idézze elő. így pl. 25 kg-os szögletkannákból legfeljebb 3 réteget szabad képezni. A sérült edényeket nem szabad a gúlába berakni.
- A raktár felépítés, elhelyezés szempontjából feleljen meg az általános tűzrendészeti irányelveknek és az illetékes tűzrendészeti hatóságok által kiadott utasításoknak.
- Festékraktárakban szigorúan tilos – még átmenetileg is – olyan anyagok tárolása, amelyek tévedés, csere folytán a festékanyagokban (esetleg felhordásuk után) károsodást okoznának. Jellegzetesen ilyen anyagok pl. a mészolaj, gázolaj, petróleum stb., amelyek – még ha kis mennyiségben is – az olaj- és zománcfestékekhez keveredve, meggátolják száradásukat.
- A méreggazdálkodás alá tartozó vagy különleges kezelést igénylő anyagok tárolására külön írásbeli utasítást kell a raktár részére kiadni. A mérgező anyagokat a raktárhelyiségen belül is lakattal elzárható térben (pl. ládában) kell tárolni. Ilyen anyagok pl. a lúgkő vagy marónátron, a fenol, az oxál-sav stb.
- Festékraktár kezelésével kizárólag olyan szakembert szabad megbízni – éppen az esetleges károk megelőzésére -, aki legalább olyan ismeretekkel rendelkezik, hogy az alábbiakban leírt, általános minőségi ellenőrző feladatokat is el tudja látni.
A festékanyagok minőségi ellenőrzése
A minőségellenőrzés a termék azonosításával kezdődik. Első feladatként az egyes edények tartalmát a címkén feltüntetett megjelöléssel egyeztetni kell. Az egyes anyagcsoportokon belül a következőket kell megvizsgálni.
Tapaszok (kittek)
Nincs-e beszáradva a tapasz? Gyakran előfordul ui., hogy a tapaszok az edény falától elválnak, zsugorodnak, esetleg felületük megrepedezik, s így a felületen száraz kéreg képződik, amely a felhasználás során minőségi hibákat okoz, ill. eltávolításuk jelentős anyagveszteséggel jár. Főleg fillingup és faátvonó tapaszoknál fordul elő.
További követelmények:
- A tapasz száradási ideje az előírt értéken belül legyen.
- A tapasz mechanikai eredetű szennyeződést nem tartalmazhat. (Ez legtöbbször nem gyártási, hanem szállítási, kezelési és raktározási hibából ered.)
- Nem lehet a tapasz szemcsés, felhordáskor karcolási nyomok a rétegen nem keletkezhetnek.
- A késtapasz spatulyával (kenőkéssel), egyenletes rétegvastagságban, gurulásmentesen felhordható legyen, tapadása a felülethez az előírtaknak megfeleljen (a gurulás oka rendszerint a magasabb víztartalom).
- Az előírt, legnagyobb rétegvastagságban felhordva sem lehet a tapasz repedezésre, zsugorodásra hajlamos (ez a hiba a megengedettnél nagyobb oldó-szertartalommal függ össze).
- Az előírt száradási idő után a tapasz csiszolása kellőképpen elvégezhető legyen.
- A tapasz halmazállapota (konzisztenciája) feleljen meg az előírtaknak, ill. az engedélyezett hígítószerek hozzáadagolásával felhordható legyen a felületre.
- Nem szabad olyan jelenséget észlelni (pl. vízcseppek, bőrképződmény, szételegyedés, kocsonyásodás, bűzösödés stb.), amely esetleg a tapasz káros átalakulásával függ össze.
- A szórótapaszok ellenőrzésére vonatkozóan az olaj- és a zománcfestékeknél leírt szempontok az irányadók.
Alapozó, közbenső és átvonó olaj- és zománcfestékek, lakkok.
A tapaszra vonatkozó követelményeket értelemszerűen ennél az anyagcsoportnál is meg kell vizsgálni, továbbá:
- Meg kell állapítani, hogy az oxidatív úton száradó festékek és lakkok (olajfestékek, szintetikus zománcok, csónaklakk, csiszolólakk stb.) nem tartalmaznak-e a megengedett 1-2%-nál több bőrképződményt. Ennél magasabb bőrképződmény ugyanis már jelentős kötőanyag-veszteséget okozhat, amely olaj- és zománcfestékek minőségi hibáinak forrása lehet (az anyagveszteség mellett). Ilyen festékanyagok – kötőanyag adagolása nélkül – felhasználásra alkalmatlanok.
- A pigmentált festékanyagok nem tartalmazhatnak olyan kemény, összeállt üledéket, amely a festék kötőanyagával, a szokásos időn belül (5- 10 perc), gondos keverés után sem azonos sűrűségű. Ebben az esetben már minőségi hibáról van szó, tehát kifogásolással kell élni. Egyes festékanyagok – felépítésükből kifolyólag – fokozottabban hajlamosak üledékképződésre, amelyek azonban nem minden esetben okoznak minőségi hibát. Ilyenek pl. az ólom-mínium tartalmú alapozó festékek, ólomfehér-tartalmú olajfestékek, stb.
- Színtelen lakkok: üledéket, mechanikai szennyeződést gyakorlatilag nem tartalmazhatnak. Gyakran előfordul, elsősorban hordókban tárolt lakkok esetében, hogy többszöri töltés után zavaró mennyiségű, apró bőrképződmények gyűlnek össze az edényben, amelyektől szűréssel sem minden esetben tisztítható meg a termék.
- Az előírt időn belül nem száradó, oxigénfelvétellel száradó lakkok, olaj- és zománcfestékek csak akkor tekinthetők minőséghibásnak, ha száradásuk az engedélyezett szikkatív adagolással nem állítható be.
- A pigmentált olaj- és zománcfestékek színárnyalatát ellenőriztetni kell, hogy – teljes száradás után – zavaró mértékben ne térjen el az előírt vagy ajánlati (etalon) mintáétól. Gyakran előfordul, hogy a színárnyalat csak néhány nap múlva állandósul (pl. gópszürke, krómzöld stb. zománcok). Ez a jelenség természetesen nem jelent hibát.
- Ellenőrizni kell, hogy a festékanyag folyékonysága, az engedélyezett legnagyobb hígítószer-adagolással, az előírt értéken belül biztosítható-e, ill. hígításnál káros átalakulás (kicsapódás, kocsonyásodás stb.) nem következhet-e be. Mindkét esetben minőségi hibáról van szó.
- Lakkoknál ellenőrizni kell, hogy színárnyalatuk (színszámuk) az előírt értéktől (vagy ajánlati mintáétól) zavaró mértékben ne térjen el.
- Fokozottan ellenőrizni kell, hogy a tárolásra, légköri nedvességre rendkívül érzékeny lakkok és zománcfestékek edénye légmentesen zárjon, illetőleg az anyagok esetleges károsodása (kicsapódása, gélesedése) ne következhessek be. A nedvesség, víz hatásától természetesen az e csoportba tartozó összes (kivéve a vizes diszperziós) festékeket óvni kell, s így vízzel való szennyeződésük (pl. beázásuk szállítás közben) minőségi hibát jelent.
- Két vagy több összetevős, katalizátorok hatására keményedő lakkokat és zománcfestékeket ellenőrizni kell, hogy a bevont száradás, az előírt keverési aránynál, a megadott időn belül következzék be.
- Ellenőrizni kell, hogy a felhordott festékanyagok vagy lakkok felületi megjelenése az előírt legyen. Pl. alapozó festékeknél vagy matt, ill. zsírfényű zománcoknál minőségi hibának számít, ha a bevonat túlzottan fényes. Természetesen a fényes bevonatoknál a mattulás és foltosodás stb. számít hibának.
- Két- vagy több-összetevős lakkok, zománcfestékek stb. egyértelmű hibája, ha a gyártómű az egyes összetevőket (komponenseket) nem az előírt arányban vagy olyan edényben szállítja, amely az anyagok károsodását idézheti elő.
Szikkatív oldatok
- Gyártásidejüket fokozottabb figyelemmel kell ellenőrizni, mert a szavatossági időn túl felhasználva rendszerint hatástalanok.
- A szikkatív oldatok üledéket gyakorlatilag nem tartalmazhatnak. Üledékes, zavaros szikkatívokat felhasználni nem szabad.
- A szikkatívok hatékonyságát ellenőrizni lehet, oly módon, hogy lakklenolajhoz (nem lenolajkencéhez) optimális arányban adagolják úgy, hogy annak teljes száradása (üveglapra vékony rétegben felhordva) 24-26 órán belül következzék be.
- A kicsapódott, kellemetlen, bomlásra emlékeztető szagú szikkatívoldatot átvenni, felhasználni nem szabad.
Oldószerek, hígítók
- Mechanikai szennyeződést, üledéket, víznyomokat, vízcseppeket nem tartalmazhatnak. A kötőanyagtartalmú hígítónak (zsíros hígító, félolaj, len-alkidhígító, lenolajkence stb.) legfeljebb 0,5- 1 térfogatszázalék üledéke lehet. Ezt az üvegből készült mérőhengerben egyszerűen meg lehet állapítani. (Vizsgálatkor az edényben tárolt hígítót természetesen fel kell kavarni mintavétel előtt.)
- A hígítók színárnyalata az engedélyezett vagy ajánlati mintáétól nem térhet el.
- Különösen fontos, hogy a hígítók – főleg a lakkbenzin, a szolventnafta (szintetikus hígító stb.) – ásványolaj-szennyeződést ne tartalmazzanak. Ilyen esetben az üveg- vagy porcelánedényekbe vett minta, természetes megvilágítás mellett is, különösen napfényben, liláskék színben, erősen fluoreszkál. (A fluoreszcencia az a jelenség, amikor egy anyag színe áteső és ráeső fényben egymástól eltér. Pl. egy ásványolajtartalmú lakkbenzin, üvegedényben, áteső fényben víztiszta, legfeljebb enyhén sárgás árnyalatú, ráeső fényben, felülről nézve, ibolyáskék színű.) Ásványolaj tartalmú hígítókat nem szabad átvenni és felhasználni.
- Ellenőrizni kell, hogy az egyes hígítók az előírt festékek, lakkokhoz alkalmasak-e s anyagukban káros átalakulás (pl. észtereknél vagy klórozott szénhidrogéneknél savképződés) nem ment-e végbe?
Kencék és kötőanyagtartalmú hígítók
A mázolómunkák egyes festékanyagait kencékkel vagy kötőanyagtartalmú hígítókkal kell elegyíteni. A kencéket, ill. a kötőanyagtartalmú hígítókat azonban nemcsak az előbbi célra, a festékek konzisztenciájának beállítására, hanem az alap előkészítésére, a hajszálcsöves szerkezeti anyagok (pl. fa, farost, faforgácslemez, beton, azbesztcement stb.) pórusainak telítésére, beeresztésére is használják.
Ez a művelet fokozott jelentőségű (pl. a kültéri és a beltéri igénybevételnek kitett faszerkezetek mázolási munkái során). Erre a célra mindmáig a lenolajkence az egyik legelőnyösebb anyag (ill. 10-15%-ban lakkbenzinnel hígítva). Újabban azonban az egyes műgyanta-alapú lakkokkal és festékanyagokkal végzett mázoláshoz különleges műgyantaoldatokat használnak.
Mit nevezünk kencéknek?
A szakmai gyakorlatban kencéknek nevezik a száradó növényi olajokból mesterséges úton, vegyi adalékokkal (szárítókkal) előállított termékeket. Általában jellemző rájuk, hogy oxigénfelvétellel száradnak, bár vannak ettől eltérő viselkedésűek is. A kencésítéskor a lenolajat vagy más száradó és félig száradó növényi olajokat ólom-, mangán-, kobalt- stb. vegyületekkel keverik és hő-kezelik. így képződnek az oxigénfelvételt elősegítő vegyületek (szikkatívok), másrészt a növényi olajok is előnyös átalakuláson mennek keresztül.
Az egyes olcsóbb növényi olajokat kén-dikloriddal főzve kencésítik. így készül a gyorsan száradó, igen vízálló, de kellemetlen, átható szagú, stox-kence, amelyet kevésbé igényes mázolási munkákhoz, elsősorban olyan helyeken használnak fel, ahol átható szaguk nem zavaró. Az egyes kencékhez különféle javítóadalékokat (pl. tallolaj, uretán-olaj, alkidgyanta, standolaj stb.) is adagolnak.
Némely anyag, amelyet a kencékhez hasonlóan pórustelítésre használnak fel, a levegő nedvességtartalmának vagy éppen a szerkezeti anyag (alap) nedvességtartalmának hatására köt, ill. képez filmet. A kencék és kötőanyag-tartalmú hígítók általános minőségi követelményeit a vonatkozó termékszabványok írják elő; ezek általában megegyeznek a lakkokra és festékanyagokra vonatkozó követelményekkel.
Oldószerek, hígítók
Az oldószerek olyan illékony folyadékok, amelyek a filmképzők oldására alkalmasak. Ezek felhordás után a festékbevonatból maradék nélkül eltávoznak. Az oldószereket nemcsak a filmképző műgyanták oldására, hanem a késztermék felhordásához szükséges folyékonysági állapot (viszkozitás) beállítására is használják.
Miben különböznek az oldószerek a hígítóktól?
A hígítók csupán annyiban különböznek az oldószerektől, hogy azokkal ellentétben nem minden esetben oldják a filmképzőt, de a festékanyaggal bizonyos arányban elegyítve, a festék folyékonyságát szabályozzák. A hígítók gyakran filmképző anyagot is tartalmaznak (pl. zsíros hígító, lenalkidhígító stb.). Az oldószer tehát minden esetben hígító is, de a hígító nem mindig oldószer! Az oldószerek és hígítók a festékbevonat kialakításában igen fontosak, s egy-egy helytelenül megválasztott vagy nagyobb mennyiségben adagolt hígító súlyos hibák forrása lehet.
Az oldószerekre, hígítókra vonatkozó általános követelmények:
- Oldják a filmképzőt, és elegyedjenek a többi illó alkotórésszel, maradók nélkül párologjanak el a bevonatból; káros alkotórészt ne hagyjanak vissza.
- A filmképzőre, pigmentekre káros vegyi hatást ne fejtsenek ki, szagtalanok legyenek, ill. szaguk ne maradjon vissza az elpárolgás után.
- Ne szenvedjenek tárolás közben káros vegyi átalakulást, hígító (azaz viszkozitáscsökkentő) hatásuk minél nagyobb legyen.
- Tűzrendészéti szempontból lehetőleg kis veszélyességi fokozatúak legyenek, ne legyenek gyúlékonyak.
A hígítók, oldószerek felhasználásához és minőségi értékeléséhez következő tulajdonságok ismerete szükséges:
A forráspont
Az a hőmérséklet (°C), amikor külső légköri nyomásnál a folyadék belső gőznyomása eléri a külső nyomást, és a folyadék forrni kezd. A forrpont alapján megkülönböztetnek alacsony (fp=3-10 °C között), közepes C/p=70-110 °C) és magas forrpontú (/p=110-170 °C) oldószereket.
A párolgási szám
Azt fejezi ki, hogy a vizsgált oldószer időben hányszor lassabban (vagy gyorsabban) párolog el, mint az egységül vett (etalon) oldószer.
Lobbanáspont
Az a °C-ban kifejezett hőmérséklet, amelynél az oldószer már olyan erőteljesen párolog, hogy a folyadékfelszín feletti légteret gőzeivel az alsó robbanási határig olyan mértékben telíti, hogy szikra vagy nyílt láng hatására az oldószergőzök robbanásszerű hevességgel égnek el. Minél alacsonyabb ez a hőmérséklet, az oldószer annál tűzveszélyesebb. A magyar szabvány V. veszélyességi fokozatba sorolja az anyagokat.
Alsó robbanási határ
Az a lobbanáspont hőmérsékletén kialakuló, térfogatszázalékban kifejezett oldószergőz-koncentráció, amelynél az oldószergőzök nyílt láng hatására lobbanásszerű hevességgel égnek el. Ha egy oldószer alsó robbanási határa pl. 0,5%, az azt jelenti, hogy a környező levegő 0,5 térfogatszázalék oldószergőzt tartalmaz, és szikra hatására robbanás következik be.
Felső robbanási határ
Az a határkoncentráció, amelynél a légtérben már nincs elegendő levegő (ill. oxigén) a robbanáshoz, ill. az elégéshez. Minél távolabb van egymáshoz ez a két határérték, annál robbanásveszélyesebb az illető folyadék (vagy gáz).
Gyulladási hőmérséklet
Az a °C-ban megadott hőmérséklet, amelyre hevítve az anyag már nyílt láng nélkül is meggyullad.
A mérgező hatás (toxicitás)
Ismerete egészségvédelmi szempontból rendkívül fontos. Még az egyébként legveszélytelenebb oldószerek is ártalmasak az egészségre, mert gőzeik a levegő oxigéntartalmát csökkentik, ezáltal a szervezet életműködéséhez szükséges oxigénfelvételt megnehezítik. Ez fokozott fáradtságérzettel, levertséggel, a munkavégző képesség csökkenésével jár. Az oldószergőzök eltávolíthatók természetes szellőztetéssel, légcserével.
Alapozó festékek
Az alapozó festékanyagokkal az alappal közvetlen érintkező, azzal tartós kapcsolatot létesítő rétegeket alakítják ki. Fa-, beton-, vakolat és azbesztcement-felületek vagy hasonló tulajdonságú hajszálcsöves szerkezeti anyagok mázolásakor az alapozóknak csak a pórusok telítése és légzárása, esetleg a felületi réteg szilárdítása a feladata.
Fém-, acélszerkezetek mázolása
Ilyen esetben az alapozókkal szemben korróziógátló, passziváló, inhibitor (késleltető) hatás követelménye is felmerül. A szakmai gyakorlatban sokféle ilyen vegyi hatást kifejtő pigmentekkel (pl. ólommínium, ólom-ciánamid, horganyfehér, cink- és tetroxikromát, bauxitvörös stb.) készült alapozófestéket használnak. Az egyes korróziógátló anyagok hatásmechanizmusát nem minden esetben tisztázták.
Az alapozó festékeknek az alábbi általános feltételeket kell kielégíteniük:
- Az alapot passziválják, ill. az azon végbemenő korróziós folyamatot állítsák meg, vagy fékezzék. Ez elsősorban az acélszerkezetek esetében követelmény.
- Olyan védőréteget képezzenek, amely meghatározott ideig (8- 10 naptól 6-8 hónapig, sőt tovább) a korróziós folyamatot megállítja.
- A további (közbenső és átvonó) lakk- vagy festékrétegek tapadását, ill. kapcsolatát lehetővé tegyék.
- Lehetőleg minél kisebb rétegvastagságban fejtsék ki rendeltetés szerinti hatásukat.
- A bevezető részben leírt általános követelményeket elégítsék ki.
Közbenső és átvonó festékek, lakkok
Az e csoportba sorolható festékanyagok és lakkok közvetlenül nem érintkeznek az alappal (esetleg a lakkok), hanem vagy közvetítő, átmeneti réteg képzésére alkalmasak az alapozó és átvonóréteg között, vagy a festékbevonatrendszer legkülső, azaz a légtérrel vagy támadó közeggel közvetlen érintkező (átvonó) rétegének kialakítására valók. Ez utóbbiak rendeltetéséből adódik, hogy fokozottabb igénybevételnek vannak kitéve, mint a bevonatrendszer többi rétegei. Kültéri igénybevétel esetén pl. a csapadékvíz, napsugárzás, vegyi anyagok stb. elsősorban az átvonó-réteget károsítják, ill. támadják meg.
Közbenső és átvonó festékekkel szembeni követelmények
A közbenső rétegre vonatkozóan fontos követelmény, hogy mind az alapozó, mind az átvonó réteghez tapadjanak, azaz átmeneti, közvetítő kapcsolatot hozzanak létre, ne váljanak le. Az átvonó réteggel szemben viszont alapvető követelmény, hogy a bevezető részben felsorolt környezeti hatásoknak és mechanikai igénybevételnek tartósan, a tervezett időtartam teljes idején át, meghibásodás nélkül ellenálljanak. A közbenső és átvonó réteg képzésére sokféle vegyi felépítésű festékanyagot és lakkot használnak.
Lakkok és műgyantaoldatok
A felületvédelem műszaki gyakorlatában lakkoknak nevezik a színtelen vagy színes, de minden esetben átlátszó (legfeljebb áttetsző) fényes vagy matt (selyemfényű, zsírfényű, viaszfényű stb.) filmképző anyagokat. Igen lényeges, hogy a lakkréteg alatt az alapfelület eredeti megjelenése (pl. a faanyagok erezete, rajzolata) – ellentétben a zománcfestékekkel – megmarad, ill. felismerhető. A lakkréteg felhordási művelete a lakkozás.
Lakkok történelmi háttere
A lakkok már ősidők óta (2-3 ezer éve) fontosak voltak az emberiség kultúrtörténetében. Ezek közül sok lakk (pl. kopállakk, japán lakk, kínai fahéj stb.) használata napjainkig fennmaradt. Ugyanakkor a vegyipar, elsősorban a műanyagkémia gyors fejlődése következtében sokrétűen felhasználható, vegyileg igen ellenállóképes, nagy hőállóságú, kopásálló stb. lakkok is piacra kerültek. A jelenlegi legnagyobb tartósságú műgyanta alapú lakkok élettartama – kültéri igénybevétel esetén – 15-20 évre tehető, ami kielégítő.
A hazai gyakorlatban, a kültéri faburkolatokon, ill. faszerkezeteken készült lakkozás élettartama legfeljebb 2-3 év
Közismert, hogy egy lakk élettartama – azonos igénybevétel és felület esetében – mindig kisebb, mint a belőle készült zománcfestéké. Hazai vonatkozásban viszont hiányoznak az olyan (ventillációs hatású) lakkok, amelyek viszonylag nagy nedvességtartalmú faszerkezetekre felhordva nem pattognak le, mert nagy páraáteresztő képességük révén a faanyag késleltetett kiszáradását lehetővé teszik. A lakkokra vonatkozó általános minőségi követelmények lényegében megegyeznek a festékanyagoknál leírtakkal.
A vastagbevonatok anyagai
A műszaki felületvédelemben az utóbbi években egyre gyakrabban alkalmazzák a korszerű, nagy tartósságú „vastagbevonatot”. Ezek a hagyományos korrózió elleni lakk- és festékbevonat-rendszerektől elsősorban nem a rétegvastagság méreteiben, hanem a védőréteg anyagi (vegyi, molekuláris) felépítésében térnek el.
Minden lakk-, ill. festékbevonat-rendszerre egy optimális rétegvastagság jellemző
Bizonyos határérték felett ennél nagyobb rétegvastagság már műszakilag nem megfelelő, mert lepattogzásra, gyors tönkremenetelre hajlamos. A hagyományos festékbevonatok optimális rétegvastagsága – szinte függetlenül a felépítő festékanyagoktól – viszonylag szűk határértéken belüli, általában 120- 150, de legfeljebb 200 ^m.
A felújított festékbevonatok új festékrétege az alapon maradt régi réteggel együtt megnövekedik ugyan, de egy bizonyos határ felett a régi festékréteget már maradék nélkül el kell távolítani. Ellenkező esetben kellő védőértékű és tartósságú bevonatrendszer nem képezhető.
A vastagbevonatok az említett hagyományos festékbevonat-rendszerektől általában a következőkben térnek el:
- Legfeljebb alapozó festés vagy vegyi és egyéb felületkezelés után, egyetlen (legfeljebb kétszeri) művelettel alakítják ki a végleges vastagságú bevonatot.
- A vastagbevonatok rétegvastagsága szélesebb határértékek között választható meg, mint a hagyományosaké. Általában vastagbevonatoknak azok nevezhetők, amelyek teljes rétegvastagsága az előbbi pontban felsorolt jellemzőkkel rendelkezik, így elsősorban nagy mechanikai szilárdság (ütésállóság, kopásállóság), vegyi ellenálló-képesség, villamos átütési szilárdság, esetleg hőállóság stb. Ennek megfelelően szélsőségesebb környezeti igénybevételnek is kitehetők.
Különleges rendeltetésű festékanyagok
Iskolatábla-festékek (helytelenül lakkok vagy mázak)
Kevés kötőanyagot tartalmaznak. Hígfolyós állapotban olyan hígítóval kell felhordani őket, hogy a fal pórusaiba beszívódjanak, filmet ne képezzenek, intenzív, egyenletesen matt, foltosodásmentes feketére színezzék a felületet. Feltétel, hogy víz hatására (24 órai vízben áztatás) ne foltosodjanak, ne oldódjanak ki. Újabban nemcsak fekete, hanem kellemes pasztellzöld vagy más élénk színű iskolatábla-festékeket is használnak.
Hőálló ezüst festék (helytelenül zománc)
Lényegében néhány százalék kuma-rongyanta benzolhomológos oldatához adagolt, tükröző vagy felületre úszó alumíniumpigment-paszta. Kizárólag száraz, páralecsapódásnak nem, de 400 – 500 °C-os hőhatásnak is kitett, előzetesen rozsdátlanított acélszerkezetek mázolására használják. 200.. .250 °C köröli hőmérsékleten a kumarongyanta erős füstképződés mellett, hólyagzás nélkül kiég, ill. elpárolog, és így csupán a pigmentpaszta képezi a bevonatot.
Kalapácszománcok
Általában nitro-, és egyéb műgyantás kötőanyaggal készülnek; színjelző pasztákkal színezhetők. Tulajdonságaik felépítésük szerint változnak. A jellemző és tetszetős kalapácsütésszerű rajzolatokat az alumínium-pigmentpasztához vagy kötőanyaghoz kevert, felületi feszültséget előidéző szilikonolaj- vagy egyéb adalékok okozzák.
A hatáskeltő adalék nem elegyedik a kötőanyaggal, ill. oldószerrel, hanem kisebb-nagyobb cseppecskék alakjában kiválik, az alumíniumpigment paszta szemcséi pedig a cseppek széleire úszkálnak. Nagy mintázatú rajzolatot kevés, apró mintázatút több pigment adagolásával lehet elérni. A pigment mennyisége általában 5- 14%. Kizárólag szórással hordható fel.
Zsugorzománc
Sok színárnyalatban gyártott, alkidgyanta-alapú, jellegzetes ráncosodással száradó zománcfesték. Toluollal hígítható, 80-90 °C-on 1 órán belül ráncosodik és 120- 130 °C-on 2 óra alatt beégethető. Szórással kell felhordani, s felhasználás előtt 4% K 116 jelű kobaltszikkatívot kell hozzáadagolni. Kiadóssága 6-8 m2/kg.
Jégvirágzománcok
Elsősorban fekete, de más színárnyalatokban is előállítható, ricinénalkid-műgyanta kötőanyagú zománcfesték, amelyet az előbbihez hasonló területeken használnak fel. Meglehetősen rugalmas, de fémfelületeken nem eléggé tapadó, jellegzetes jégvirágrajzolatú bevonatot képez. A rajzolat 40-60 °C körüli hőmérsékleten szén-dioxidban gazdag légtérben alakul ki, majd ezután 150- 160 °C között 1 órán át kell hőkezelni. Jellemzői általában a zsugorzománccal egyezők.
Néhány fontosabb effekt- (rajzolatos!) lakk-, ill. zománcbevonat megjelenési formáját az alábbi ábra szemlélteti.
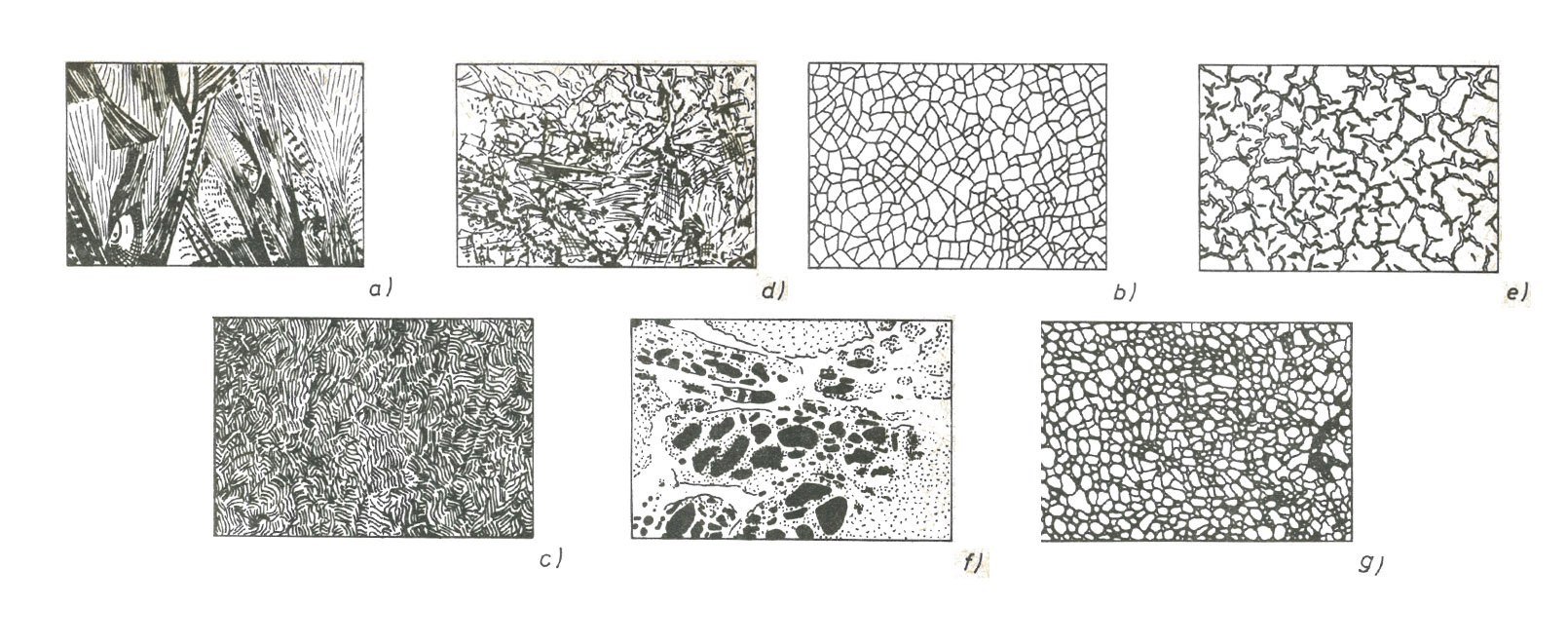
Különböző lakkmintázatok.
a) kristálylakk;
b) jégviráglakk;
c) ráncos lakk;
d) szövedékes lakk;
e) repedezett lakk;
f) márványlakk;
g) kalapácslakk
Zsírtalanító- és zsíroldó szerek – mázolási munkák
Ezeket a mázolási munkák területén elsősorban és csaknem kizárólag fémalapok tisztítására, a zsír, olaj, bitumen, kátrány stb. alapú szennyeződések eltávolítására használják. Ilyen célra a következő anyagcsoportok alkalmasak.
Oldószerek
Egyszerű fizikai úton oldják a zsiradékokat, s oldat alakjában távolítják el a felületről. Használatukkor – különösen erősen tagolt szerkezetek esetében – ügyelni kell arra, hogy az oldott zsiradékot ne továbbítsák egyik helyről a másikra. Fontosabb zsíroldószerek pl. a lakkbenzin, középbenzin, foltbenzin, petroléter, benzol, xilol, szolventnafta, triklór-etilén, szén-tetraklorid, aceton és a külön erre a célra készített oldószerkeverékek.
Lúgos kémhatású sók vagy lúgok
Ezek vizes oldatban a zsiradékok egy részét vegyileg vízoldható sóvá (szappanokká) alakítják (elszappanosítják), s így a felületről eltávolítják. Ilyen zsiradékeltávolítók pl. a marónátron, marókáli, trisó, szóda, hamuzsír stb.
- Marónátron: nátrium-hidroxid (NaOH), vizes oldata, a nátronlúg. Erősen nedvszívó (higroszkópos), fehér, sószerű tömeg. Rendkívül veszélyes, maróhatású, vízben erős hőfejlődéssel oldódik. Használatakor védőszemüveget, gumikesztyűt és védőruhát kell viselni. Zsírtalanításra 10-15%-os oldatát használják. Ügyelni kell arra, hogy a horganyt (cinket) és az alumíniumot heves hidrogénfejlődés közben oldja, amely adott esetben robbanási veszélyforrás lehet (ugyanez a többi lúgos anyagra is fennáll!).
- Marókáli: kálium-hidroxid (KOH). Tulajdonságai az előbbiével megegyeznek.
- Trisó: trinátrium-foszfát (Na3P04). Enyhén sárgásfehér, ipari vízben opálosan oldódó, kristályos anyag. Lúgos kémhatással oldódik, de kevésbé maró hatású, mint az előbbiek. 10-12%-os oldatát használják zsírtalanításra.
- Szóda (ammóniákszóda): nátrium-karbonát (Na2C03). Ipari célokra elsősorban a kristályvízmentes terméket használják, amely laza, fehér színű, vízben kiválóan oldódó por. 10-15%-os oldatban a trisóval közelítőleg azonos zsíroldó hatású.
- Hamuzsír: kálium-karbonát (K2C03). Bár a nátriumkarbonátnál valamivel erősebb maróhatású, használata mégsem terjedt el, mert erősen nedvszívó, összeálló, kristályos anyag, és így kezelése is nehézkesebb.
Emulziós zsírtalanítok
Egyrészt fizikai úton oldják a zsiradékszennyeződéseket (mint az oldószerek), majd emulgeáló hatásuk folytán habképződéssel eltávolítják azokat. Igen előnyös zsírtalanítok.
Szintetikus mosószer alapú zsírtalanítók
A szakmai gyakorlatban kiválóan beváltak.
Festéklemarató szerek
Régi vagy meghibásodott festékrétegek eltávolítására használják. Vegyi felépítésük szerint oldószerekként feloldják, meglazítják, maróanyagokként elroncsolják a régi festékbevonatokat. (Az elnevezés nem következetes, mert az oldószeres készítményeket is festéklemarónak nevezik.) A festékbevonat felépítése, ill. a fedőréteg anyaga szabja meg, hogy melyik csoportba tartozó festéklemaróval távolítható el legelőnyösebben. A festéklemaró anyagok felépítésük szerint a következő csoportokra oszthatók.
Oldószeres festéklemarók
Különféle oldószerkeverékekből állnak. Elsősorban acetont, benzol-szénhidrogéneket (pl. toluol, xilol), klórozott szénhidrogéneket (pl. triklór-etilén, szén-tetraklorid stb.), esetleg alkoholokat (metilalkohol, denaturált szesz stb.), ritkábban észtereket (pl. etil-butil-acetát) tartalmaznak.
Kevés olyan anyagot is tartalmaznak, amelyek az oldószer párolgását azáltal csökkentik, hogy felületén hártyát képeznek. így az oldószer hosszabb ideig hat a festékfilmre. Hátrányuk, hogy a felület zsírtalanítása körülményesebb. Az oldószeres festéklemarók gyúlékony, erősen tűzveszélyes, bódító és mérgező hatású anyagok. Főleg aceton, toluol és triklór-etilén, diklór-metén stb. elegyéből állnak, és paraffinadalékot tartalmaznak.
Az oldószeres festéklemarók hatását az alábbi ábrák szemléltetik.
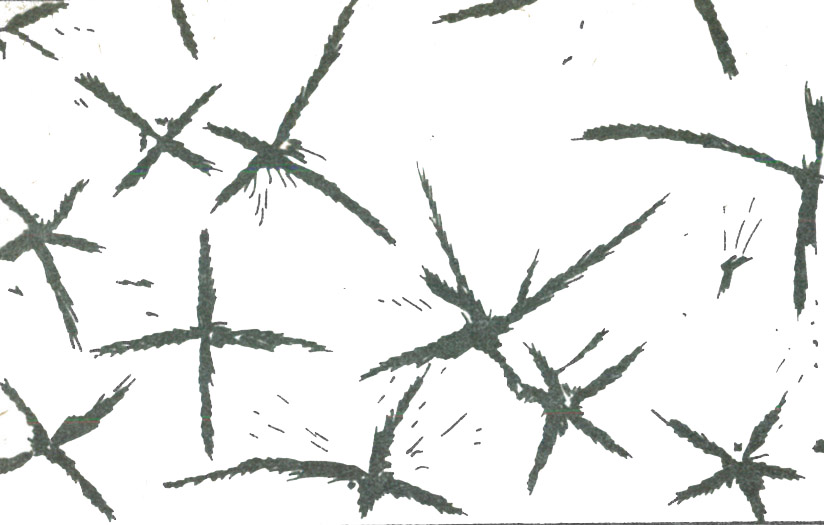
Az agresszív oldószer első fázisában sugár irányú, jellegzetes repedéseket hoz létre a bevonaton
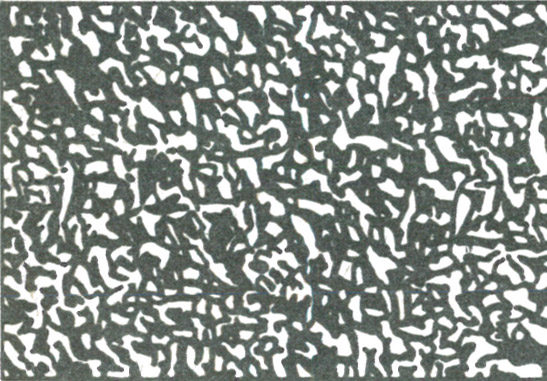
A megbontott régi festékbevonat további oldószer hatására erősen duzzad, ráncképződés közben összeugrik, fellazul és ilyen állapotban spatulyával egyszerűen eltávolítható
Lúgos festékmarók
Ilyen célra káli- és nátronlúgot, trisót, hamuzsírt, ammóniákszódát és vízüvegoldatot, vagy ezek keverékét szokták használni, 10- 15%-os vagy töményebb oldatban. Használatukkor ügyelni kell erős maróhatásukra, így kizárólag védőszemüvegben, gumikesztyűben és védőöltözetben szabad dolgozni velük. Alumínium, horgany és horganyzott acélfelületre felhordott festékréteg maratására nem használhatók! Szükség esetén a kezelt felületet ecetsav vagy ammónium-klorid (szalmiáksó) 4-5%-os vizes oldatával le kell mosni, és így semlegesíteni.
Kombinált festékmarók
Lúgos hatású maróanyagokból és oldószerekből állnak, vagyis az előbbi két csoportba tartozó anyagok kombinációi.
Csiszoló és fényező anyagok
A csiszolóanyagok a mázolás előtti felület (alap) vagy tapaszréteg egyenletessé koptatására vagy az egymás után következő rétegek felületi érdesítésére valók. (Kedvezőbb a tapadás.) A csiszolóanyagok természetes és mesterséges eredetűek, ill. megjelenésük szerint csiszolószemcsék, csiszolókövek, csiszolólapok (papír, vászon, műanyag stb.) lehetnek. Fontosabb közülük:
A természetes habkövek
Laza szerkezetű, vulkanikus eredetű, habosított szilikátok, tufák. Elsősorban fafelületek, faátvonó tapaszok csiszolására alkalmasak. Zománcfestékkel mázolt, lakkozott felület csiszolására a legjobbak.
A mesterséges csiszolókövek és habkövek
Szervetlen, javarészt ásványi eredetű, különféle szemcsenagyságú csiszolószemcsék mesterséges ragasztóanyagokkal kocka vagy téglalap alakúra sajtolt idomok. Méretük általában 12 x 8 x 6 cm.
Csiszolószemcsék
Finomságukat négy fokozatban, arab, a kötés szilárdságát (keménységét) pedig római számokkal jelölik. A csiszolószemcsék olyan érdes, rideg, nagy keménységű természetes vagy mesterséges anyagok, amelyeket elsősorban gépi úton, sűrített levegővel végzett csiszoláshoz, vagy megfelelő ragasztóanyaggal papírvászon stb. lemezekre rögzítve mesterséges csiszolólemezek gyártására használnak. Fontosabb csiszolószemcsék: kvarchomok, gránit, üvegpor, meteoritszemcse, szilícium-karbid (karborundum), elektrokorund, bór-karbid vagy bór-nitrid, ipari gyémánt (karbonádó, bort) stb.
A csiszolópapír vagy csiszolóvászon
Az előbbi szemcsékből készül oly módon, hogy meghatározott szemcsenagyságú frakciót (szitálással osztályozott részt) papírlemezre vagy textilszövedékre ragasztanak. A ragasztóanyag és papír, ill. textil minősége alapján a csiszolópapír vagy -vászon lehet vízálló (tehát nedves csiszolásra is alkalmas) vagy nem vízálló.
Szemcsenagyság szerint általában öt finomsági fokozatot jelölnek meg. Az igen durva minőségű csiszolóvásznat kizárólag fa- és fémfelületek, a durva és közepes finomságút főleg tapaszrétegek, a finomszemcséset az egyes festékrétegek tapadását biztosító érdesítő csiszolásra, az igen finom szemcsézetűt pedig kész zománcfesték-bevonatok polírozás (fényesítés) előtti csiszolására fényezési munkákhoz használják.
A csiszolópaszták
Finom szemcsézetű csiszolóanyagok műviasz- és ásvány-olaj-szuszpenzióban. Főleg nitro- és nitrokombinációs zománcfesték-bevonatok finom felületi csiszolására alkalmasak. Kézi és gépi csiszoláshoz egyaránt használatosak.
A polírozó (fényező) paszták
Az előbbivel teljesen azonos felépítésű, igen finom csiszolóanyagot tartalmazó vagy azoktól mentes, különféle márkanéven forgalomba kerülő készítmények. A zománcfesték-bevonatok felületi simaságát, fényét fokozzák. Hasonló rendeltetésű termék a polírvíz is.
Pórustelítő (beeresztő) impregnáló anyagok
A pórustelítők azok a folyékony halmazállapotú anyagok, amelyeket a pórusos szerkezeti anyagok teljes keresztmetszetén vagy bizonyos felületi rétegében levő pórusok kitöltéséhez, átitatásához használnak, az alapozó festékbevonatok felhordása előtt. A beeresztőanyagok helyes vagy helytelen használatától az egész bevonatrendszer élettartama, tartóssága függ. (Helytelenül a beeresztőanyagokat alapozóknak, alapozó oldatoknak, „grundoknak” is nevezik, amelyek a technológiai előírásokban gyakran súlyosabb megtévesztést okozhatnak.)
A telítő- vagy beeresztőanyagokra vonatkozó követelmények:
- A mázolandó szerkezeti anyag pórusait – térfogatváltozás nélkül – legalább olyan felületi mélységben töltsék ki, amely kizárja, hogy a pórusokban levő levegő, gáz, vízgőz stb. hő okozta kiterjedése és összehúzódása a bevonatra káros, feszítő, lazító hatást fejtsen ki.
- A felületi réteg pórusaiból a levegőt, vízgőzt, gázokat szorítsák ki, és minél mélyebb rétegbe szívódjanak be.
- A felületi réteg pórusaihoz teljesen és rugalmasan tapadjanak; elválásra ne legyenek hajlamosak.
- Az alap felületi rétegének pórusait a felület síkjával egyezően töltsék ki, de határozott filmréteget ne képezzenek.
- A pórusokban és a felületen levő, portalanítással esetleg nehezen eltávolítható, lazán tapadó részecskéket szilárdan rögzítsék.
- Penészedésre, gombásodásra ne legyenek hajlamosak.
- Vízfelvételük, ill. víz hatására bekövetkező duzzadási hajlamuk minél kisebb legyen, ill. a légköri páratartalom ingadozására ne legyenek érzékenyek.
- A felület- vagy tapasz-festékréteg anyagára káros vegyi hatást ne fejtsenek ki.
- Egészségvédelmi, gazdaságossági és egyéb szempontból is kedvező eredménnyel legyenek felhasználhatók.
A telítőanyagokkal szembeni követelmények kielégítése
A telítőanyagok a fenti követelmények kielégítésével biztosítsák a tapaszréteg- és festékbevonat felülethez való tapadását, ez pedig a bevonat élettartama szempontjából alapvető követelmény. Természetesen ezeket a követelményeket nem minden beeresztőanyag elégíti ki. Ebből következik, hogy az egyes szerkezeti anyagok mázolás előtti beeresztéséhez a felület porozitása, szilárdsága, vegyi felépítése, nedvességtartalma, valamint környezeti igénybevétele stb. szerint más és más tulajdonságú anyagokat kell felhasználni.
Mire alkalmas a lenolajkence?
A műgyanták elterjedése ellenére, pl. fafelületek beeresztésére mindmáig legalkalmasabb anyag a lenolajkence vagy más hasonló tulajdonságú, száradó növényi olaj, 15-20%-os lakkbenzines hígításban. Ennek egyrészt az az oka, hogy a lenolajkence viszonylag hígfolyós (alacsony viszkozitású), tehát jelentős hígítása nem szükséges ahhoz, hogy a pórusokba mélyen beszívódjék (szemben a műgyantákkal). Ezt a lényeges eltérést az alábbi ábrák szemléltetik.
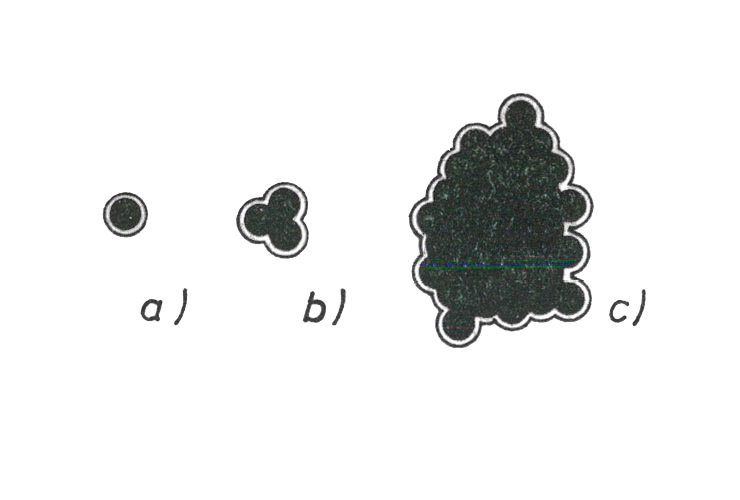
Fontosabb beeresztőanyagok molekulaméreteinek szemléltetése.
a) egyes molekulákból álló kötőanyag (pl. lenolaj);
b) kevés molekulából álló molekulacsoport, azaz alacsony polimerizációs fokú kötőanyag (pl. lenolajkence, esetleg standolaj);
c) óriás molekulájú, azaz magas polimerizációs fokú molekulacsoport (pl. alkidgyanta, általában a műgyanták).
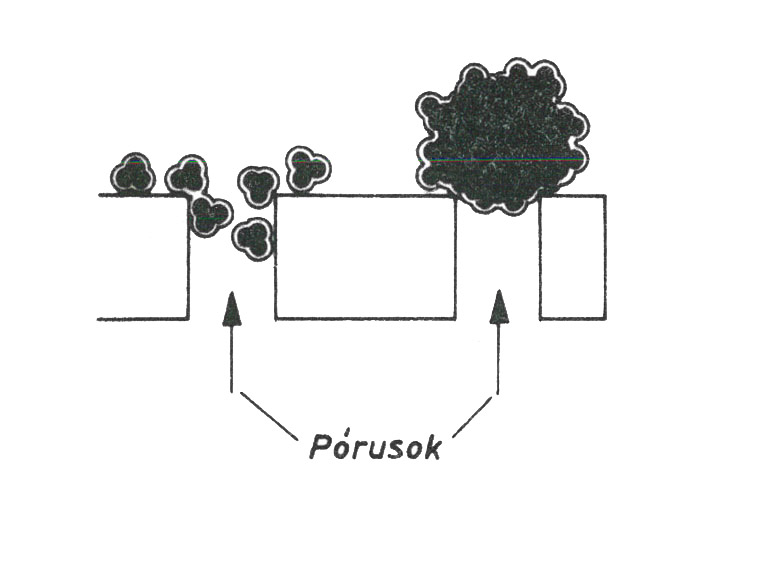
A kis molekulasúlyú beeresztőanyag a fa pórusaiba képes hatolni (pl. lenolaj, lenolajkence), a nagy molekulasúlyú műgyanta (pl. alkidgyanta, szintetikus lakk) mintegy fennakad a pórusok felületén, alig hatol a pórusokba
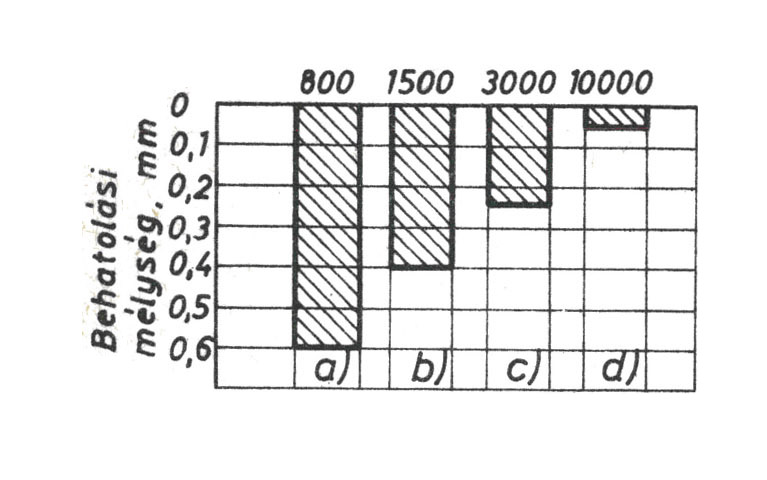
A molekulák behatolási mélysége a fa pórusaiba, a molekulasúly függvényében.
a) lenolaj;
b) lenolajkence;
c) lenstandolaj;
d) alkidgyantalakk (a behatolás a fák pórusaiba a telítőanyagok molekulasúlyának növekedésével csökken).
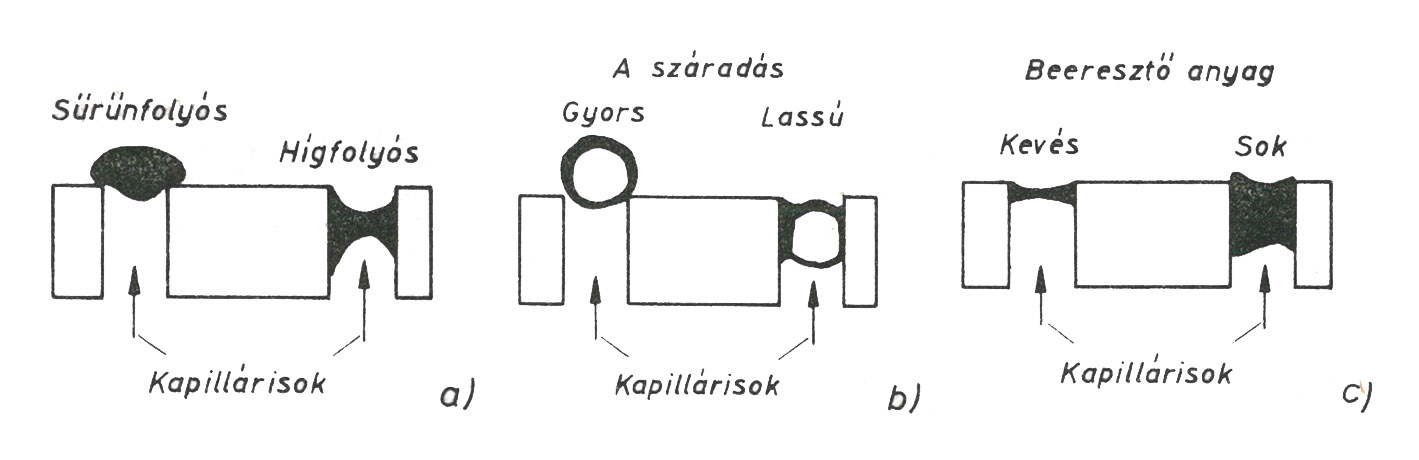
A beeresztőanyag behatolása a pórusokba.
a) magasabb hőmérsékleten a beeresztő hígfolyósabbá válik (viszkozitása csökken), s így a pórusokba mélyebben szívódik be;
b) gyorsan száradó beeresztőanyag a felületen hamar filmet képez, vagy besűrűsödik és nem képes a pórusokba hatolni;
c) csak a kellő mennyiségben adagolt beeresztőanyag töltheti ki a pórusokat.
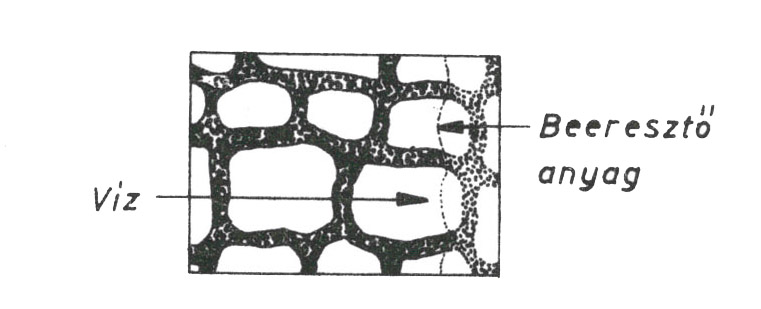
Nedves pórusú alap beeresztése.
A beeresztőanyag (grund) csak abban az esetben képes kellő mennyiségben a pórusokba hatolni, ha azokat más anyag (rendszerint víz) nem tölti ki.
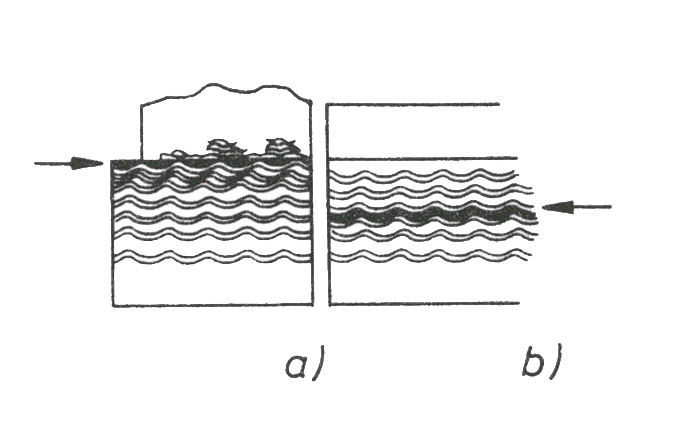
A duzzadó és nem duzzadó beeresztőanyag használatának következményei.
a) nem duzzadó beeresztőanyag viselkedése: az alapból elpárolgó nedvesség csak a határterületen talál először ellenállásra és ott a gőznyomás a festékbevonat felhólyagzását, leveles leválását idézi elő (ilyen pl. alkidgyanta fafelületen);
b) duzzadásra hajlamos telítőanyag viselkedése: itt a fa pórusaiba beszívódott nedvesség nem kerül a felületre és nem okoz hólyagzást, hanem mérsékelt duzzadást idéz elő.
Ugyanakkor a lenolajkence oxigénfelvétellel szárad, tehát térfogatát növeli, ezért az elpárolgó oldószer helyét a megnövekedett térfogat foglalja el, s ez gyakorlatilag a pórusok térfogatának teljes kitöltéséhez vezet.
A lenolajkence előnyei, hátrányai
Bár a vízzel, légköri nedvességgel szemben a lenolajkence kevésbé ellenálló, mint sok műgyanta, ez nem jelent túlzott hátrányt. A lenolajkence vízfelvétel hatására ui. erősen duzzad, egyben térfogatát is növeli, és így a fa pórusait még inkább kitölteni igyekszik. Ezáltal a faszerkezetek vízfelvételét lényegesen csökkenti, tehát mintegy szabályozó szerepet játszik.
Érdekes, hogy hasonló az előnye faszerkezetek beeresztésénél a poli(vinil-acetát)-műgyanta vizes diszperziójának is, amely még nagy nedvességtartalmú (27-30%) fa pórusaiba is beszívódik, és emellett a faanyag lassú, előnyös kiszáradását is elősegíti.
Mázolás: felület-előkészítő és felületkezelő szerek
Vegyi hatású felületkezelő szerek
Az e csoportba tartozó anyagok elsősorban az acélszerkezetek korrózió elleni védelmére használatosak.
Közös jellemzőjük a következők:
- Vegyi hatást fejtenek ki, azaz a rozsdaréteget vegyi úton átalakítják. A felületet mintegy stabilizálják, azáltal, hogy azon vízben nem oldható, a további festékrétegeket nem zavaró, sószerű réteget képeznek. Hatóanyaguk rendszerint foszforsav (esetleg kevés sósav és korróziógátló inhibitor-adalék, pl. kálium-kromát, nátrium-nitrit stb.). A foszforsav ui. a rozsdát vízben oldhatatlan ferrofoszfát alakjában eltávolítja, ill. átalakítja.
- Alapvetően abban különböznek a korróziógátló alapozó festékektől, hogy a felületkezelő szerek nem képeznek jellemző vastagságú védőréteget, mivel az alapot csak 10- 15 mikronos rétegvastagságban stabilizálják, és így legfeljebb néhány (4-8) napig gátolják a felület rozsdásodási folyamatát. Ez azt jelenti, hogy a velük kezelt felületet ez időn belül még megfelelő alapozóréteggel vagy korrózió ellen védőréteggel kell ellátni.
- Több felületkezelő szer alkalmazásakor esetleg zavaró melléktermékek (pl. rideg, szívós réteg) is keletkezhetnek, amelyeket vizes öblítéssel vagy egyéb úton el kell távolítani.
- A vegyi felületkezelő szerekhez természetesen nem szükséges fémtiszta felület, hanem csak a laza (szálló-) rozsdát, reveréteget stb. kell eltávolítani a felületről.
- Sok esetben (pl. tagolt acélszerkezetekhez) a vegyi felületkezelők eredményesen és előnyösen használhatók, bár gondos körültekintést igényelnek.
Korrózió ellen átmenetileg védő anyagok
A korrózió elleni védelem területén egyre nagyobb mértékben alkalmaznak ideiglenes rendeltetésű védőbevonatokat. Ezek viszonylag rövidebb időtartamra (hetekre, hónapokra, pl. egy szállítási, készletezési, tárolási időszak ra) átmenetileg megbízható védelmet nyújtanak a korróziós károsodások ellen. Az e csoportba sorolható anyagok fontossága korántsem lebecsülendő.
Ezek a gyártmányok ásványolaj-származékok (zsírok, viaszok), olcsóbb műgyanták és rendszerint tartalmaznak még különféle inhibitor-adalékokat is.
A rájuk vonatkozó általános követelmények röviden így foglalhatók össze:
- könnyen felhordhatok és nyom nélkül eltávolíthatók legyenek;
- a végleges korrózió ellen védő réteg kialakítását ne nehezítsék meg;
- a védett szerkezeti anyag felületét ne károsítsák, azt zavaró mértékben ne szennyezzék, s végül
- hatékonyak legyenek, azaz a tervezett időn belüli védelmet megbízhatóan teljesítsék.
Tapadásjavító vagy tapadást létesítő felületátvonó alapozók
Az építési munkák új műszaki megoldásainak bevezetésekor gyakran felmerül az a követelmény, hogy egymással nehezen vagy egyáltalán nem köthető szerkezeti anyagok között kell tartós kapcsolatot létesíteni. Leginkább felvetődnek ezek a problémák pl. a ragasztásos kötés, a hézagtömítés, tapaszolás, felületátvonás, korrózió elleni védelem, burkolómunkák stb. esetében.
Nehézségek az egyes anyagok ragasztásával, tapaszolásával kapcsolatban
Ismeretes, hogy a nagy porozitású szerkezeti anyagokat, műanyagokat és egyes fémeket (pl. horgany, horganyzott acél, réz, ón, alumínium stb.), az üveget, mázas kerámiákat stb. igen körülményes ragasztóréteggel, tapaszolással ellátni, mert felületükön olyan erők hatnak, melyek a kapcsolatot teljesen bizonytalanná teszik. Egyes műanyagokat, elektrosztatikus feltöltődésük miatt, nem lehet közbenső tapadásjavító réteg kialakítása nélkül pl. ragasztott kötéssel rögzíteni.
Eredmény: speciális alapozóanyagok kifejlesztése
Ez a probléma irányította a figyelmet arra, hogy olyan tapadásjavító közvetítő réteget képező alapozóanyagokat dolgozzanak ki, amelyek egyes egymástól eltérő sajátosságú szerkezeti anyagok és elemek közötti kapcsolat megbízható kialakítását hozzák létre.
Korrózió elleni védelemre néhány gyártmány forgalomba került ugyan, tehát nem kimondottan tapadásjavító rendeltetéssel, de ezt a követelményt is betölti, a cink-kromátos könnyűfém alapozó, a könnyűfém alapozó, a korróziógátló alapozó stb., amelyek segítségével új horgany- és horganyzott acéllemez-felületen is megbízhatóan tapadó festékbevonat-rendszer építhető fel.
A tapadásjavító átvonó (vagy alapozó) anyagokra vonatkozó általános követelmények a következők
- Rendeltetésüket káros átalakulás nélkül töltsék be a tervezett tartóssági időn belül.
- Kezelésük egyszerű, gyors, veszteségmentes legyen. Ilyen értelemben előnyösek az egyalkotós (fizikai úton száradó), esetleg a kétösszetevős átvonó-anyagok.
- A tapadást létrehozó át vonóanyagok rövid időn belül (15- 20 perc) száradjanak, átvonhatók, ill. rendeltetésszerűen igénybe vehetők legyenek.
- Szélsőséges körülmények között, de legalább – 5 °C alsó hőmérséklethatárig felhasználhatók legyenek.
- Ne legyenek mérgező és egészségre ártalmas hatásúak.
- Legalább 6-8 hónapos szavatosságú tárolási idejük és biztonságos, veszteségmentes felhasználást lehetővé tevő csomagolásúak legyenek.
- Szórással, ecseteléssel, hengerléssel, esetleg merítéssel stb. egyenletes rétegben felhordhatók legyenek.
- Minél több szerkezeti anyag felületére alkalmasak, de egyben jól elhatárolhatók legyenek.
Tapaszok, kittek, felületkiegyenlítő és pórustömítő anyagok
A tapaszok (vagy kittek, helytelenül gittek) azok az anyagok, amelyek az alapozott (vagy előkezelt) felületre felhordva az egyenlőtlenségeket (hézagok, lyukacsok, repedések stb.) kitöltik.
A tapaszokat csoportosíthatjuk:
- konzisztenciájuk (megjelenési állapotuk), ill. felhordási lehetőségük szerint, pl. késtapaszok, szórótapaszok (fröccskittek stb.),
- kötőanyaguk, vegyi felépítésük szerint (pl. olajos, nitroalkidgyantás, epoxi- stb. alapú tapaszok),
- felhasználási területük szerint (pl. faátvonó, fémtapasz, korróziógátló stb. tapaszok).
A tapaszokra vonatkozó általános követelmények a következők.
- Az alaphoz kifogástalanul tapadjanak, arra káros vegyi hatást (pl. rozsdásodást, maró hatást stb.) ne fejtsenek ki.
- A hézagokat, lyukakat gyakorlatilag térfogatváltozás nélkül töltsék ki, repedésre, zsugorodásra ne legyenek hajlamosak.
- Legalább olyan rugalmasságúak legyenek, ami a felület igénybevétele során (hajlító, mechanikai, rezgő stb. igénybevétel) repedésre, az alaptól való elváláshoz nem vezet.
- Száradás, kötés, felhordás, kezelés, tárolás szempontjából a termelékeny felhordás, utólagos kezelés (pl. csiszolás) és felhasználás, gazdaságosság stb. általános követelményeit is elégítsék ki.
Mire kell vigyázni tapasz alkalmazásakor?
Különösen veszélyes hibák forrása lehet a felületet egybefüggően borító vastag tapaszréteg, amely pl. faszerkezetek, járművek stb. mázolásakor gyakori jelenség. Mázolás szempontjából az a felület a legelőnyösebb, amely tapaszolásra egyáltalán nem szorul. Ezzel ellentétben sok technológiai utasítás – helytelenül – a teljes felület egybefüggő tapaszréteg átvonását írja elő (pl. bútorok mázolásakor).
A pórustömítők célja
A pórustömítőket elsősorban lakkozással készült pórusos fafelületek át-vonására használják, egyrészt a felület szívóképességének csökkentése, másrészt a fafelület jellegzetes rajzolatainak kiemelése érdekében.
Világos színű felületen pl. a sötétebb pórustömítő a rajzolatokat kiemeli, vagy fordítva. Hazánkban világos és sötét diófa színű pórustömítőt hoznak ilyen célra forgalomba. Ezek finom szemcséjű pigmentekből, valamint növényi olajos vagy műgyanta-alapú kötőanyagokból állnak, 70-80% testtartalommal. Simítóacéllal hordhatók fel, s 20-24 órai száradás után csiszolhatok és nitrolakkal át vonhatók. A pórustömítők tapaszok helyett nem használhatók. A tapaszolás elvét az alábbi ábra szemlélteti.
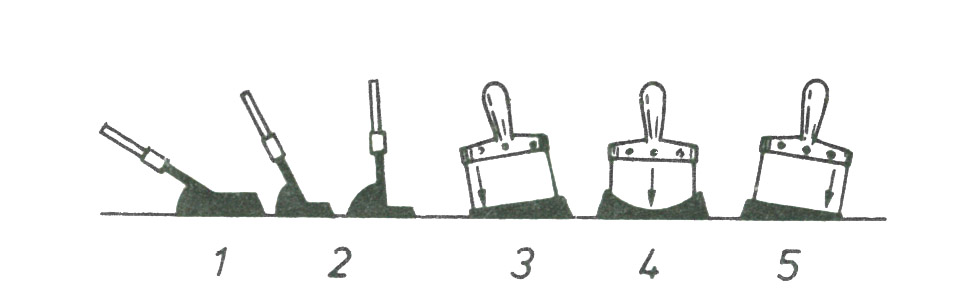
A tapaszolás elvének szemléltetése.
1 – vastag tapaszréteg;
2 – vékony tapaszréteg;
3 – ferde, egyenlőtlen vastagságú tapaszréteg;
4 – árkos, homorú tapaszréteg;
5 – ferde, egyenlőtlen tapaszréteg
A mázolásra alkalmas fontosabb szerkezeti anyagok jellemző tulajdonságai
Mázolástechnikai szempontból megkülönböztetett jelentőségűek a szerkezeti anyagoknak mint alapoknak a felépítése és jellemző viselkedésük. Ilyen vonatkozásban a következő szerkezeti anyagcsoportok ismerete fontos a mázolószakember számára.
Faszerkezetek
A fa növényi sejtekből felépített, természetes szerkezeti anyag. A természetben előforduló több ezer fafajta közül mintegy 400-félét használnak szerkezeti anyagként. Az egyes fafajták tulajdonságai felépítésük, helyi előfordulásuk szerint nagymértékben változnak. Teljes körű favédelem, 30 év garanciával.
A fa alkotóelemei
A fa sejtjei általában 45-50%-ban cellulózmolekulákból állnak. Ez hosszú láncú, kristályos szerkezetű szerves vegyület. A rostokat merevítő, tehát a fatest szilárdságát növelő másik építőanyag a még nem tisztázott szerkezetű lignin 20-30% mennyiségben található a fában. Hasonló a szerepük a pentozánoknak is, lombos fákban 20-30%-ban, fenyőfélékben 9-15%-ban vannak jelen. A fa anyagában előfordulnak még keményítők, cukrok, fehérjék, zsírok, olajok, gyanták és balzsamok (pl. a fenyőfákban mintegy 6-14%-nyi mennyiségben!), csersav és hasonló szerves vegyületek, továbbá kalcium-oxalát, kalcium- és kálium-karbonát és egyéb szervetlen vegyületek.
A fatestet felépítő sejtek méretétől, felépítésétől és vegyi összetételétől függ elsősorban a faanyag legtöbb jellemzője, pl. fajlagos tömeg, szilárdsági értékek, porozitás stb. A faanyag bonyolult felépítését az alábbi ábrák szemléltetik.
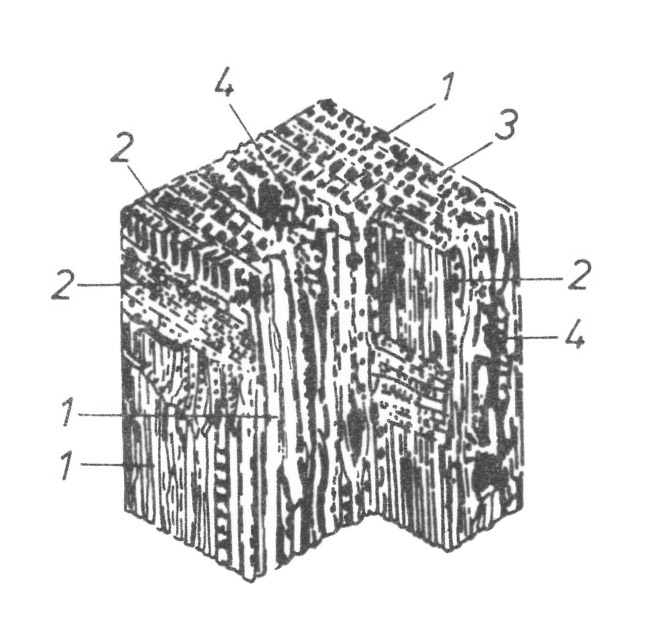
Lombosfa törzséből kimetszett kocka.
1 – edény (trachea);
2 – edény lépcsős áttöréssel
3 – szilárdító (libriform) sejt;
4 – alapsejtekből (parenchim) felépülő bélsugár (200:1)
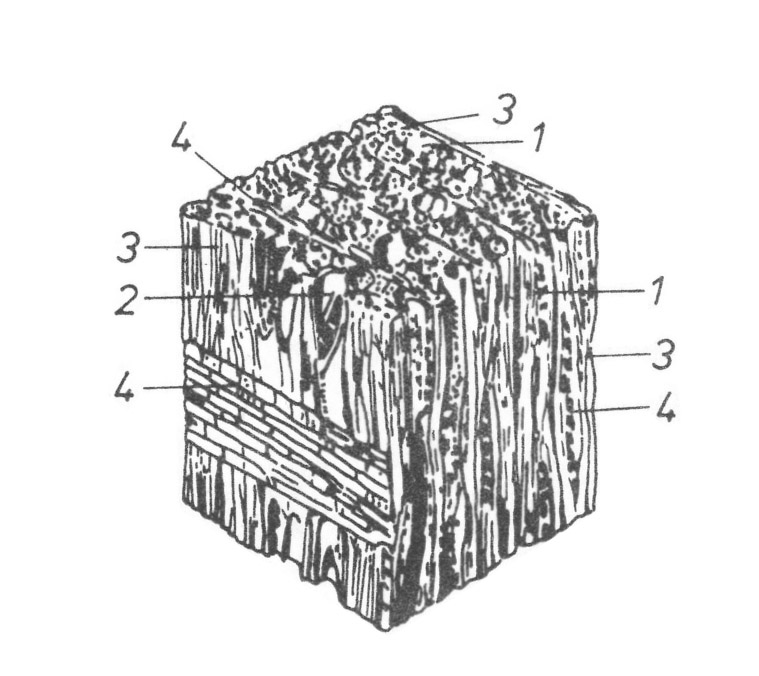
Fenyőfa törzséből kimetszett kocka.
1 – áledény (tracheida);
2 – bélsugár;
3 – gyantajárat;
4 – évgyűrűhatár (200:1)
A fák rostjainak pórusátmérője a fa vízfelvételét és -leadását, valamint alakváltozását nagyban befolyásolja. A rostok pórusátmérői alapján megkülönböztetnek bőpórusú (pl. tölgy) és tömörpórusú (pl. mahagóni) fákat. Az előbbiek pórusai nehezen zárhatók le, emiatt pl. lakkozásnál különleges kezelésre szorulnak.
Egyes tűlevelű fák (pl. vörösfenyő, erdeifenyő) anyagát a gyantajáratok hálózzák be. Ezeket a gyantával kitöltött metszeteket mázolás előtt el kell távolítani. Ehhez hasonlóan viszont több lombos fa (pl. tölgy, nemes gesztenye) járatai sok csersavat és pirogallolt tartalmaznak, amelyek lakkozásakor zavaró elszíneződés keletkezhet. (Pl. a tölgyfa parkettát savra keményedő lakkal átvonva kékeslilás-fekete elszíneződés keletkezhet, a sósavas edzőoldat vasszennyeződése miatt.)
A természetes fafajták felosztását az alábbi táblázat ismerteti.
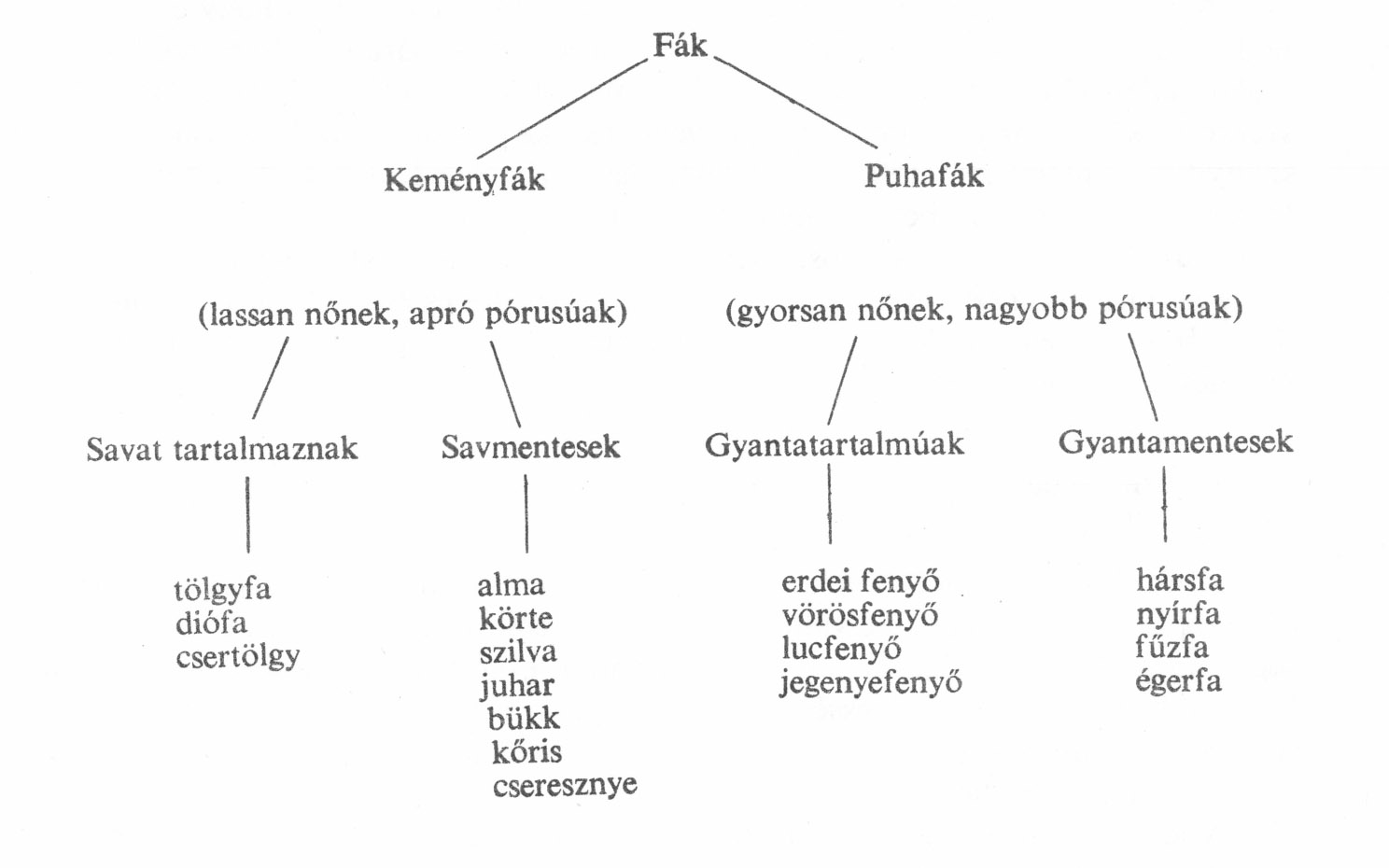
A faanyagok felosztása
Az egyes fafajták műszaki jellemzőit az évgyűrűk, ill. sejtjeiknek méretei és elhelyezkedése határozza meg
Ezek alapján a fa anizotrop közeg, mert az egyes jellemzők értéke a mérés irányától függően változik. Az ilyen szempontból megkülönböztetett irányokat, illetve metszési síkokat az alábbi ábra mutatja.
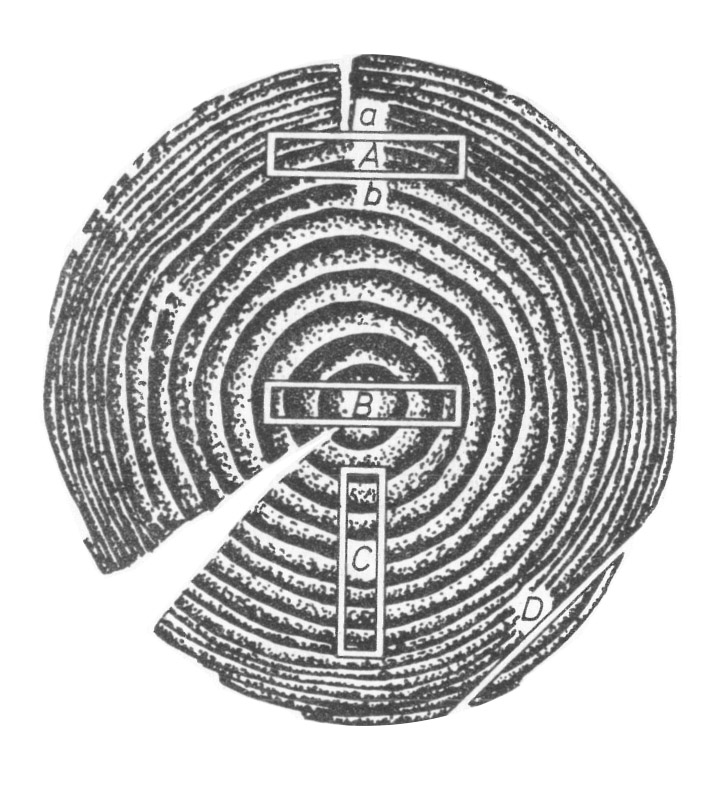
Fatörzs fontosabb metszési síkjai.
A – sugárirányú hosszmetszet;
B – hosszmetszet;
C – keresztmetszet (bütümetszet);
D – húr- vagy érintő irányú metszet
A faanyag jellegzetes hajszálcsöves felépítéséből következik, hogy erősen nedvszívó, higroszkópos tulajdonságú. Mivel a rostok, járatok elrendeződése szabálytalan, a nyersfa víztartalma, ill. a szárazfa vízfelvétele a faszerkezet különböző részeiben nem egyenletes.
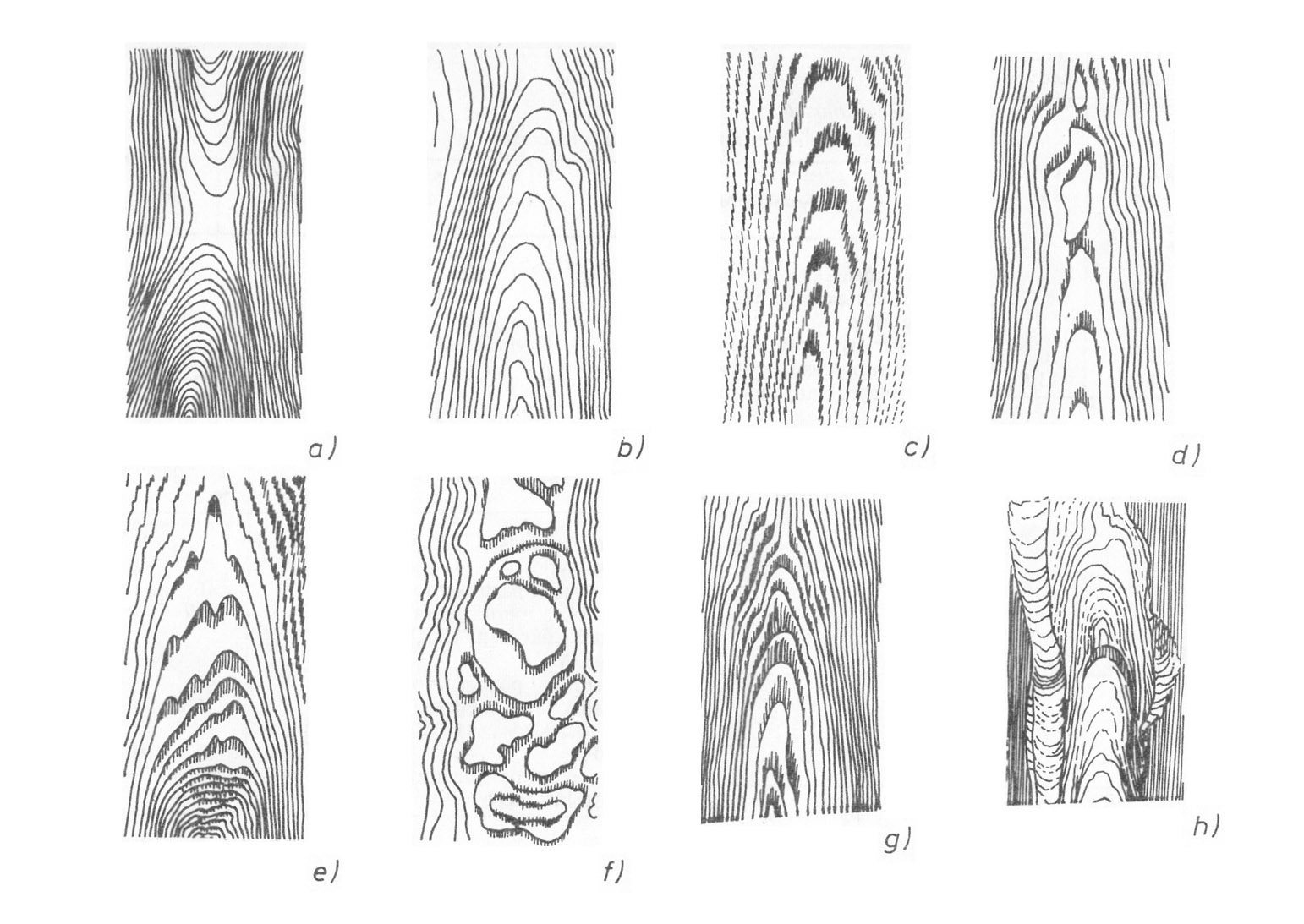
Néhány fontosabb keményfa jellemző faerezési rajzolata.
a) ciprus;
b) cédrus;
c) szilfa;
d) sárga fenyőfa;
e) angol kőrisfa;
f) magyar kőrisfa;
g) amerikai diófa;
h) rózsafa
Az élő- a szárazfa súlyához viszonyítva mintegy 30- 150% vizet tartalmaz (nettó nedvesség). A víz eloszlása a fa egyes részein belül nagy eltéréseket mutat. A nedvességtartalom műszaki szempontból igen fontos, mert a fa nedvességfelvétel hatására dagad (térfogata nő), míg száradáskor zsugorodik. A dagadás és zsugorodás nem minden irányban azonos.
A faanyagok vízfelvétel okozta dagadása az alábbi átlagértékek között ingadozik:
rostirányban | 0,6- 2,7% |
sugárirányban | 3- 5% |
érintőleges irányban | 6,5- 13% |
A faszerkezetek nedvességtartalma
A mázolásos felületvédelem egyik célja éppen az, hogy a faszerkezeteket a nedvesség okozta káros elváltozásoktól megvédje. A faszerkezetek nedvességtartalma (ha csapadék nem éri) elsősorban a levegő relatív páratartalmától függ. Adott relatív légnedvesség esetén a faanyagokra jellemző higroszkópos egyensúlyi állapot alakul ki, amelynél a faszerkezet nedvességet nem ad le, de nem is vesz fel.
A levegőn tárolt, ázásnak ki nem tett, légszáraz faszerkezetek nedvességtartalma általában 12-18%, míg a mesterségesen szárított és legfeljebb 50% relatív páratartalmú légtérben tárolt faszerkezeteké 8-12%. A faszerkezetek nedvességtartalma igen lényeges mázolástechnikai szempontból is.
Egy festékbevonat-rendszer ui. a faszerkezetek felületén biztosan tapadó réteget csak akkor képezhet, ha a fa anyaga egy bizonyos egyensúlyi nedvességtartalomnál több nedvességet nem tartalmaz. A faanyag nedvességtartalmára az egyes festékanyagok nem egyformán érzékenyek.
Műszaki szempontból tehát igen fontos a mázolási műveletek előtt a faszerkezetek nedvességtartalmának ellenőrzése
A faszerkezetek nedvességtartalmának meghatározására fémtüskés, elektromos fa nedvességmérőket használnak. A faanyag gyakran igen veszélyes károsodását különféle növényi és állati kártevők is okozhatják. Egyes penészgombafajták elszíneződést, mások korhadást, biológiai korróziós folyamatokat idéznek elő. Egyik legveszélyesebb ilyen károsító a könnyező házigomba, amely igen gyorsan terjed, és rendkívül nehéz ellene védekezni. Mázolástechnikai szempontból a következő mesterséges faanyagok a természetesektől gyakran eltérő tulajdonságúak.
Rétegelt (enyvezett) falemez
Természetes faanyagokból előállított, furnér rétegekből álló, mindig a két szomszédos réteg szálirányára merőlegesen összeragasztott lemez. Hazánkban főleg bükkfából, ritkábban éger-, hárs- és cserfából készül, 3-5-7 stb. réteggel.
Faforgácslap
Cellulóztartalmú anyagok aprított hulladékaiból (pl. faforgács kender pozdorja, rizsháncs stb.) műgyanta-alapú ragasztókkal mesterségesen előállított faanyag. Tulajdonságai a lap minden irányában azonosan változnak. Légnedvesség ingadozására kevésbé érzékeny, ezért zsugorodásra, dagadásra kevésbé hajlamos. Ezzel szemben vízfelvétele sokkal nagyobb a természetes faanyagokénál. A lap szélrészei különösen érzékenyek a vízfelvételre, légköri hatásokra, így mázolásakor külön nedvesség elleni szigeteléssel kell ellátni. Nedvességtartalma 8- 12% között változik. Jóval nagyobb pórusai miatt, mázoláskor különleges kezelést igényel.
Pozdorjalap
Kender feldolgozási melléktermékből, a kender-pozdorjából nyert, nagy szilárdságú, rostos szerkezeti anyag. Tulajdonságai a faforgácslapéhoz állnak közel.
Farostlemez
Növényi, főleg farostokból, kötőanyaggal vagy anélkül, nagy nyomással sajtolt, kiváló tulajdonságú, mesterséges szerkezetű faanyag. Előállítása jelenleg is igen biztató fejlődés alatt áll. Tulajdonságai függetlenek a lap irányától; ezért a természetes faanyagokat előnyösebben helyettesíti minden olyan esetben, amikor a fa rajzolata nem követelmény. Felhasználási területe igen sokféle. A 100-300 kg/m3 (vagy ennél kisebb) fajlagos tömegű lemezeket főleg hang- és hőszigetelésre, a félkemény, kemény és különlegesen kemény 500- 1050 kg/m3 fajlagos tömegűeket pedig a bútoriparban, faszerkezetek, padlóburkolatok készítésére, sőt házak építésére is előnyösen használják fel.
Farostlemezek nedvességtartalma
A félkemény és kemény farostlemezek nedvességtartalma általában 5-7 %, gyakorlatilag teljesen érzéketlenek a környező légtér páratartalmára. Még 24 órai vízben áztatás után is legfeljebb 10- 18% nedvességet vesznek fel, vagyis lényegesen kevesebbet, mint a természetes faanyagok a környező légtérből!
Farostlemezek kezelése
A farostlemezek mázolásakor ügyelni kell arra, hogy felületük gyakran olyan járulékos szennyeződéseket (pl. paraffinolaj, fenolnyomok stb.) tartalmaz, amelyek a festékbevonatok száradását, tapadását gátolják, vagy egyéb bevonat-meghibásodásokat idézhetnek elő. Szigetelésükről vagy eltávolításukról gondoskodni kell. A farostlemezek gombamentesítése általában nem szükséges, mert a kötéshez leggyakrabban felhasznált fenolgyanta erősen gombaölő hatású.
Fémszerkezetek
A szerkezeti anyagok egyik legnagyobb csoportját a fémek alkotják.
Mázolástechnikai szempontból az alábbi fontos közös sajátságuk fontos:
- A fémek felületén általában, a feldolgozás (pl. hengerlés) és a légköri tényezők hatására, jellegzetes, az egyes fémek szerint eltérő tulajdonságú, laza vagy nehezen eltávolítható korrodált réteg képződik, amely a festékbevonat tapadását bizonytalanná teszi. Ilyen korróziós képződmény a közismert hengerlési reveréteg, amely az acélok felületén a megmunkálás közben hő hatására keletkezik. Főleg vas-oxidokból áll. A rozsdaréteg a légköri tényezők (elsősorban oxigén, vízgőz és szén-dioxid), valamint a vegyi anyagok hatására alakult vas-oxid-hidrátokból, esetleg -karbonátokból áll. Ezek eltávolítása nemcsak a felület stabilizálása és a bevonat megakadályozása miatt szükséges. A nemesfémek felületvédelmére nincs szükség.
- A fémek felületén, pl. a megmunkálásuk során lerakódott olyan egyéb szennyeződések (pl. zsírok, olajok stb.) is találhatók, amelyek eltávolítása szintén szükséges a festékbevonat tapadása érdekében.
- A fémek felülete általában egyenletes, elhanyagolható porozitású, tehát a festékanyag a pórusokba nem szívódhat be, mint pl. a fa- és falszerkezetek esetében stb. Éppen ezért a fémek felületének gondos letisztítása fokozottabb követelmény.
- Egyes fémek felületén nemcsak fizikai tapadást kell a festékbevonat számára nyújtani, hanem vegyi kezeléssel a felületet stabilizálni is kell.
A gyakorlatban az alábbi fémszerkezetek felületét szokták általában védőmázolással ellátni:
- acél, horganyzott acél,
- horgany,
- alumínium és ötvözetei,
- esetleg réz és rézötvözetek.
Egyéb szerkezeti anyagok
Síküvegek mázolására nem felületvédelmi, hanem rendszerint díszítő céllal kerül sor. Általában a huzalhálós, a homokfúvással vagy savmaratással mattírozott, valamint a közönséges gépi húzású és hengerelt síküvegeket mázolják. Tartós kapcsolat a festékbevonatok és a síküveg felületei között nem hozható létre. Alapvető szabály, hogy az üveg felületét előzetesen gondosan zsírtalanítani kell. Viszonylag tartós festékbevonatot kizárólag igen rugalmas tulajdonságú festékanyagokkal (pl. olajfestékek) lehet elérni.
Papír, műbőr, textíliák stb. festését általában a feldolgozó üzemek végzik, így ezek mázolása tulajdonképpen nem sorolható az általános mázolási munkákhoz. Bevonásukra különleges festékanyagokat hoznak forgalomba, amelyek felhordásához a gyártóművek által megadott követelmények betartása szükséges.
Mázolómunkák előfeltételei
Kapcsolódás más építési munkákhoz
A mázolás előtt minden olyan befejező építési (építőmesteri) munkát teljesen el kell végezni, amelyek egyrészt akadályozhatnák a mázoló munkaműveleteket, másrészt a kész festékbevonatot károsíthatnák.
Így pl.:
- az üvegezett szerkezetek üvegtábláinak beépítése, a horony tapaszolása kész legyen, (tapaszolás előtt az üvegtábla tartószerkezetét alapozó mázolással kell ellátni);
- fűtőtestek (radiátorok) és csőszerelvények, csővezetékek mázolása előtt a rendszer nyomáspróbáját is el kell végezni; az összes szerelési munka teljesen kész állapotban legyen;
- a homlokzati nyílászáró szerkezetek mázolásakor a végleges felületképzés és beltéri szerkezeteknél a falfestés teljesen kész legyen;
- parkettázott helyiségekben a parketta lerakását, felgyalulását, készre csiszolását (esetleg alapozó lakkozását vagy pórustelítő beeresztését) a mázolás elkezdése előtt el kell végezni;
- szükség esetén – ha utólagos szerelési munka (pl. üzemzavarelhárítás) elvégzése elkerülhetetlen – a kész mázolás papír- vagy műanyagfólia-letakarással megvédhető;
- általában kerülni kell az olyan porképződéssel (vagy egyéb szennyeződéssel) járó munkákat, amelyek a mázolást károsíthatnák;
- villamos feszültség alatti berendezések (pl. távvezetéktartó acélszerkezetek, gépek, vezetékek stb.), egyéb üzemeltetésben levő szerkezetek mázolását mindaddig nem szabad elkezdeni, míg szabványos feszültségmentesítésüket (áramtalanításukat) el nem végezték, s ezt hitelesen vezetett naplóban nem rögzítették.
A mázolómunkák elvégzésének környezeti (klimatikus) feltételei
Mázolási munkát kizárólag olyan környezetben (munkatérben) szabad elkezdeni, ahol a festékréteg képzéséhez szükséges műveletek akadály nélkül elvégezhetők, és a kész bevonat károsodása nem fordulhat elő.
Nem szabad mázolási munkát végezni a következő körülmények között:
- Poros, huzatos helyiségben vagy olyan kültéri környezetben, ahol a még meg nem száradt bevonat szennyeződésével számolni lehet (pl. a homokszemcsék beleragadnak a festékrétegbe).
- Oxigénfelvétel száradó festékekkel és lakkokkal (ilyenek pl. az olajfestékek, olaj-, gyantalakkok és zománcfestékek, egyes műgyantaalapú lakkok és zománcfestékek stb.). Nem szabad mázolást végezni olyan dohos, nyirkos, rosszul szellőztetett helyiségekben, ahol a száradáshoz (filmképzéshez) szükséges légcsere és kb. 15-20 °C körüli hőmérséklet nem biztosítható.
- Különösen acél- és fémszerkezetek mázolását nem szabad akkor végezni, amikor a felületen (alapra) páralecsapódással lehet számolni (pl. a nagy páratelítettségű levegő jelentősen lehűl); általános követelmény, hogy a festékbevonat (vagy alap) teljes száradás előtt ne legyen kitéve csapadékvíz vagy bármilyen eredetű nedvesség hatásának.
- Nem szabad elkezdeni a festék- vagy lakkréteg felhordását olyan környezetben (munkatérben) sem, ahol a mérgező hatású és robbanásveszélyes oldószergőzök légcserével (szellőztetéssel) nem távolíthatók el. (Egyes lakkokból, pl. VILUPÁL parkettalakkból, még mérgező gázok is képződhetnek az oldószergőzök mellett.)
- Különösen gyorsan száradó lakkal, zománcfestékkel nem szabad erős huzatban mázolni, mert az oldószerek, hígítók gyors párolgása következtében a felület erősen lehűl, emiatt a légtérből pára csapódik a filmrétegre, s az foltosán kifehéredik vagy „bemattul”.
Az alapfelületre vonatkozó általános követelmények
A mázolást csak olyan szerkezeti anyag felületén szabad elkezdeni, amelyen a lakk- és festékbevonat-rendszer képzéséhez szükséges munkaműveletek megbízhatóan elvégezhetők.
Fontosabb követelmények a következők:
- Az alapfelület tiszta vagy megtisztítható legyen a zavaró mechanikai és vegyi szennyeződésektől.
- A mázolásra szánt szerkezet (alap) felülete ne legyen hajlamos olyan utólagos átalakulásra, amely a festékréteg károsodását előidézhetné (közismerten ilyen szerkezeti anyag pl. a nedves fa, amelyen a festékbevonat felhólyagosodik és lepattogzik).
- Az alapfelület ép és sérülésmentes legyen; sérüléseket, folytonossági hiányokat csak olyan mértékben tartalmazhat, amelyek a mázolás előkészítő műveletei során megbízhatóan kijavíthatok (szükség esetén a szerkezeti anyagot kell kicserélni megfelelő épségűre).
- Az alapfelület stabil vagy kezeléssel stabilizálható legyen, olyan értelemben, hogy a határfelületen (vagy a szerkezeti anyag belsőbb rétegében) a festékbevonatot károsító vegyi (vagy fizikai) folyamatok ne mehessenek végbe.
- A mázolásra, lakkozásra tervezett felületen azokat az általános minőségi követelményeket is biztosítani kell, amelyeket az anyagfelhasználási (gyári) útmutatók is előírnak.
Fajlagos anyagfelhasználás, anyagnormák
Ezzel kapcsolatban érdemes hangsúlyozni, hogy a fajlagos anyagfelhasználást igen sok tényező befolyásolja, s így azokat szinte esetenként a helyi körülmények figyelembevételével célszerű kísérleti (gyakorlati) próbával meghatározni. A fajlagos anyagfelhasználást pl. egy olaj- vagy zománcfesték, ill. lakk esetében a következő fontosabb tényezők befolyásolják.
Ezek a tényezők:
- A lakk- vagy festékanyag oldószertartalma (a hígítás mértéke). Minél nagyobb az oldószer tartalom, annál kisebb rétegvastagságú bevonat készíthető.
- A lakk- vagy festékanyagra jellemző fajlagos sűrűség, ill. fajlagos tömeg. Minél kisebb fajlagos sűrűségű (töltőanyagszegény) egy festékanyag, annál nagyobb felület lefedésére elegendő belőle 1 kg-nyi vagy liternyi mennyiség.
- A lakk- vagy festékanyag tixotrop jellege. Minél tixotrópabb a festékanyag, annál kisebb a felhordási anyagveszteség.
- Az alapfelület porozitása, szívóképessége. Minél nagyobb a porozitás, annál nagyobb a szívóképesség, tehát nehezebben (több anyaggal!) telíthetők a pórusok, így ennek megfelelően nagyobb a fajlagos anyagfelhasználás.
- Az alapfelület tagoltsága, ill. fajlagos felülete. Az alapfelület méretadatainál figyelembe kell venni a felület egyenlőtlenségeit, tagoltságát (pl. díszes rács esetén).
- A lakk- és festékanyag felhordásának külső körülményeit, továbbá a mázolási technika, a mázoló gyakorlottsága, lelkiismeretessége, szakmai tapasztalata stb.
- A szükséges rétegvastagság kialakítása. A szakmai gyakorlatban többféle számítás ismeretes a lakk- vagy festékanyag előírt rétegvastagságra vonatkoztatott anyagszükségletének kiszámítására. Ezek elméleti jelentőségűek, csak megközelítő értéket adnak, így realitásuk kétséges.
A reális fajlagos anyagfelhasználást a következőképpen kell megállapítani, s azt a megrendelővel (beruházóval) egyeztetni
A pontosan körülhatárolt, lemért és előkészített felületű alapot (pl. acélszerkezet) egy előzetesen legalább ± 5 g pontossággal lemért, használatra kész konzisztenciájúra hígított festékanyaggal be kell mázolni (ecseteléssel vagy szórással stb.), a jellemző üzemi körülmények között.
A kiindulási és a lemért felület mázolásának elvégzése után visszamaradt festékanyag mennyisége közötti különbség adja a felületre eső anyagszükségletet, természetesen az elhullási veszteséggel együtt. A festékréteg vastagságát száradás után méréssel kell meghatározni.
A munkaidő-szükséglet számítása
Különleges mázolómunkáknál vagy olyan esetben, amikor a helyi adottságok miatt nehezebb az egyes munkaműveletek elvégzése, feltétlenül szükséges a munkaidő-szükséglet meghatározása helyszíni mérésekkel és beépítése az egységárelemzésbe.
Munkaszervezési teendők
A mázolómunkák alapvető követelménye a munkaterület gondos előkészítése, a munkaműveletek zavartalan elvégzésének lehetővé tétele.
Ennek érdekében a következő szempontokat kell figyelembe venni:
- Különösen építés helyi mázolási munkáknál kell ügyelni arra, hogy azok más építőipari munkák elvégzését ne zavarják, szennyeződést stb. ne idézzenek elő, ill. megfordítva: á mázolást a közelben végzett más munkák ne akadályozzák, ill. károsodását ne idézzék elő.
- Az anyagokat előírás szerint kell tárolni. Gondoskodni kell a festékanyagok, oldószerek, hígítók, segédanyagok károsodás nélküli tárolásáról úgy, hogy azok folyamatosan a közvetlen felhasználás helyére legyenek továbbíthatók.
- A munkaműveleteket úgy kell ütemezni, hogy folyamatosan legyenek elvégezhetők. Ezt az építéshelyi körülmények, az egyéb helyi adottságok jelentősen befolyásolják. Ennek érdekében a munkaműveleteket úgy kell megszervezni, hogy időszükségletükbe az alapozó, közbenső és átvonó stb. rétegek száradási idejét is be kell építeni, munkafázis-eltolódással.
- Gondosan elő kell készíteni – szükség esetén megfelelő segédeszközök igénybevételével -, hogy a mázolási, valamint az előkészítő műveletek a környezetben más felületek, berendezési tárgyak stb. szennyeződését ne idézhessék elő.
A bevonatrendszerek rövid jellemzése
A szerkezeti anyagok felületén a több rétegű mázolással vagy egyéb úton kialakított bevonatot festékbevonat-rendszernek nevezik.
A bevonatrendszer kialakítását (amely a mázoló feladata) az alábbi tényezők befolyásolják:
- A környező korróziós tényezők (pl. hő, nedves, párás meleg, savas, lúgos, oldószeres stb. igénybevétel);
- a felület vagy alap fizikai, kémiai tulajdonságai (pl. porozitás, kémhatás stb.);
- a felület érdessége, egyenlőtlenségei;
- a szerkezeti anyag, ill. festék bevonati rendszer mechanikai igénybevétele (pl. hajlító, koptató, dinamikus stb.);
- a tárgy vagy szerkezet alakja, ill. rendeltetése (pl. nagyméretű beépített tetőszerkezeten beégető bevonatrendszer nem jöhet számításba);
- a festékbevonat-rendszerre vonatkozó egyéb különleges követelmények (pl. tisztíthatóság és színezés esztétikai vagy jelzési célzattal);
- a bevonatrendszer kialakításának egyéb helyi lehetőségei (pl. élelmiszeripari üzemekben mérgező hatású festékanyagokat még abban az esetben sem szabad használni, ha azok műszakilag a legelőnyösebb megoldást jelentenék);
- a bevonatrendszer kiválasztásának mindig az az alapvető szempontja, hogy azt, ill. az ahhoz szükséges festékanyagokat kell a felület és az igénybevétel körülményeihez alkalmazni, nem pedig fordítva.
A gyakorlatban a fenti körülmények előzetes mérlegelése után kiválasztott festékbevonat-rendszer felépítésének legfontosabb szempontja stabilitásának (állandóságának), tartósságának biztosítása.
A festékbevonat-rendszerek tartóssága (stabilitása) az alábbi követelmények kielégítésével biztosítható
- A festékbevonat-rendszer az adott mechanikai, vegyi, korróziós és egyéb igénybevételeknek a legteljesebb mértékben álljon ellen;
- az alap felülete és az alapozó festékbevonat közötti tapadás teljes (100%-os) legyen;
- az alap felületi rétegét kémiailag is stabilizálni (semlegesíteni) kell, úgy hogy az alap a festékbevonatra káros vegyi hatást ne fejthessen ki, és természetesen a festékanyag, ill. hígítószerei sem az alap anyagára;
- az egymás után következő festékrétegek sem felhordáskor, sem pedig a későbbiek folyamán egymásra káros hatással ne legyenek;
- az egyes festékrétegek egymással mechanikai és fizikai tulajdonságaik (pl. rugalmasság, hőtágulás, ütésszilárdság stb.) tekintetében is összeférjenek *(Megjegyzés lent!).
- a festékbevonat-rendszert (bizonyos mértékig a felület adottságaitól függően) egyenletes rétegekből kell felépíteni;
- a festékbevonat folytonossági hiányoktól mentes legyen. Minden kiálló szemcse, kihagyás stb. a bevonat leválását, meghibásodását előidéző sérülés kiindulóhelye lehet.
*Ennek érdekében az alábbi szempontokat kell érvényesíteni:
- az alaptól a bevonat külső felülete felé haladva az egyes festékrétegek mindig kötőanyagdúsabbak, ill. rugalmasabbak legyenek az alattuk levő réteghez képest (a hajlítási rugalmassággal mért 2. fokozatnak megfelelő eltérés esetén már repedezéssel, zsugorodással lehet számolni);
- a rugalmas alapozó vagy közbenső rétegben merev, rugalmatlan átvonó festékbevonatot nem szabad képezni (olajfestékalapra merev gyantalakk);
- a fényes, igen sima felületű alapozó vagy közbenső rétegre, matt, erősen túlpigmentált átvonó réteget felhordani nem szabad;
A festékbevonat-rendszerekre vonatkozó általános követelmények
A festékbevonatokat a már előzőkben megadott körülmények figyelembevételével választják meg. Minthogy a gyakorlatban igen sok tényező hatását kell mérlegelni, így az egyes bevonatrendszerekre vonatkozó követelmények is igen sokrétűek. Gyakran ellentétes követelmények is felmerülnek.
A festékbevonat-rendszerekkel szemben az alábbi általános követelményeket támasztják:
- adott – mechanikai, légköri és korróziós – igénybevételnek minél tovább, meghibásodás nélkül ellenálljon;
- a felületet vagy szerkezetet minél nagyobb mértékben védje a korróziós hatásokkal szemben;
- a bevonat védőhatása és élettartama (tartóssága) előállítási költségével arányos, azaz elhasználódási tényezője minél kisebb értékű legyen;
- az esztétikai – higiéniai és egyéb követelményeket – a bevonat elégítse ki;
- meghibásodás esetén a bevonat felújítása, javítása különleges nehézségekbe ne ütközzék.
Azt, hogy milyen mértékben képes a festékbevonat ezeket az általános igényeket kielégíteni, az alábbi, csoportokba foglalt követelmények vizsgálatával lehet értékelni.
Mechanikai követelmények
- Tapadás. A bevonat az alappal tartós kapcsolatot létesítsen.
- Kopásállóság. Különösen a dörzsölésnek, súrlódó, koptató igénybevételnek kitett bevonatok esetében jelentős (pl. padló-, parketta-lakkoknál stb.). A gyakorlatban nem mindig a keményebb bevonatok a kopásállóbbak.
- Ütésállóság (ütésszilárdság). Az a joule-ban kifejezett ütőmunka, amelyet a bevonat meghibásodás nélkül elvisel. Különösen a mechanikai igénybevételnek kitett szerkezetek festékbevonatának fontos követelménye.
- Rugalmasság, szívósság stb. Főleg az utólagosan, alakváltozással járó megmunkálás esetén fontos tulajdonság (pl. mázolt lemezek).
Fizikai, esztétikai követelmények
- Megjelenés. A festékbevonat egyenletes, folytonossági hiányoktól mentes legyen, kiálló szemcséket stb. ne tartalmazzon.
- Színárnyalat. Egyenletes, az előírt mintával egyező legyen. Ma már a színtartalmat szabványos színkoordinátákkal, számokkal írják elő, a fehérségtartalmat pedig százalékban pontosan meg lehet adni.
- Felületi fényesség. Számokkal jellemezhető vagy ajánlati (etalon) mintával való összehasonlítással értékelhető. A bevonat lehet fényes, zsírfényű vagy matt felületű.
- Keménység. A bevonat számokkal is jellemezhető tulajdonsága; elsősorban a kopás- és nyomásállóság szempontjából fontos követelmény.
- Rugalmasság (képlékenység, elasztikusság). A bevonat utólagos alakváltozásokkal szembeni viselkedésére jellemző. A rugalmas bevonatok a hő hatására bekövetkezett tágulást, összehúzódást sokkal inkább elviselik, mint a merevek, kevésbé rugalmasok.
- Elöregedési hajlam. A bevonat tartóssága szempontjából egyik legfontosabb követelmény. Összetett károsodási folyamat eredménye. Értéke különféle szabványos vizsgálati módszerekkel meghatározható. Az öregedési hajlamot általában a bevonat rugalmasságának csökkenése jellemzi.
- Porozitás (lyukacsosság). A festékbevonat lyukacsosságát fejezi ki. Minél nagyobb valamely bevonat porozitása, annál kisebb a védőhatása. A porozitás egyes festékbevonatok esetében (pl. falfestékeknél) fontos követelmény. Vízáteresztő képesség. Csökkent védőhatás mellett a bevonat meghibásodását (pl. hólyagosodását) idézi elő. Különösen fontos pl. víz alá merülő acélszerkezetek korrózió ellen védő festékbevonat-rendszereinél, hogy azok ne legyenek vízáteresztők.
- Víz-, gőz- és páraáteresztő képesség. Szintén a porozitással összefüggő jellemző, amely a falfestékek igen fontos követelménye.
- Duzzadást hajlam víz hatására. Különösen a kültéri vagy párás helyiségekben levő festékbevonatoknál fontos követelmény, hogy azok minél kisebb vízfelvevő képességűek és duzzadási hajlamúak legyenek.
- Hőállóság. A bevonat fontos jellemzője. Az öregedési hajlamot is hőkezeléses vizsgálattal lehet legegyszerűbben megállapítani.
Időállósági követelmények
Elsősorban a kültéri festékbevonatok esetében fontos szempont, hogy azok a légköri, klimatikus tényezők hatására milyen mértékben károsodnak. A természetes hatásokkal szembeni ellenállóképesség (vagy tartósság) értelemszerűen a viharállóságot is jelenti. A kültéri időállósági vizsgálat körülményeit szabványok írják elő.
A vizsgálat előnye, hogy az egyedüli megbízható eredményt adja a festékbevonatok kültéri időállóságára vonatkozóan. Hátránya viszont, hogy időben évekig elhúzódik. Éppen ezért összetett, gyorsított laboratóriumi ciklusvizsgálattal próbálják az eredményeket rövid időn belül kiértékelhetővé tenni.
Az alábbi vizsgálatokból a festékbevonatok kültéri időállóságára lehet következtetni.
- Napfényállóság (fényállóság). Azt fejezi ki, hogy a bevonat színárnyalata (esetleg felületi fényessége) napsugárzás hatására milyen mértékű, zavaró változást szenved.
- Kvarcfényállóság. Vizsgálata az adott teljesítményű higanygőzlámpa (kvarclámpa) megvilágítására bekövetkező szín- vagy egyéb elváltozást értékeli ki. Bevonatonként előírható, hogy hány órán át tartó sugárzás hatására nem változhatnak vagy fakulhatnak ki.
- Laboratóriumi ciklusvizsgálat. Pontosan előírt követelmények között elvégzett összetett, gyorsított vizsgálat. A ciklusok számából lehet következtetni arra, hogy a vizsgált festékbevonat kültéri igénybevételre használható-e, vagy sem.
Sajnos sem a szabványos kültéri, sem a laboratóriumi ciklusvizsgálat egyértelmű összehasonlítási alapját képező kiértékelési előírás nincs.
A festékbevonat-rendszer vegyi ellenálló képességére vonatkozó követelmények
E követelmények elsősorban a vegyi igénybevételnek kitett festékbevonatoknál fontosak. E csoporton belül általában az anyagok következő tulajdonságait szokták vizsgálni: vízállóság, sóoldatokkal szembeni ellenálló képesség, savállóság, lúgállóság, oldószerállóság. Aktív gázokkal, gőzökkel szembeni ellenálló képesség stb.
A vizsgálatok során a festékbevonat-rendszereket különböző hőmérsékleten és töménységű oldatokkal vizsgálják, és figyelik a bevonat károsodását. Ide sorolhatók természetesen a különféle gyakorlati vegyszerállósági próbák is, amelyeknek a bevonat használat közben is ki van téve (pl. mosószerállóság, ásványolaj-, benzinállóság stb.). A vizsgálatok körülményeit szabványok írják elő.
A festékbevonat gombásodásig penészesedési hajlamára vonatkozó követelmények
Adott körülmények között gyakran fontos követelmény lehet (pl. ebédlőkben, konyhákban, élelmiszeripari üzemekben stb.), az, hogy a festékbevonat gombásodásra, penészedésre ne legyen hajlamos. Ez a követelmény általában nedves, trópusi klíma hatásának kitett bevonatoknál csaknem mindig felvetődik.
A mázolómunkák előtervezési és munkaszervezési kérdései
A színdinamikai elvek műszaki jellegű hasznosítása
Mivel a mázolómunkák olyan jellegűek, hogy jelentős részük – a nagyméretű, egybefüggő falfelületekkel szemben – kisebb méretű (pl. nagyobb méretű felületekkel, elemekkel határolt épületszerkezetekre, berendezési tárgyakra, gépekre, járművek, ipari csarnokok szerkezetei, csővezetékekre, hídszerkezetekre stb.) a színdinamikai hatáskeltést a környezeti jellemzők fokozott figyelembevételével kell megtervezni. A mázolással, színes lakkozással és annak különféle változataival készült bútorok, belső berendezési tárgyak, gépi berendezések stb. felületképzése már az ipari formatervezés, belsőépítészet, lakásberendezés, kirakatrendezés önálló tevékenységi köreivel is közvetlen kapcsolatban áll.
A mázolás gyakorlati jelentősége
Az ipari üzemekben pl. a csővezetékek szabvány színben előírt mázolása, továbbá a biztonsági szín- és alakjelek stb. kifejezetten a munkavédelem, ergonómia, munkalélektan területét érintik. Érdemes megfigyelni, hogy a korszerű vegyipari, gépipari, könnyűipari, élelmiszerfeldolgozó ipari üzemek mázolt szerkezeti elemei, színes felületei színdinamikai összhatásukban nemcsak kedvező megjelenést, esztétikai benyomást keltenek, hanem a kellemes munkahelyi, „komfort érzetet” is, s ezáltal a munkakedvet növelő termelési tényezőként is hatnak.
A mázolás esztétikai jelentősége
Ugyanígy egy városkép, lakóépület, üdülőövezet stb. kialakításában, esztétikai formálásában is megkülönböztetett kifejező hatásúak a” nagy számban előforduló, tagoltabb mázolt felületek és épületszerkezetek, pl. nyílászáró szerkezetek, ajtók, ablakok, rácsok, ereszcsatornák stb. A mázolás elsősorban műszaki rendeltetésű állag-, ill. felületvédelem, de az esztétikai jellegű igények ezzel az alapvető követelménnyel mindenkor összehangolhatok.
A festékbevonat-rendszerek tervezése környezeti igénybevételre
Mivel a mázolásra vonatkozó elsődleges követelmény az állagvédelem (a szerkezeti anyagok élettartamának, tartósságának növelése), így indokolt a környezeti (károsító) hatások gondosabb felmérése, mint pl. falfestés esetén. Ezt az a körülmény is indokolja, hogy a mázolás sokkal többféle, egymástól erősen eltérő szerkezeti anyag védelmét érinti, mint a falfestés. így a korróziós folyamatok is sokkal szerteágazóbbak.
Elsősorban ez a magyarázata annak, hogy a környezeti hatások rendszerezését, körülhatárolását és ezek vizsgálatát egész sor szabványelőírás és műszaki irányelv szabályozza. A hétköznapi gyakorlatban a lakk- és festékbevonat-rendszerek lényegében a következő egyszerűsítettebb károsító fokozatoknak vannak kitéve, a rendeltetés szerinti igénybevételük során.
I. fokozat
Egyszerű, száraz beltéri igénybevétel.
II. fokozat
Nedves beltéri igénybevétel, +5-+60 °C közötti hőterhelés mellett, 100%-os relatív páratelítettségű légtérben, tartós páralecsapódás, fröccsenő víz hatásának van kitéve a bevonat.
III. fokozat
Egyszerű szabadtéri (kültéri) igénybevétel, -30-+40 °C léghőmérséklet, 50- 100%-os páratelítettségű légtér, tartós napsugárzás, légköri csapadékok (eső, köd, jég, hó stb.) mellett, poros, homokszemcsés áramló légtér koptató hatásának van kitéve a bevonat; legfeljebb kis szennyeződésű ipari légtérrel lehet számolni.
IV. fokozat
Szabadtéri vegyi igénybevétel. Környezeti hatások mint előzőnél, de kifejezett vegyi jellegű légszennyeződések (pl. S02, S03, H2S, H2S04, HC1, NH3, sók, lúgok, esetleg oldószergőzök, mechanikai – lebegő – szennyeződések stb.) mellett. (Vegyipari üzemek technológiai műveleteivel összefüggő környezeti szennyeződések.)
V. fokozat
Víz alá merülő szerkezetek lakk- és festékbevonatai. Pl. tengeri sós víz, ipari szennyvizek, zagyok, szenny vízderítők stb.
VI. fokozat
Mint előző, de élelmiszeripari követelmények mellett, azzal a feltétellel, hogy a festékrétegből károsító, mérgező vagy kellemetlen mellékízt adó alkotórészek tartós igénybevétel esetén sem oldódhatnak ki.
VII. fokozat
Hőigénybevétel, kétféle változatban:
- száraz hőigénybevétel: +80-+ 300 °C-os (esetleg +450 °C-ig) hőmérsékleten legfeljebb 35-50%-os pára telítettségű légtérben, nem kifejezetten vegyi szennyeződések esetén, páralecsapódás nem jöhet számításba;
- nedves hőigénybevétel +80-+ 300 °C-os hőigénybevételnél, 100%-os páratelítettségű légtérben, átmeneti vagy tartós páralecsapódás mellett.
VIII. fokozat
Különleges igénybevételek, az előbbi hatások kombinációja (pl. nedves vagy száraz szubtrópusi, tengerparti klíma), penészes baktériumtelepek stb. kifejezetten mikrobiológiai korróziója, mechanikai koptató hatás (pl. parketta lakkrétege), radioaktív és egyéb nagy energiájú sugárzás károsító hatása stb. Mindezek természetesen nem pontosan körülhatárolható, hanem egymást átfedő, együttesen vagy váltakozva érvényesülő környezeti igénybevételt képeznek, esetleg egyéb más károsító tényezőkkel kombinálódva.
A korrózió fogalma és a korróziós tényezők ismertetése
A korrózió a szerkezeti anyagok környezeti tényezők hatására bekövetkező károsodási folyamata. A korrózió legtöbbször több folyamat és kölcsönhatás eredménye. Ezért a korrózió megjelenési formája is igen sokféle lehet. A mázolással képzett festékbevonatok legfontosabb rendeltetése a szerkezeti anyagok védelme a környező károsító (korróziós) hatásokkal szemben. A legjobban ellenálló festékbevonat kialakításához ismerni kell a károsító tényezők festékbevonatokra gyakorolt hatását. A fontosabb korróziós jelenségek eredetük szerint négy csoportba sorolhatók.
Kémiai korrózió
A szerkezeti anyagoknak az anyagok vegyi egymásra hatására bekövetkezett káros átalakulása.
Ilyenek:
- rozsdásodás (pl. vasanyagokon, oxigén és víz hatására),
- patinaképződés (pl. rézanyagokon szén-dioxid és vízgőz hatására),
- reveképződés (a fémek hő hatására és következő oxidációja, pl. vas),
- füstgáz-korrózió (a füstgázok S02, S03, H2S, C02, vízgőz és egyéb szennyeződéseinek vegyi támadó hatására (pl. acél csővezetékeken),
- atmoszferikus korrózió (ipari légköri szennyeződések támadó hatása pl. vegyi üzemek közelében),
- vízgőz okozta korrózió (pl. csővezetékekben),
- savak, lúgok, sóoldatok stb. közvetlen támadó vegyi hatása,
- hidrogén okozta korrózió (a hidrogén az acélok elridegedését okozhatja, főleg magasabb hőmérsékleten, hidrogénridegség),
- talaj korrózió (a talajban levő hatóanyagok pl. humuszsavak stb. szerkezeti anyagokat károsító, vegyi hatása),
- fázishatár-korrózió (az egyes közegek határfelületein kialakuló korrózió, pl. vízfelszín közelében levő fémszerkezet).
Elektrokémiai korrózió
A szerkezeti anyagok érintkezésénél, helyi galvánelem képződés következtében, létrejött elektrokémiai folyamatok károsító hatása.
Ezek:
- galvánelem képződés (elektrolit, pl. víz, sósavoldat stb. jelenlétében egyes fémek között, elektród-potenciálkülönbség hatására, elektromos áramlás indul meg, s az egyik fém oldatba jut, pl. vas-cink, vas-ón, vas-réz stb. érintkezésénél);
- kontakt korrózió (az egyes fémek tartós érintkezése közben az egyik fém teljes károsodást szenved, pl. vas-alumínium);
- kristályközi korrózió (fémek és fémötvözetek kristályszemcséinek ha-tárfelületein, esetleg külső vegyi vagy helyi galvánelem-képződés hatására bekövetkező káros átalakulás);
- szelektív korrózió (a fémötvözetekből az egyik alkotórészt oldja ki a támadó közeg; pl. sárgarézből a cink gyakran eltávozik korróziós hatások következtében),
- kóboráram okozta korrózió (kóboráram hatására bekövetkező, elektrolízishez hasonló, káros elektrokémiai folyamat),
- sugárzási korrózió (radioaktív és egyéb nagy energiájú sugárzások hatására fémötvözetek kristályrácsaiban káros átrendeződés indul meg).
Biológiai korrózió
Az egyes szerkezeti anyagok növényi, állati élőszervezetek életműködése következtében beálló káros átalakulása.
Ilyenek:
- baktériumok okozta korrózió (baktériumok, baktériumtelepek, pl. fa falszerkezeteken okozott károsító hatása);
- gombák, penészgombák okozta korrózió (főleg a fafelületeket károsítják életműködésük során, pl. reves korhadás);
- növények okozta korrózió (pl. a borostyán és egyéb futónövények meg-telepedése fa falfelületeken jelentős károsodást okozhat);
- rovarok és egyéb élősdiek okozta korrózió (pl. fa falfelületek szuvasodása stb.).
Mechanikai és egyéb korrózió
Szerkezeti anyagok mechanikai és dinamikus erők hatására történő károsodása.
Ezek:
- dörzskorrózió (az egymással érintkező fémrészek felületein a gyakori elmozdulás, pl. rezgések hatására bekövetkező káros helyi roncsolódás);
- erózió (áramló gázok, gőzök és a bennük lebegő szilárd alkatrészek mechanikai koptató hatása, pl. a szél, ill. levegő+porszemcsék koptató hatása);
- abrázió (áramló folyadékok és a bennük lebegő szilárd alkatrészek mechanikai koptató hatása, pl. folyóvízben lebegő homokszemcsék koptató hatása);
- kifáradási korrózió (váltakozó mechanikai igénybevételnek, rezgésnek stb., esetleg egyidejűleg vegyi hatásnak kitett szerkezetek károsodása);
- feszültségi vagy cr-korrózió (fémek hideg alakítása vagy hegesztése közben kialakult, belső húzófeszültségek hatására keletkező, főleg repedések alakjában jelentkező, káros szerkezeti változások),
- kapilláris vagy réskorrózió (üregekben, illeszkedési hézagokban keletkező jellegzetes károsodási folyamat).
Bár a korrózió folyamata fémeknél jobban elhatárolható, általában más szerkezeti anyagok károsodását is korróziónak nevezik.
A korróziós károk megelőzésének és csökkentésének szerepe
Ez nemcsak gazdasági, hanem műszaki, sőt biztonságtechnikai kérdés is. Ugyanis nemcsak a szerkezeti anyag közvetlen károsodása jelentős, hanem gyakran ennél nagyobb lehet a szerkezeti korrózióra visszavezethető károsodása, tönkremenetele.
Pl. súlyos korrózió esetén egy acél tartószerkezet teljes tönkremenetelekor más berendezések (pl. gépek) is károsodhatnak, és ilyenkor baleseti veszélyforrással is számolni kell. Jelentős károsodást okozhatnak a korróziós képződmények a kész termékek elszennyezésével is (pl. vegyipari berendezéseknél, gyógyszergyártásnál stb.).
A korróziós károk megelőzésére jelenleg az alábbi megoldások használatosak
- ellenállóképes szerkezeti anyag kiválasztása, védő, ellenállóképes fémbevonat kialakítása (tűzi úton, fémszórással, galvanizálással vagy egyéb úton);
- a felületen szilikát zománcbevonatok kialakítása, filmképző, festékbevonat-rendszerek képzése;
- a felület kémiai stabilizálása (pl. eloxálás, pácolás stb.);
- katodikus vagy anodikus védelem, korróziógátló inhibitorok felhasználása, egyéb különleges megoldások segítségével.
A fontosabb korróziós tényezők hatásmechanizmusa
A légköri vagy klimatikus tényezők
Lényegében az időjárásra jellemző levegő állapotát kialakító fizikai sajátosságok. Ezek bizonyos határértékeken belüli átlagos vagy szélső értékei alapján klímaterületeket (égöveket) különböztetnek meg (így pl. hideg, mérsékelt, trópusi nedves, trópusi száraz, magaslati klímaterületek stb.).
A levegő hőmérséklete
Igen széles határértékek között változik. Hazánkban, tehát a mérsékelt égöv alatt is -30-+40 °C-os hőmérséklet-ingadozással lehet számolni. A hőmérséklet-ingadozás, különösen a hirtelen hőmérsékletváltozás a festékbevonatok elöregedését, rugalmasságának csökkentését idézi elő. Itt jelentős az alap pórusaiban levő vízgőz és levegő hőingadozás hatására történő kiterjedése és összehúzódása, ami a festékbevonat-rendszert lefeszíteni igyekszik.
Kellően nem telített pórusú felületről a festékbevonat gyorsan leválik. A gyakorlatban a festékbevonat, a hőelnyelés miatt, lényegesen jobban felmelegszik, mint a léghőmérséklet. így pl. egy fekete (tehát hőelnyelő) festékbevonat felülete 30 °C-os léghőmérsékleten 60-65 °C-ra is fölmelegedhet.
Páratartalom
Egyes festékbevonatokra (pl. olajfestékekre) különösen káros, mert duzzadásukat idézi elő, s ez gyakran a bevonat folytonosságának megbontásához (hólyagosodás, repedezés stb.) vezethet. A bevonat alá került nedvesség vízgőz alakjában vagy fagy hatására szintén a bevonat leválását, fel-hólyagosodását okozza.
A napsugárzás, kozmikus sugárzás
Rendkívül roncsolja a festékbevonatokat. A nagy energiájú kozmikus sugárzás bármely rétegvastagságú festékbevonaton áthatol, míg a napsugarak (az ultraibolya sugárzás tartománya) főleg a színtelen lakkokat és a sötét színárnyalatú bevonatokat károsítják, elöregedésüket okozzák. A fotokémiai aktivitás egyes pigmentek (pl. titánfehér és szerves pigmentek, horganyfehér és párizsi kék stb.) kifakulását, színváltozását idézi elő.
A légmozgás (szél)
Ezeknek a károsító hatása is jelentős, bizonyos körülmények között, így pl. orkánszerű viharos szél esetén (18-35 m/s szélsebesség) néha tekintélyes tömegű (0,1-20 g) éles homokszemcsék vagy jégdarabok ütődnek a festékbevonatok felületére.
Vegyi jellegű korróziós tényezők
Ide tartoznak az ipari környezet (újabban a nagyvárosi légkör) gáz-, gőz-, folyadék és szilárd halmazállapotú vegyi szennyeződések.
Széntüzelésű berendezések, járművek üzemeltetése során a levegőbe tekintélyes mennyiségű kén-dioxid, kén-hidrogén kerül, amelyek végső oxidációs termékként kénsavvá alakulnak, és károsító hatást fejtenek ki a festékbevonatokra. Egyes festékbevonatokra (pl. horganyfehér-tartalmú olajfestékek) még a kevésbé agresszív szén-dioxid is károsító hatású lehet.
Jelentős a légköri szennyeződés vegyipari üzemek területén vagy közvetlen környezetében, ahol erős savas, lúgos hatású gőzök, gázok és szilárd lebegő alkatrészek (sók, hamuk stb.) kerülhetnek a levegőbe, amelyek egy helytelenül kiválasztott festékbevonat-rendszer teljes tönkremenetelét okozhatják.
Mechanikai tényezők
Szintén jelentős hatásúak a koptató igénybevételnek kitett festékbevonatok tartósságában. Ilyen mechanikai hatásnak vannak kitéve a folyadékokat szállító csővezetékek, reaktorok, silók, vegyipari berendezések, de pl. a padlólakkok és zománcok is.
Biológiai károsító tényezők
Közülük meg kell említeni a festékbevonatokon megtelepedő gomba-, penész-, baktérium- stb. képződményeket és egyéb élősdieket, amelyek pl. trópusi környezetben nem egy alkalommal a festékbevonatok igen gyors tönkremenetelét idézték elő.
A festékbevonat rendszer és az alap vagy a különböző festékrétegek közötti egymásrahatás révén keletkező károsodás
Ilyen pl. az alumínium felületére felhordott higany tartalmú pigment vagy lúgos hatású, falfelületen nem lúgálló festékbevonat kialakítása stb.
Különleges károsító tényezők
Ezek közé tartozik pl. a radioaktív sugárzások roncsoló hatása, amelyek a kozmikus sugárzáshoz hasonlóan hatnak.
A mázolómunkák terminológiája
Lényegében a mázolással azonos elvű és felépítésű korrózióvédelmi eljárás, ill. szakmai tevékenység a fényezés (szórófényezés, dukkózás, szórólakkozás stb.), ami javarészt a gépkocsik karosszériájának védelmére korlátozódik. Mivel munkaműveletei valamelyest eltérnek a mázoláséitól, ill. a fényezést kizárólag szóróeljárással végzik, ezt a tevékenységet külön szakmai képesítéshez kötik.
Ide tartoznak pl. a beégetős típusú (azaz hőkezeléssel képezhető) bevonat-rendszerek (pl. zománcfesték, kalapácslakk – helyesebben zománc – stb.).
Mázolómunkák – Mi a helyzet e téren itthon?
Általános kérdések
A különféle szerkezeti anyagoknak a környezeti támadó tényezők hatására bekövetkezett károsodása (korróziója) világszerte jelentős anyagi értéket képvisel. Hazánkban az évenként keletkező korróziós károkat mintegy 2,5-3,0 milliárd forintra becsülik. A megelőző jellegű korrózió elleni védelemre fordított költségek ennek többszörösét teszik ki.
A szinte áttekinthetetlenül nagyszámú felületvédelmi eljárások (pl. galvanizálás, tűzi horganyozás, ónozás, zománcozás, foszfátozás stb.) közül még mindmáig a lakkokkal, festékbevonatokkal végzett védelem, a mázolás (festés) a legelterjedtebb, még fémes szerkezeti anyagok esetében is.
Újabban ennek korszerűsített változatai, így pl. a beolvasztásos műanyagbevonat (szinterezés), beégetéssel vagy hideg úton készült vastagbevonatok is egyre nagyobb tért hódítanak. A korrózió elleni, ill. állagvédelem egyre terjedő, költségesebb, de jóval hatékonyabb megoldása pl. a faszerkezetek – mázolást, további felületvédelmet nem igénylő – műanyagszerkezetekkel való helyettesítése, vagy a rozsdásodó acélszerkezetek korrózióálló acélokkal, alumíniumszerkezetekkel való helyettesítése.
Mi a helyzet e téren itthon? – Történelmi kitekintés
Hazánkban az összes felületvédelmi eljárások közül csak a mázolás mintegy 60-65%-ot tesz ki. Egy új lakóház összes építési költségének – a végleges elhasználódásig szükséges karbantartási költségeket figyelembe véve – a mázolás (lakkozás, festés) mintegy 12-18%-a. Annak ellenére, hogy a mázolással (lakkozással) végzett felületvédelem több ezer éves (!) múltra tekint vissza, tudományos alapon való vizsgálatára, ill. továbbfejlesztésére csak az utóbbi évtizedekben (mintegy 90-100 éve) került sor. A korróziós folyamatok megfelelő tudományos vizsgálata pedig még rövidebb múltú.
Egy festékbevonat-rendszer hatékonyságát (élettartamát) legalább 25-30-féle tényező befolyásolja
A hatékony és eredményes felületvédelemben ezek ismerete, helyes kombinációja sokkal fontosabb, mint a kézügyességgel összefüggő tevékenység (bár ez sem lebecsülendő). A mázolási munkák népgazdasági szempontból való eredményességét nem a termelési érték jellemzi elsősorban, hanem az a körülmény, hogy minél később kerül sor a felújításra, lehetőleg hiánypótlási és garanciális munkák nélkül.
Nehézségek a szabványok hiányossága miatt
Hátrányosan érezteti hatását az a körülmény is, hogy a hazai (és import) festék gyártmányok, korrózióvédelmi anyagok tartósságát (élettartamát) adott bevonatrendszer és környezeti hatások függvényében nem rögzítik anyagszabványok vagy egyéb műszaki előírások, sőt még az EMI által kiadott ún. műszaki alkalmassági bizonyítványok sem utalnak erre az alapvetően fontos jellemzőre!
Ennek hiányában pedig a korrózió elleni védelmet megtervezni (mintegy igénybevételre méretezni), eredményességét, népgazdasági hasznosságát tervszerűen kiszámítani eleve lehetetlen. Ilyen körülmények között pedig a lelkiismeretesen megtervezett és kivitelezett mázolási munka is bizonytalan kimenetelű kísérletezésnek tekinthető, amely a jelenlegi műszaki ismeretek színvonalán nem engedhető meg.
A helyzet nem könnyíti meg a kivitelezők helyzetét sem
Ez a tény meglehetősen visszás helyzetet teremt a minőség terén vállalt társadalmi (és jogi) felelősség vonatkozásában is. Ugyanis a kivitelező építőipari vállalatoknak, szövetkezeteknek, kisiparosoknak olyan festékbevonat-rendszerre (mázolási, lakkozási munkára) kell, kültéri igénybevétel mellett – az újabb rendelkezések szerint már nem három, hanem öt év – szavatossági kötelezettséget vállalni, amely tartósságát semmiféle előírás vagy törvényes rendelkezés nem szavatolja!
Több példát lehetne idézni olyan festékek széles körű bevezetésére – anélkül, hogy tartóssági jellemzőiket ismerték volna -, amelyek több száz milliós Ft összegű népgazdasági kárt okoztak. A festékeket ugyanis nem az adott rendeltetési célra propagálták.
A kivitelezés területén is elég sok a hiányosság
Ez gyakran már a tervezésnél kezdődik, ahol helytelenül a festékbevonat-rendszert kizárólag minél kisebb egységára szerint választják ki. Egy festékbevonat-rendszer gazdaságossága független az egységárától, hiszen azt az elhasználódási tényezője: az egységár és élettartam hányadosa jellemzi. Ebből következik, hogy általában a nagyobb tartósságú bevonatrendszer gazdaságosabb. A kivitelező vállalatoknak az az érdeke – elsősorban tervteljesítés szempontjából -, hogy minél nagyobb egységárú bevonatrendszert készíttessen a megrendelő.
Erre – a kedvezőbb tartósság reményében – gyakran sor is kerül. Ez vezet aztán az olyan visszás helyzetekhez, hogy pl. egy vegyileg ellenállóképes festékbevonat-rendszer kerül kültéri igénybevételre – természetesen igen kedvezőtlen tartóssággal -, ahol egy olcsó olaj festék-bevonattal sokkal nagyobb időállóság lett volna biztosítható. Gyakran nem veszik figyelembe a felület, a környezet és a festékanyag kölcsönhatását, amely pedig a műszakilag megalapozott kivitelezés alapja.
A mázolómunkák tárgyköre
„Mázoláson” vagy „mázolómunkákon” azt a felületvédelmi eljárást, egyben azon munkaműveletek összességét értjük, amelyek során a különféle szerkezeti anyagok, használati tárgyak állagát a felületükön képzett folytonos, filmszerű védőréteggel (lakk- vagy festékbevonat-rendszer) védjük a környezet károsító hatásai ellen. A mázolás, a mázolási munkák tehát nemcsak kizárólag a festékanyagok felhordását jelentik, hanem magukban foglalják a felület előkészítését (pl. rozsdamentesítését, passziválását, tisztítását stb.) és az egyéb munkafolyamatokat is.
A szakmai gyakorlatban a mázolási munkák célja:
- a felület védelme a környezet károsító (korróziós) hatásaival (pl. nedvesség, napsugárzás vagy szennyezések stb.) szemben, egyszóval állagvédelem;
- díszítő hatáskeltés;
- a felület tisztításának, karbantartásának stb. megkönnyítése;
- különleges műszaki vagy egyéb követelmények kielégítése.
Mivel elsősorban a környezeti hatásokhoz és a felület adottságaihoz, tulajdonságaihoz kell a legalkalmasabb bevonatrendszert kialakítani, amely bizonyos mértékig a mázolás technológiai lehetőségeit is meghatározza, a továbbiakban ezt tárgyaljuk.